Dover BLACKMER CRL1.25 Petunjuk Pemasangan, Pengoperasian, dan Pemeliharaan - Halaman 3
Jelajahi secara online atau unduh pdf Petunjuk Pemasangan, Pengoperasian, dan Pemeliharaan untuk Pompa Air Dover BLACKMER CRL1.25. Dover BLACKMER CRL1.25 12 halaman. Blackmer liquefied gas pumps
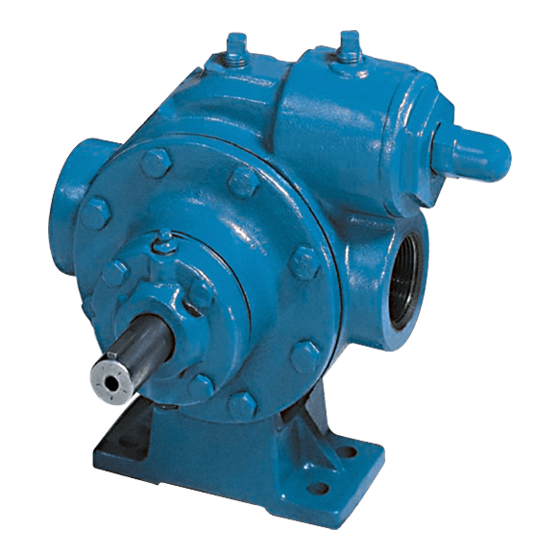
NOTICE:
Blackmer pumps must only be installed in systems
designed by qualified engineering personnel.
design must conform with all applicable regulations and
codes and provide warning of all system hazards.
Install, ground and wire to local and
National Electrical Code requirements.
Install an all-leg disconnect switch near
the unit motor.
Disconnect and lockout electrical power
before installation or service
Hazardous voltage.
Electrical supply MUST match motor
Can shock, burn or
nameplate specifications.
cause death.
Motors equipped with thermal protection automatically
disconnect motor electrical circuit when overload exists.
Motor can start unexpectedly and without warning.
PRE-INSTALLATION CLEANING
NOTICE:
New pumps contain residual test fluid and rust inhibitor.
If necessary, flush pump prior to use.
Foreign matter entering the pump WILL cause extensive
damage. The supply tank and intake piping MUST be
cleaned and flushed prior to pump installation and operation.
LOCATION AND PIPING
Pump life and performance will be significantly reduced when
installed in an improperly designed system. Before starting
the layout and installation of the piping system, review the
following suggestions:
1.
Locate the pump as near as possible to the source of
supply to avoid excessive inlet pipe friction.
2.
The inlet line should be at least as large as the intake
port on the pump. It should be insulated, slope downward
to the pump, and should not contain any upward loops.
Eliminate restrictions such as sharp bends; globe valves,
unnecessary elbows, and undersized strainers.
3.
A strainer must be installed in the inlet line to protect the
pump from foreign matter. The strainer should be located
at least 24" (0.6m) from the pump, and have a net open
area of at least four times the area of the intake piping.
The strainer housing must be rated to 600 WOG.
Strainers must be cleaned regularly to avoid pump
starvation.
4.
The intake and discharge piping system must be free of
all leaks.
5.
Expansion joints, placed at least 36" (0.9m) from the
pump, will compensate for expansion and contraction of
the pipes. Contact the flexible connector/hose
manufacturer for required maintenance/care and design
assistance in their use.
6.
Install pressure gauges in the NPT ports provided in the
pump casing to check pump performance at start up.
7.
ALL piping and fittings MUST be properly supported to
prevent any piping loads from being placed on the pump.
INSTALLATION
8.
Check alignment of pipes to pump to avoid strains which
might later cause misalignment. See Figure 2. Unbolt
System
flanges or break union joints. Pipes should not spring
away or drop down. After pump has been in operation
for a week or two, completely recheck alignment.
9.
The use of a vapor return line will speed up delivery by
preventing pressure build up at the receiving tank and
reducing pressure in the supply tank.
10. Keeping the liquefied gas systems full of liquid, even
when idle, will keep the O-rings from changing shape,
shrinking or super cooling. Evaporation of liquefied gas
leaves an abrasive powder on the surface which can
cause wear to the pump, meter, and seals.
INTERNAL PUMP RELIEF VALVE AND EXTERNAL
BYPASS VALVE
The pump internal relief valve is designed to protect the
pump from excessive pressure and must not be used as
a system pressure control valve.
For ALL liquefied gas applications, install an external bypass
valve, and any necessary piping, back to the tank. DO NOT
pipe the bypass valve back to the intake line.
Refer to "Relief Valve Setting & Adjustment" section. The
setting on the external bypass valve must be at least 25 psi
(1.7 bar) lower than the pump internal relief valve setting. The
valve and piping must be of adequate size to accommodate
the full flow from the pump when the discharge line is closed.
Refer to Blackmer Bypass Valve Installation and Maintenance
Instructions for bypass valve settings and adjustments.
701-A00
page 3/12
Figure 2
NOTICE:
Figure 3 – Bypass Valve Mounting