Axminster CrushGrind Shaft 195mm Petunjuk - Halaman 2
Jelajahi secara online atau unduh pdf Petunjuk untuk Peralatan Axminster CrushGrind Shaft 195mm. Axminster CrushGrind Shaft 195mm 4 halaman. 195mm
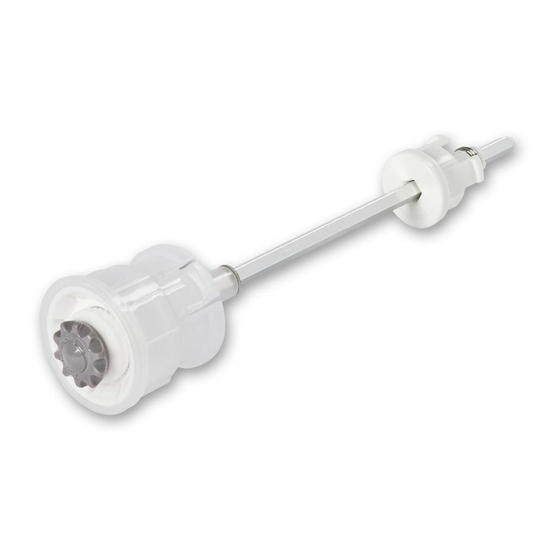
CrushGrind Shaft Instructions
Congratulations on your choice of this high quality
ceramic peppermill mechanism which should give you
many years of useful service. The following tips and
guidance should assist in the process of making a mill
to be proud of.
Preparing your blank
Select a suitable section of timber approximately
65mm square and long enough to accommodate your
mechanism plus some storage space for peppercorns,
salt, etc. The shaft could be reduced in length to make a
shorter mill if required.
Turn down to a cylinder between centres slightly
undercutting the ends and part off a section about 85mm
long that will be used for the top.
Boring the mill blanks
Remount the body section of the mill holding the end
that was adjacent to the top in the jaws of a woodturning
chuck.
Using a tailstock chuck and saw tooth Forstner bit drill
a 45mm diameter hole in the bottom of the mill body
19mm deep.
Change the size of bit to 38mm diameter and drill to
a depth of 53mm overall. A simple way of achieving
the correct depth is by wrapping some insulating tape
around the shank of your drill bits and using this as a
depth guide.
Using a special recess tool, the groove for the catchers on
the mill mechanism can now be cut at the bottom of this
hole to about 5mm deep x 5mm wide.
Now place a 25 or 26mm diameter bit in your tailstock
chuck and drill to a depth of approximately three quarters
of the length of the mill body.
Remove the mill body from the lathe and turn end for
end gripping the drilled bottom end in your woodturning
chuck.
Change the bit size to 38mm and bore a hole 15mm deep
and then change to a 25 or 26mm bit and bore to meet
the hole you bored from the other end of the mill. The
boring on this section is now complete.
Now mount the top section into the woodturning chuck
and gripping it by the uppermost part drill a 22mm hole
to a depth of 40mm using a saw tooth Forstner bit.
Turn a tenon on the top section approximately 10mm
long by 38mm diameter to fit into the hole bored into
the top end of the mill body. Use the body of the mill as a
sizing guide for this tenon.
Using a recess tool, make a 5mm location groove for the
catchers on the top section of the mechanism. This should
be 14.8mm in from the edge of the hole.
This concludes the boring of the top section of the mill.
Finishing your mill
Make up some stepped hardwood insert blocks to fit the
holes at either end of the mill body and remount between
centres. Make sure you get a snug fit between the body of
the mill and the blocks. Turn the mill body to your chosen
design and sand and finish.
Turn a stepped insert block mounted on your screw chuck
to fit into the 22mm hole in the top section of the mill.
When a good friction fit is achieved, mount and turn the
top section of your mill to your chosen design, sand and
finish. As an alternative you could hold the top section by
holding the tenon in your woodturning chuck for shaping
and finishing.
The following saw tool Forstner bits are available for
drilling the required holes
502051 Fisch Saw Toothed Forstner Bit 22mm
502052 Fisch Saw Toothed Forstner Bit 25mm
502056 Fisch Saw Toothed Forstner Bit 38mm
502057 Fisch Saw Toothed Forstner Bit 45mm
Final Assembly
When you are satisfied with the design and finish of your
mill, you will need to assemble the components. A careful
check of dimensions should be made before assembly of
the mill takes place N.B When producing a CrushGrind
mill, the utmost care and attention should be paid to
the dimensions given as this will ensure the assembly
goes smoothly and you will have a mill that will last
for many years.
Make up a cylindrical block of wood 44mm diameter
by 25mm long and produce a recess in one end big
enough to accommodate the knob at the bottom of the
mechanism. This is used to press the mechanism up into
the lower section of the mill.
A suitable block will be needed for the top end but
2