Miller A-500 Manuel du propriétaire - Page 12
Parcourez en ligne ou téléchargez le pdf Manuel du propriétaire pour {nom_de_la_catégorie} Miller A-500. Miller A-500 24 pages.
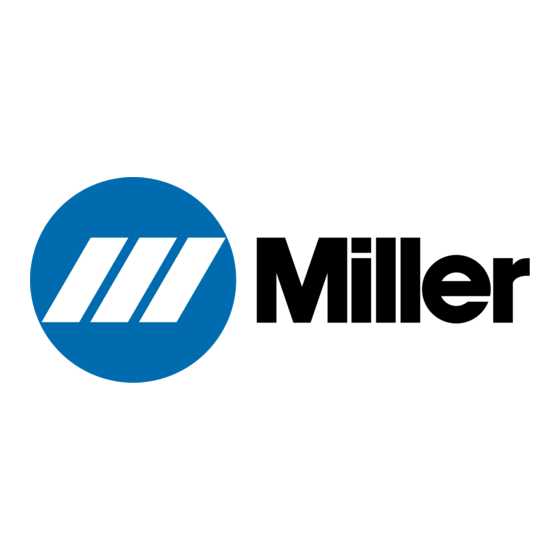
3-2.
ELECTRICAL INPUT CONNECTIONS
A.
Electrical
Input Requirements
This
welding
power
source
is
designed
to
be
operated
from
a
three-phase,
60
Hertz,
ac
power
supply
which
has
a
line
voltage
rating
that
corresponds
with
the
electrical
input
voltage
shown
on
the
nameplate.
Consult the local electric
utility
if there is any
question
about the type of electrical
system
available
at
the
installation
site
or
how
proper
connections
to
the
welding
power
source
are
to
be made.
B.
Input
Conductor Connections
rri
It
is
recommended
that
a
line disconnect switch be
installed
in
the
input
circuit
to
the
welding
power
source.
This
would
provide
a
safe
and convenient
means
to
completely
remove
all electrical power
from
the
welding
power
source
whenever
it is necessary
to
perform
any internal
function
on
the unit.
I
I~_
r
Before
making
electrical
input
connections
to
the
welding
power
source,
machinery
lockout
procedures
should be
employed.
If the connection is
to
be made from
a
line disconnect
switch,
the switch
should
be
padlocked
in
the
open
position.
If the
connection is made from
a
fuse
box,
remove
the fuses
from
the box
and
padlock
the
cover
in
the
position.
If the unit is connected
to
a
circuit
breaker,
or
other
disconnecting
device
without
locking
facilities,
attach
a
red
tag
to
the device
to
warn
others
that the circuit is
being
worked
on.
CAUTION
Connect the
inpu:
conductors
to
th~ing
power
source
before
making
connections
to
the
three-phase
power
supply.
The
input
conductors should be covered with
an
insulating
material which conforms
to
local electrical standards. Table
3-1
is
provided only
as a
guide
for
selecting
the proper size
input
conductors and fuses.
Table 3-1.
Input
Conductor And Fuse Size
Input
Conductor Size
-
AWG
Fuse Size
In
Amperes
230V
460V
480V
230V
460V
480V
6(81
10(10)
10110)
90
45
45
Input
conductor sizes
are
based
on
allowable
ampacities
of
insulated
copper
conductors,
having
a
temperature
rating
of
75C,
with
not
more
than three conductors
in
a
raceway
or
cable.
Numbers in I
I
are
equipment ground
conductor sizes.
Insert the three
input
conductors
plus
one
ground
conductor
through
the
access
hole
on
the
rear
panel.
This hole will
accept
standard conduit
fittings.
See
Figure
3-2 for hole loca
tion and size.
reco
mme
nded
th
at
a
ter
ml
na
I
lug
S
adeq
ua
te
amperage
capacity
be attached
to
the ends of the
in
put and
ground
conductors. The hole diameter
in the
terminal
lug
must
be of proper size
to
accommodate
the line and
ground
terminal studs.
Connect
the three
input
conductors
to
the line terminals
on
the
primary
terminal board and
connect
the
ground
conduc
tor
to
the
ground
terminal
(see Figure
3-2 for location of
terminals).
The
remaining
end
of
the
ground
conductor
should be connected
to
a
proper
ground,
Use
a
grounding
method that is
acceptable
to
the local electrical
inspection
authority.
I
The
ground
terminal
is
connected
to
the
welding
power
source
chassis
and
is
for
grounding
purposes
only.
Do
not connect
a
conductor from the
ground
terminal
to
any
one
of the line terminals
as
this will
result
in
an
electrically
energized
welding
power
source
chassis.
Figure
3-2.
Input
Conductor Connections
3.3. WE1..D OUTPUT CONNECTiONS
To
obtain the full rated output from this
unit,
it is necessary
to
select, install,
and maintain
proper
welding
cables. Failure
to
comply
in
any
of
these
areas
may
result
in
less than
satisfactory
welding performance.
L,
Ensure that the
unit is
completely
shut down before
making
any
weld output connections.
A.
Location
The
POSITIVE
and
NEGATIVE weld output
terminals
are
located
on
the upper
portion
of
the
front
panel,
B.
Welding
Cables
If
welding
cables
were
not
ordered with this
unit,
the steps
listed
should
be
followed
to
ensure
the
best
welding
performance:
1.
It
is
recommended
that the
welding
cables be
kept
as
short
as
possible,
be
placed
close
together,
and
be of
adequate
current
carrying capacity.
The resistance of the
welding
cables
and
connections
causes
a
voltage
drop
which
is added
to
the
voltage
of the
arc.
Excessive
cable
resistance
may
result in
overloading
as
well
as
reducing
the
maximum
current
output
capability
of
this
unit.
Prdper operation
is
to
a
great
extent
dependent
on
the
use
of
welding
cables
and
connections
that
are
in
good
condition
and
of
adequate
size.
2.
Use Table 3-2
as a
guide
for
selecting
correct
cable size for
the
anticipated
maximum
weld
current
which
will
be
~,,
Table 3-2 shows total cable
length,
which includes
the electr.4e and work cable.
Example:
If the electrode
holder cable
is 75 feet
long
and the work cabte
25 feet
long,
select the size cable that
is
recommended for 100
feet
at
the maximum weld
current
that is
to
be used.
3.
Do
not
use
damaged
or
frayed
cables.
4.
Use
correct
lugs
on
the weld cables
to
connect
the work
clamp
and
to
connect
the cables
to
the weld
output
terminals.
5,
Ensure that all connections
are
clean and
tight.
CAUTION
I
Ground Terminal
TA-049 297
I
I
Page
6