KitchenAid KDTE104ESS3 Fiche technique - Page 11
Parcourez en ligne ou téléchargez le pdf Fiche technique pour {nom_de_la_catégorie} KitchenAid KDTE104ESS3. KitchenAid KDTE104ESS3 12 pages.
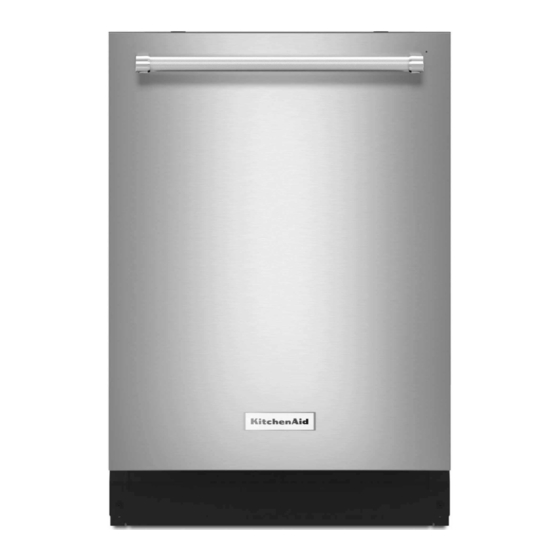
FOR SERVICE TECHNICIAN'S USE ONLY
Customer
Potential Causes
Description
Detergent Not
1. Item in lower rack
Dispensing or
blocked lid or blocked
Detergent Left
spray of water to
in Dispenser
dispenser.
NOTE:
2. Mechanical binding
Check error
of dispenser lid.
history. If no
error codes for
electrical
problems, problem
3. Lid latch binding
is mechanical. Do
due to excess
not replace
detergent in
control.
mechanism.
4. Dispenser electrical
problem.
5. Control canceled
cycle before
dispensing due to
error detected with
wash motor.
Poor Wash
1. Cycle selection of
customer not
appropriate for dish
load.
2. Plugged or
damaged screens.
3. Spray arms not
rotating or plugged.
4. Poor wash due to
draining, dispensing,
and/or temperature
problem.
5. Control canceled
cycle due to error
detected with wash
motor.
6. Soil sensor
problem.
7. Diverter problem.
8. Diverter disk
missing.
9. Heating problem.
10. Softener problem
(on some models).
Check
Related
Error
Code
Instruct customer on
proper dish loading.
1. Unplug dishwasher
or disconnect power.
2. Check/replace
dispenser.
Instruct customer on
proper dispenser filling.
10-1
Refer to "Service Error
Codes" table.
Refer to "Service Error
4-3
Codes" table.
Instruct customer on cycle
selection. Recommend
"High Temp" option for
wash performance boost.
Inspect following
3 screens:
- Filter cup coarse screen
- Filter cup fine screen
- Sump fine screen
1. Check arm rotation. If
arms are blocked by dish
item, instruct customer.
Also check for correct
upper spray arm alignment
with docking station
located on feed tube back
wall.
2. Check nozzles. If they
are plugged, clean nozzles
and confirm filters installed
properly.
See "Will Not Drain or
Excess Water Left in Unit,"
or "Detergent Not
Dispensing or Detergent
Left in Dispenser," or
details on temperature
sensing in "Long Cycles
and/or Stuck in Certain
Part Of Cycle."
Refer to "Service Error
4-3
Codes" table.
Refer to "Service Error
3-2
Codes" table.
3-3
NOTE: Even if no error
code recorded, confirm
OWI passes all OWI checks
in Service Diagnostics
cycle and see checks for
Error 3-3.
Refer to "Service Error
9-1
Codes" table.
9-2
Remove outlet cover and
inspect for red plastic disk
through holes in outlet.
Install new disk if missing.
Refer to "Service Error
7-1
Codes" table.
Refer to "Service Error
6-8
Codes" table.
Customer
Potential Causes
Description
Film or Spots
1. Customer not using
on Glasses
rinse aid and/or
and/or Dishes
heated dry.
2. RInse aid dispenser
problem.
3. Hard water leaving
film on dishes.
4. Detergent carryover
or over-sudsing.
5. Etching of glass
from too much
detergent at too high
of temperature.
6. Diverter problems. Refer to "Service Error
7. Drain loop check
valve not sealing.
Poor Dry
1. Customer not using
rinse aid and/or
dispenser empty.
2. Customer not using
Heated Dry option.
3. Rinse aid dispenser
problem.
4. Vent stuck closed
due to pilot relay
stuck on.
5. Diverter problem
kept water from
heating in final rinse
(plastic tub models
only).
6. Fan problem (on
models with fan).
7. Control canceled
cycle due to error
detected with wash
motor.
8. Heating problem.
11
Check
Related
Error
Code
Check rinse aid gauge level
on dispenser. Instruct
customer how to fill and
monitor, add, or use
rinse aid.
Refer to "Service Error
10-1
Codes" table.
Check water hardness. If
hard, instruct customer to
use premeasured
detergent tablets or packs
and rinse aid daily. Also
recommend 1 HR Wash
cycle. To clean the
dishwasher, recommend
running with 1 cup (250
mL) of white vinegar
sitting upright in upper
rack.
For models with water
softener, check for "Add
Salt" LED at the end of
cycle. If On, add salt and
instruct customer.
For models with water
6-8
softener, Regen valve
electrical problem. Refer to
"Service Error Codes"
table.
6-3
Check water hardness. If
below 10 grains, instruct
customer to use less
detergent and recommend
the 1 HR Wash cycle.
Check water hardness. If
below 10 grains, instruct
customer to use less
detergent and recommend
the 1 HR Wash cycle.
9-1
Codes" table.
9-2
1. Disconnect drain hose at
plumbing connection.
2. Elevate hose above
dishwasher and fill with
water. If water flows into
dishwasher, replace entire
drain loop. Install as high
as possible and attach to
underside of counter top if
possible.
Check rinse aid gauge
level on dispenser. Instruct
customer how to fill and
monitor, add, or use
rinse aid.
Recommend use of Heated
Dry or Smart Dry to
customer.
10-1
Refer to "Service Error
Codes" table.
Refer to "Service Error
1-1
Codes" table.
Refer to "Service Error
9-1
Codes" table.
9-2
Refer to "Service Error
10-3
Codes" table.
4-3
Refer to "Service Error
Codes" table.
Refer to "Service Error
7-1
Codes" table.