Dynabrade 13450 Handbuch für Sicherheit, Betrieb und Wartung - Seite 6
Blättern Sie online oder laden Sie pdf Handbuch für Sicherheit, Betrieb und Wartung für Werkzeuge Dynabrade 13450 herunter. Dynabrade 13450 8 Seiten. 1hp right-angle. governor controlled 2,800 rpm and 2,800 rpm, versatility kit
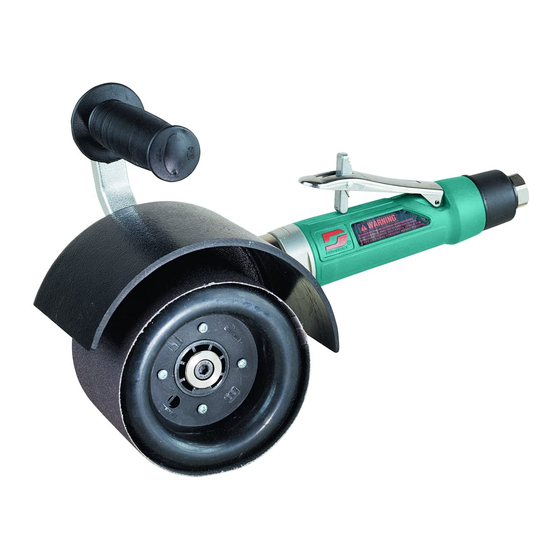
Important: Manufacturer's warranty is void if tool is disassembled before warranty expires.
Please refer to parts breakdown for part identification.
Motor Assembly:
Important: Be sure parts are clean and in good repair before assembling. Follow grease, oil and torque specifications.
1. Place rotor into a padded vise with gear teeth or male thread facing upwards.
2. Slip 51927 Spacer over rotor shaft and down against rotor body face.
3. Press 96441 Pin into 51922 Front Bearing Plate. Make certain, coiled pin does not protrude beyond internal bearing surface.
4. Place a .002" shim into the base of 51922 Front Bearing Plate as an initial spacing and slide 54520 Bearing to the front plate base. Note: 51951 Shim Pack contains
001" and .002" shims.
5. Press Bearing/Bearing Plate assembly onto rotor.
6. Check clearance between rotor and front bearing plate by using a .001" feeler gauge. Clearance should be between .001" – .0015". Adjust clearance by repeating steps
4 and 5 with different shims if necessary.
7. Once proper rotor gap clearance is achieved, install well lubricated 51926 Blades (4) into rotor slots. Dynabrade recommends lubricating blades with 95842 Air Lube.
8. Install 51925 Cylinder over rotor and front plate raised boss. Align coiled pin on front plate to cylinder slot.
9. Press 96441 Coiled Pin into blind hole on 51923 Rear Bearing Plate. Press (2) 96445 Coiled Pins into the back side of rear bearing plate.
10. Peel backing off 51924 Gasket and apply it firmly in place onto 51923 Rear Bearing Plate.
11. Place 51923 Rear Bearing Plate over rotor mandrel and insert raised boss on rear bearing plate into cylinder diameter, while inserting short coiled pin into cylinder slot. Be
sure inlet slot on rear bearing plate line up with inlet slot on cylinder. To correct alignment flip cylinder end to end and repeat steps 8 & 9 for correct assembly.
12. Using 96243 Bearing Press Tool (ordered separately) press 02057 Bearing onto rotor and into 51923 Rear Bearing Plate hole until it is seated. Important: While pressing
02057 Bearing, make certain to contact the inner race of bearings only. Cylinder must fit snug between bearing plates. If too tight, rotor will not turn freely. Rotor must be
lightly tapped at press fit end until rotor spins freely while still maintaining a snug fit. A loose fit will not achieve the proper preload on motor bearing. While pressing 02057
Bearing, make certain to contact inner race of bearing.
13. Add one drop of Loctite
®
243 (or equiv.) to governor assembly male thread and screw governor assembly into place (Left Hand Thread) with slotted screw head.
Torque to 2 N•m (18 lb.-in.).
14. Install motor assembly into housing, making sure motor seats all the way into housing. Note: Align both 96445 Pins to slots in insert and against 51924 Gasket.
Motor Assembly Complete.
Planetary Gear Casing Assembly:
1. Install 53665 Ring Gear over 54520 Front Motor Bearing, keeping 2 slots facing outward.
2. Install gears with needle bearings on retainer shafts and assemble shaft assembly onto planetary carrier by pressing retainer shafts into place.
