Clarke PP15ND Manual de funcionamiento y mantenimiento - Página 7
Navegue en línea o descargue pdf Manual de funcionamiento y mantenimiento para Compresor de aire Clarke PP15ND. Clarke PP15ND 10 páginas. Air compressor
También para Clarke PP15ND: Instrucciones de uso y mantenimiento (17 páginas), Instrucciones de uso y mantenimiento (20 páginas)
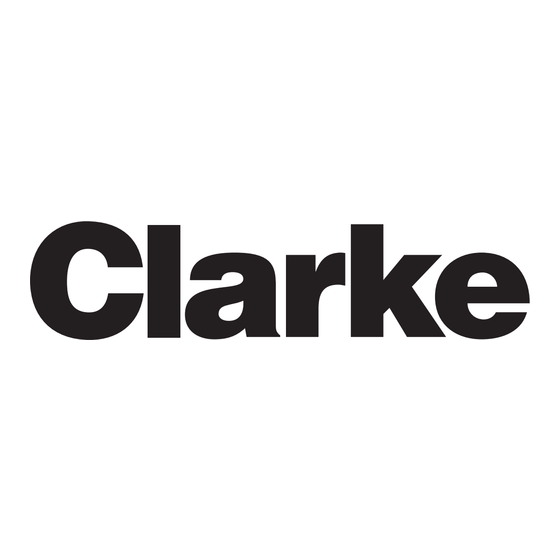
TROUBLE SHOOTING CHART
IMPORTANT
1. Any remedial work that may be required must be carried out by a qualified engineer.
2. Switch off the engine before removing any parts from the compressor.
3. Drain the Air Receiver before dismantling any part of the compressor unit's pressure system.
4. If your compressor develops a fault do not use until the fault has been rectified.
5. For troubleshooting the engine, refer to the engine manual.
SYMPTOM
PROBABLE
Engine difficult to
Load Genie leaking
start
(compressor unit is on load
during start).
Non-return valve blocked,
possibly frozen up.
Pressure switch defective.
Compressor unit
constantly 'on load'
Pressure switch set at a
pressure higher than the
safety valve's opening
pressure.
Bleed valve under
Load Genie leaking.
pressure switch blows
whilst compressor is
not running.
Bleed valve under
Load Genie leaking.
pressure switch blows
whilst machine is
running.
Compressor constantly
Suction filter blocked.
'on load' and cannot
Leak between compressor
attain the working
block and air receiver leaks in
pressure required.
or near air receiver.
Valves blocked by dirt, paint,
dust or choked up.
Inspection cover or plug
leaking.
CAUSES
REMEDY
Stop engine and empty air
receiver. Clean or replace
Load Genie
Thaw Load Genie out (Unit must
be installed in frost-free place).
Have pressure switch changed
by an electrician.
Adjust pressure switch or safety
valve.
WARNING: DO NOT ADJUST
SAFETY VALVE ABOVE MAXIMUM
WORKING PRESSURE DETAILED.
CleanLoad Genie or replace.
Clean Load Genie or
change pressure switch.
Change filter.
Tighten connection and repair
leak.
Clean or change valves.
Empty air receiver and
change seal.
- 14 -
PREPARATION FOR USE
A. Environmental
•
Ensure the compressor is sited on a firm level surface.
•
Ensure the environment is dry and dust free.
•
Ensure there is adequate ventilation for:
a) Air intake to compressor
b) Cooling for compressor pump
c) Engine exhaust gases.
B. Engine
Check oil and fuel levels and a visual check of components. Refer to engine service manual.
C. Pump
•
Check oil level on the Dipstick - to level marked.
D. Fuelling
Fill with unleaded petrol, according to the instructions within the engine manual.
•
Ensure the fuel tap is set to the required position.
•
Ensure The fuel hose and connectors are intact, in perfectly serviceable
condition and there is no leakage.
Note : Always use a funnel to fill the fuel tank so as to avoid accidental spillage of
fuel. If fuel is spilled it must be removed from the unit and surrounding area, before
attempting to start the engine.
E. Receiver
•
Drain off any condensate, by opening the drain cock (see Fig. 1). Remember
to close the cock when completed.
NOTE: This should be carried out DAILY when the compressor is in constant use.
F. Air Hose & Air Tool
•
Attach the air hose to the outlet using an appropriate connector.
NOTE: Quick fit nuts are provided. These may be removed if a 1/4"BSP is required.
•
Attach the air tool/spray gun to the air hose...If using snap couplings, use
a whip end, available from your Clarke dealer.
!
- 7 -