Baumer GNAMG Series Manual - Halaman 5
Jelajahi secara online atau unduh pdf Manual untuk Aksesori Baumer GNAMG Series. Baumer GNAMG Series 41 halaman. Inclination sensor with canopen interface
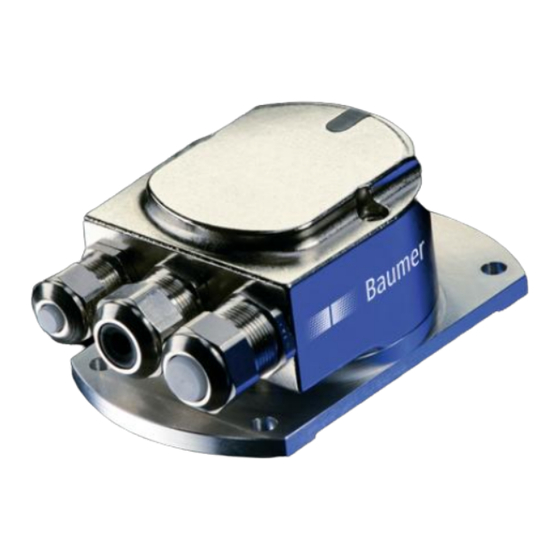
3. CAN-bus and CANopen communication
CAN bus (CAN: Controller Area Network) was developed by Bosch and Intel for high-speed, economic data
transmission in automotive applications. Today CAN bus has been commercialised for use in industrial
automation.
CAN bus is a fieldbus system (standards administered by CAN in Automation, CiA) for communication
between appliances, actors and sensors of different brands.
3.1.1. CAN-bus properties
• Data rate of 1 Mbaud with network length capabilities of max. 40m
• Bilateral terminated network
• Bus medium: twisted pair wire
• Realtime capability: Max. defined waiting time for high priority messages.
• In theory up to 127 users in one bus line, physically however only 32 (due to driver).
• Seized netwide data consistency. Faulty messages are made known as faulty to all nodes in the network.
• Message-oriented communication
The message comes with an identifier. All nodes in the network check by the identifier whether the message
is relevant for them or not.
• Broadcasting, Multicasting
All nodes get every message at the same time, thus enabling synchronisation.
• Multi-Master capability
Every fieldbus user is able to transmit or recieve data independently, irrespectible of a priority by master.
Every user can start his message if the bus is not busy. If several messages are transmitted at the same
time, the user with the highest priority will succeed.
• Message priorities
Message priority is determined by the identifier. Thus, the bus is quickly transmitting important messages.
• Risk of remaining errors
Reliability precautions in the network reduce the risk of faulty, inevident data transmissions to less than 10
11
. A 100% reliability in transmission can be taken for granted.
• Function guarding
Stations with malfunction or breakdown are located. The CAN protocol provides function guarding of the
nodes in the network. Defective nodes are restricted in their function or even logged off from the network.
• Data transmission with minimized error recovery time
Thanks to several error diagnostics faulty messages will be recognized with maximum reliability. Upon
recognizing an error the message will be automatically repeated.
CAN bus is networking several bus users by bus cable. Every network user is in a position to transmit and
receive messages. There is a serial data transmission between the individual network users.
Network users for CAN bus euipment might be:
• automation equipment, for example PLCs
• PCs
• input/output modules
• drive controls
• analysing equipment, for example CAN monitor
• operating and input equipment as HMI (human machine interface)
• sensors and actuators
Manual_GNAMG_CANopen_EN.doc
21.11.12
5/41
Baumer IVO GmbH & Co. KG
Villingen-Schwenningen, Germany
-