3. Place 96498 Wavy Washer at the base of 53695 Gear Casing female threaded end.
4. Slide planetary carrier assembly, with threaded end first, into 53695 Gear Casing and through 54520 Bearing.
5. Apply one drop of Loctite
®
#243 (or equiv.) to threads of 51935 Coupling. Secure planetary carrier using 53698 Wrench (order separately) and thread on 51935 Coupling
(twist clockwise). Torque to 17 N•m (150 lb.-in.).
6. Install 53665 Ring Gear over 54520 Front Motor Bearing, keeping 2 slots facing outward.
7. Apply a small amount of Loctite
rotor spline into planet gears to allow carrier to spin freely.
8. When slots from ring gear line up with set screw hole, apply a small amount of Loctite
ring gear in place.
9. Torque 53695 Gear Casing to 35 N•m (310 lb.-in.).
Motor Assembly Complete.
Right Angle Head Assembly:
1. Apply a small amount of Loctite #680 to the top of flange on 53649 Gear Oil Plate and press 01041 Gear Oil Fitting into 53649 Gear Oil Plate and insert sub-assembly
into right angle housing.
2. Press 96325 Bearing into housing until it is firmly seated against 53649 Gear Oil Plate. Important: While pressing 96325 Bearing, make certain to contact outer race
of bearing only.
3. Add one drop of Loctite
®
#243 (or equiv.) to male thread of 53635 Pinion Adapter and tighten pinion using a 3/16" Hex Key wrench and the pinion wrench flats.
Torque to 17 N•m (150 lb.- in.).
4. Using 96244 Bearing Press Tool (ordered separately) press 53635 Pinion Adapter into 01266 Bearing. Important: While pressing 01266 Bearing, make certain to
contact inner race of bearing only.
5. Add one drop of Loctite
®
#243 (or equiv.) to male thread of adapter and tighten 51935 Coupler using wrench flats. Torque to 17 N•m (150 lb.- in.)
6. Insert sub-assembly into male threaded end of 53600 Right Angle Housing.
7. Apply a small amount of Loctite
8. Place 51936 Coupling Insert into 51935 Coupling. It is very important to match the radii of the 51936 Coupling Insert to the radii of the 51935 Coupling. If the radii do
not match, remove and rotate the coupling insert 90˚.
9. Secure 53600 Right Angle Housing, against both side handle bosses, in a padded vise.
10. Rotate motor housing/gear casing and 53650 Lock Ring until throttle lever is located between the 9-11 o'clock position. Torque lock ring to 35 N•m (310 lb.-in.).
11. Place well lubricated 53608 Wick against 96325 Bearing with flat edge towards pinion gear. (Wick must be completely saturated with Dynabrade 95848 Gear Oil before
installation). Note: Do not contaminate wick with any other oil or grease product.
12. Press 97679 Bearing onto spindle and against shoulder. Important: While pressing 97679, make certain to contact inner race of bearing only.
13. Press gear, with teeth facing away from bearing, into spindle and against 97679 Bearing inner race.
14. Insert spindle assembly into 53600 Right Angle Housing until 97679 Bearing contacts housing shoulder.
15. Rotate spindle while pressing down into housing to check for gear alignment and backlash. Install shims as required (minimum backlash is recommended for maximum
gear life. Make certain there is clearance throughout 360˚ revolution).
16. Press 50899 Seal into 50963 Retainer with base of seal facing outward.
17. Apply a small amount of Loctite
18. Using 97782 Pin Wrench (ordered separately) or an adjustable pin wrench, torque retainer to 35 N•m (310 lb.-in.).
Right Angle Head Assembly Complete.
Tool Assembly Complete. Please allow 30 minutes for adhesives to cure before operating tool.
Important: Before operating, place 2-3 drops of Dynabrade Air Lube (P/N 95842) directly into inlet with throttle lever depressed. Operate tool for 30 seconds to allow air lube to
properly lubricate internal motor components. Motor should now be tested for proper operation at 90 PSIG max. If tool operates at a higher RPM than marked on the tool or if
vibration and sound levels seem abnormal, the tool should be serviced to correct the cause before use.
Assembly Instructions -
®
#567 (or equiv.) to male thread of motor housing and thread 53695 Gear Casing over ring gear and onto motor housing. Important: Align
®
#567 (or equiv.) to 53600 Right Angle Housing thread, and install 53650 Lock Ring (Left hand Threads).
®
#567 (or equiv.) to the male thread of the retainer and thread into place. (Left Hand Thread)
(Continued)
®
#567 (or equiv.) to male thread of 04014 Set Screw, and install set screw to lock
6
Loctite
®
is a registered trademark of Loctite Corp.