Doepke 09114892 Manual de instalación y funcionamiento - Página 2
Navegue en línea o descargue pdf Manual de instalación y funcionamiento para Disyuntores Doepke 09114892. Doepke 09114892 2 páginas. Residual current circuit-breakers
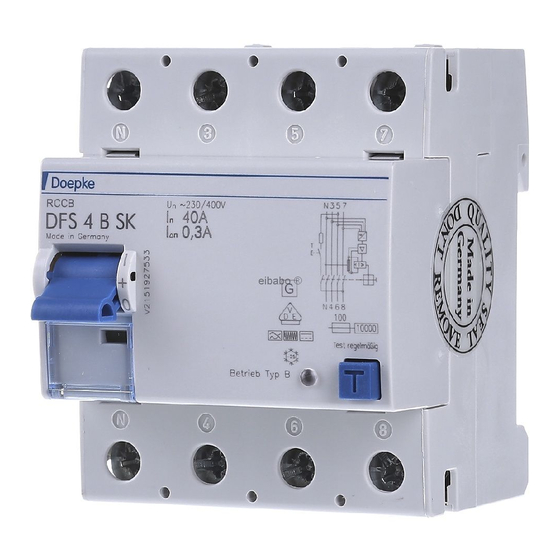
DE EN
Installation and Operating Manual
residual current circuit-breakers of series
DFS 4 B SK / F60 / V500 /
V500 F60 / S / S V500
Installation position
Any installation position may be used.
Intended use and mounting
By snapping onto top-hat rail and for installation in distribution boards with com-
pliant covers for preventing direct contact with hazardous live parts.
Electrical connection
Guide all active conductors and outer cables (L1, L2, L3 and the neutral conduc-
tor MP/N) through the switch. When doing so, pay attention to the energy flow
direction, i. e., the input terminals are 1, 3, 5, 7, the consumer system side is 2, 4,
6, 8. Scrape and grease aluminium conductors immediately before connection.
Function and area of application
The residual current circuit-breakers of the DFS 4 B SK model ranges are AC-
DC sensitive residual current circuit-breakers for detecting Type B residual cur-
rents. These devices are designed for use in single- and multi-phase mains
systems. They are not intended for use in DC networks. They consist of a mains
voltage-independent part for detecting sinusoidal AC and pulsating DC residual
currents with a rated frequency of 50 Hz (rated frequency of 60 Hz with se-
ries F60), as well as a mains voltage-dependent part for detecting residual cur-
rents within a frequency range of 0 Hz to 100 kHz.
In order to ensure protection in the event of indirect contact with a maximum
touch voltage of 50 V resp. 25 V across the entire covered frequency range, the
earth resistance must be < 167 Ohm resp. < 83 Ohm, when a residual current
circuit-breaker with a rated residual current < 300 mA is used. When using re-
sidual current circuit-breakers with a rated residual current of 500 mA, the earth
resistance must be < 100 Ohm resp. < 50 Ohm.
For frequencies > 1 kHz the tripping current for a DFS 4 B SK is below 2 A. This
means that highest possible system availability is ensured in this frequency
range, within which the usual switching frequencies of frequency converters
are located.
Testing and functional check
An insulation test of the user equipment is to be carried out in accordance with
DIN EN 61557-2. This may only be done when the device is switched off. Insula-
tion testing when the device is switched on or insulation testing on the input side
may lead to incorrect measured values. A functional inspection of the residual
current circuit-breaker itself is possible with connected mains voltage by press-
ing the test button T and, as in commercial use (BGV A3), should be carried
out at least every six months in the case of stationary systems and should be
repeated every working day in the case of non-stationary systems.
The green LED signals that the internal operating voltage is sufficient for AC-
DC sensitive residual current detection (residual currents of type AC, A and B).
If the LED does not illuminate, then only tripping via type AC and A residual
currents is still guaranteed. The internal supply of the DFS 4 B SK is carried out
via the terminals 1, 3, 5, 7. At least two arbitrary conductors must conduct AC
voltage of greater than 50 V in order to guarantee residual current detection that
is sensitive to all currents.
Important information on operation with electronic equipment (such as
frequency converters, inverters etc.)
1. Electronic equipment and its associated EMC protective provisions, such
as e. g. integrated or in series-connected EMC filters, as well as shielded
cables, can give rise to high capacitive leakage currents.
2. The maximum number of items of electronic equipment connected down-
stream of the DFS 4 B SK is based on the level of leakage currents that
occur. Excessive discharge currents may lead to undesired tripping in spite
of the special release frequency response. Relevant information concerning
the discharge currents that are produced can be requested from the manu-
facturers of the electronic equipment.
3. During operation with frequency converters long, shielded motor cables
may lead to high discharge currents in the event of the controller release
of the frequency converter, which lead to undesired tripping. If necessary,
a sinusoidal output filter should then be used directly behind the frequency
converter (before the shielded motor cable).
4. When switching on and off electrical systems with electronic equipment, it is
possible that very high surge leakage currents will be produced, which will
lead to tripping in the event of an appropriate duration. In order to keep the
processes for switching on and off as short as possible, the electrical system
should not be switched on with the DFS 4 B SK. Quick-switching, all-pole
contactors or switches with stored energy operating mechanisms are suit-
able (manual rotary switches should not be used).
