BENDIX BA-921 COMPRESSOR-STD-CLOSED ROOM Service Data - Page 4
Parcourez en ligne ou téléchargez le pdf Service Data pour {nom_de_la_catégorie} BENDIX BA-921 COMPRESSOR-STD-CLOSED ROOM. BENDIX BA-921 COMPRESSOR-STD-CLOSED ROOM 17 pages. Air power compressor
Également pour BENDIX BA-921 COMPRESSOR-STD-CLOSED ROOM : Instructions d'installation (4 pages)
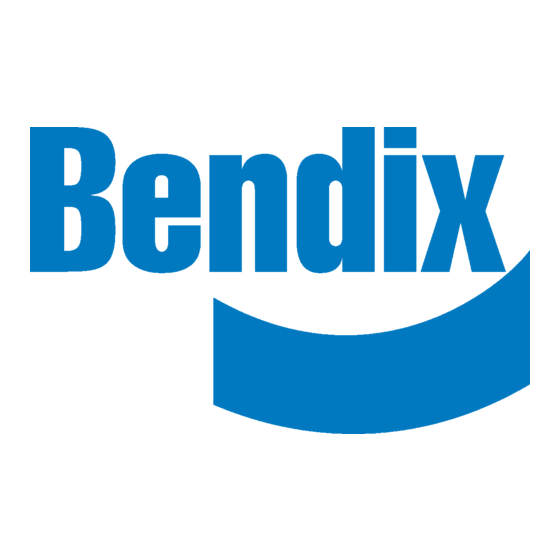
BACK / RETOUR
UNLOADER
COVER
HEAD
BOLT (4)
INLET
PORT
COOLANT IN OR OUT
(ONE OR OTHER NOT USED)
CYLINDER HEAD PORT IDENTIFICATION
The cylinder head connection ports are identified with cast
in numerals as follows:
Atmospheric AIR IN
Compressed AIR OUT
Coolant IN or OUT
Governor Control
FIGURE 8- TYPICAL BA-921 CYLINDER HEAD
AIR INDUCTION
The BA-921 compressor is designed for either natural aspi-
ration (connection to the vacuum side of the engine's air
induction system) or turbocharging. When attached to the
pressure side of the turbocharger, pressure at the BA-921
inlet port must not exceed 45 psig. See the tabulated tech-
nical data in the back of this manual.
One of the single most important aspects of compressor
preventive maintenance is the induction of clean air. Since
the BA-921 is connected to the engine air cleaner, proper
periodic maintenance of the engine air filter eliminates the
need for separate filter maintenance.
Inspect the compressor intake fittings, and the connecting
hoses each time engine air cleaner maintenance is per-
formed.
1. Inspect the intake hose adapters for physical damage.
Make certain to check the adapters at both ends of the
intake hose or tubing.
2. The intake hose clamps and tighten them if needed.
3. Inspect the intake hose or line for signs of drying, crack-
ing, chafing and ruptures and replace it if necessary.
COMPRESSOR COOLING
Inspect the compressor discharge port, inlet cavity and dis-
charge line for evidence of restrictions and carboning. If
excessive buildup is noted, thoroughly clean or replace the
affected parts. Since carbon buildup generally indicates in-
adequate cooling, closely inspect the compressor cooling
system. Check all compressor coolant lines for kinks and
4
COOLANT IN OR OUT
(ONE OR OTHER NOT USED)
GOVERNOR
CONNECTION
DISCHARGE
PORT
DISCHARGE
SAFETY VALVE
0
2
9
4
restrictions to flow. Minimum coolant line size is 3/8" I.D.
Check coolant lines for internal clogging from rust scale. If
coolant lines appear suspicious, check the coolant flow and
compare to the tabulated technical data present in the back
of this manual. Carefully inspect the air induction system
for restrictions.
LUBRICATION
Check the external oil supply line for kinks, bends, or re-
strictions to flow. Supply lines must be a minimum of 3/16"
I.D. Refer to the tabulated technical data in the back of this
manual for oil pressure minimum values.
COMPRESSOR DRIVE
Check for noisy compressor operation, which could indi-
cate excessive drive component wear. Adjust and/or replace
as necessary. Check all compressor mounting bolts and
retighten evenly if necessary. Check for leakage and proper
unloader mechanism operation. Repair or replace parts as
necessary.
COMPRESSOR UNLOADER & GOVERNOR
Test and inspect the compressor and governor unloader
system for proper operation and pressure setting.
1. Make certain the unloader system lines are connected
as illustrated in figure 3.
2. Cycle the compressor through the loaded and unloaded
cycle several times. Make certain that the governor cuts
out at its specified pressure (cut in should be approxi-
mately 15-20 psi less than cutout pressure). Adjust or
replace the governor as required.
3. Note that the compressor cycles to the loaded and un-
loaded conditions promptly. If prompt action is not noted,
repair or replace the governor and/or repair the com-
pressor unloader.
SERVICE TESTS
GENERAL
The following compressor operating and leakage tests need
not be performed on a regular basis. These tests should
be performed when; it is suspected that leakage is sub-
stantially affecting compressor buildup performance, or when
it is suspected that the compressor is "cycling" between
the load and unloaded modes due to unloader plunger leak-
age.
OPERATING TESTS
Compressor Performance
Vehicles manufactured after the effective date of FMVSS
121 must have a compressor capable of raising air system
pressure from 85-100 psi in 25 seconds or less, with the