3930212 | 05/2013
5. According to the instructions, a conventional 3-conductor EMC filter should
only be connected in series with the relevant electronic equipment. So
that the filter effect is not impaired, under no circumstances should further
single-phase consumers such as incandescent bulbs be connected on the
output side of the EMC filter.
6. As a rule, different clock frequencies (chopper) can be selected in the case
of electronic equipment. In an unfavourable case, the clock frequency may
lead to a tendency to oscillation in an upstream EMC filter and therefore
to greatly increased leakage currents, which then result in a tripping of the
DFS 4 B SK. In this case, the clock frequency must be changed.
7. Frequency converters with an integrated EMC filter often only allow a maxi-
mum length of the shielded motor cable of 5 to 10 m. Longer cable lengths
lead to greatly increased discharge currents and to the ineffectiveness of
the integrated EMC filter. The manufacturer's specifications must always be
observed for the frequency converter.
Application instructions and warnings
The following notes and warnings must be observed in order to ensure safe
operation:
1. Installation may only be carried out by an authorised specialist, who is famil-
iar with the relevant national installation regulations.
2. Without any additional protective housing, residual current circuit-breakers
should only be stored and operated in a dry, low-dust environment. An ag-
gressive atmosphere must also be avoided.
3. The user must be made aware of repeat testing using the test button T.
4. Using surge current strength residual current circuit-breakers cannot abso-
lutely guarantee to rule out trips due to leakage currents caused by surge
voltage. In cases where an interruption of the power supply may lead to
potential dangers for humans and animals or serious damage to property,
residual current protection should be implemented by means of increased
surge current strength, selective residual current circuit-breakers and up-
stream surge arresters. In specific cases, the switching status should be
monitored by means of an auxiliary contactor at the residual current circuit-
breaker and an appropriate signalling device.
5. The guarantee will be rendered null and void if the device is opened.
Wiring diagrams
1 3
2 4
V two-pole
(N)
1 3 5
7
(N)
(N) 2 4 6
8
(N)
V four-pole, neutral on left or right, depending on device version
Technical Data
DFS 4 B SK / F60 / V500 / V500 F60 / S / S V500
Rated current
Rated residual current I ∆N
Detection range of residual
current
Rated
voltage
U n
DFS 4 B
Rated
frequency
DFS 4 B
residual currents
min.
operating
voltage
residual currents
Internal consumption
SK, SK F60, SK S
Working
range of
test circuit
DFS 4 B
number of poles
Dissipation power P v (typ.)
Thermal back-up fuse
OCPD,
utilization category gG
Short-circuit back-up fuse
SCPD,
utilization category gG
Tripping times
Tripping times selective
Rated switching capacity I m
Rated short-circuit switch-
ing capacity I ∆m
Rated short-circuit current
I nc
Rated residual short-circuit
current I ∆c
Surge current strength
Shock resistance
Type of protection
Installation position
Supply side
Ambient temperature
Resistance to climatic
changes
round-wire, solid
Terminals
~
min. cross section
Tightening torque of
terminals
Endurance
Design requirements
Electromagnetic compat-
ibility
Weight
Dimensions
DIN VDE 0636, IEC 60269
1)
16 A
25 A
40 A
63 A
80 A 100 A 125 A
0.03 A; 0.1 A; 0.3 A; 0.5 A
0 – 100 kHz
SK F60
230/400 V AC
SK V500 F60
290/500 V AC
SK
50 Hz
SK F60
60 Hz
SK V500
50 Hz
SK V500 F60
60 Hz
for detection of
0 V (mains independent)
Type A/AC
for detection of
50 V AC
Type B
max. 3.5 W
185 V AC – 440 V AC
SK V500,
SK V500 F60,
185 V AC – 500 V AC
SK S V500
two-pole, four-pole
0.5 W 1.2 W 2.9 W 7.2 W 12 W 18 W 28 W
16 A
25 A
40 A
63 A
1)
100 A
1)
1 x I ∆n ≤ 300 ms; 5 x I ∆n ≤ 40 ms
1 x I�n > 130 ms ≤ 500 ms;
5 x I�n > 50 ms ≤ 150 ms
500 A
630 A 800 A 1000 A 1250 A
500 A
630 A 800 A 1000 A 1250 A
10 kA
10 kA
Ring-wave 0.5 ms / 100 kHz:
200 A, impulse 8/20 µs: 3 kA
20 g / 20 ms duration
IP 40 (after installation in distribution board)
optional
terminals 1, 3, 5, 7
-25 °C to +40 °C
conforming to IEC 68-2-30: damp/heat, cyclic
(25 °C / 55 °C; 93 % / 97 % rel. hum., 28 cycles)
1 x 1.5 – 50 mm²
2 x 1.5 – 16 mm²
1 x 1.5 – 50 mm²
stranded
2 x 1.5 – 16 mm²
1 x 1.5 – 35 mm²
flexible
2 x 1.5 – 16 mm²
50 mm²
3 Nm
mechanical
> 5,000 cycles
electrical
> 2,000 cycles
DIN EN 61008-1, DIN EN 62423
IEC 61 453 (interference resistance
– industrial environment)
approx. 500 g
W 72 mm (4 module width) × H 85 mm × D 75 mm
80 A
125 A