DOLD MINISTART BL 9228 Terjemahan Petunjuk Asli - Halaman 2
Jelajahi secara online atau unduh pdf Terjemahan Petunjuk Asli untuk Pengontrol DOLD MINISTART BL 9228. DOLD MINISTART BL 9228 6 halaman. Softstarter with dc-brake
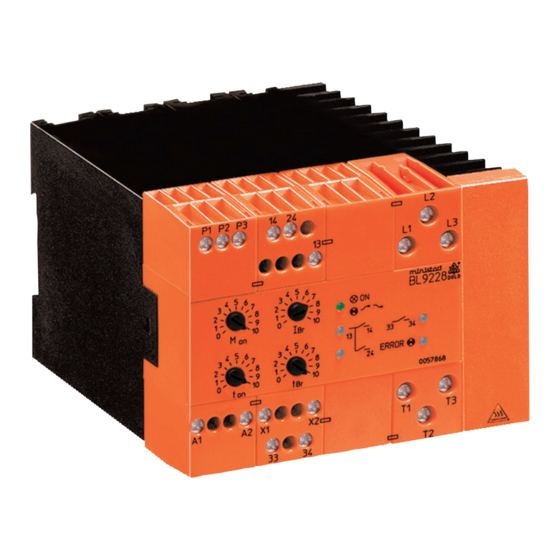
Function Diagram
A1/A2
X1
L1/L2/L3
13-24
43-44
33-34
T1
T2/T3
M Mot
n
t 0
t 1
t 2
t 0
: start
t 4
: stillstand detection
t 0 -t 1 : test
t 1 -t 2 : ramp up time
t 3 -t 4 : braking time
Function
Monitoring relay 4 (contact 43-44)
This relay is energized when motor standstill is detected. It will be reset by
pushing the on-button. The contact can be used for example to lock a safety
gate. The monitoring relay 4 is de-energized if an error occurs.
Input P
/ P
/ P
to monitor the motor temperature
1
2
3
To monitor overtemperature onnb the motor a bimetallic contact can
be connected to P
/ P
. When overtemperature is detected the power
2
3
semiconductors switch off and all relays de-energise.
On P
/ P
up to 6 PTC sensors can be connected. On detection of
1
2
overtemperature, short circuit or broken wire (in sensor circuit) the power
semiconductors switch off and all relays de-energise.
The fault is reset by disconnecting the power supply temporarily after the
temperature on the motor is down again.
Indication
Green LED: Continous light: - When auxiliary supply connected
Flashing light:
Monitoring relay 1
Yellow LED: Continous light: - When contact 13-14 switched on
Monitoring relay 2
Yellow LED: Continous light: - When contact 13-24 switched on
Monitoring relay 3
Yellow LED: Continous light: - When contact 33-34 switched on
t 3
t 4
t 0
- While starting and breaking
Indication
Monitoring relay 4 optional
Yellow LED: Continous light: - When contact 43-44 switched on
Red LED:
Flashing light :
1*
:
)
2*
:
)
3*
:
)
4*
:
)
5*
:
)
6*
:
)
7*
:
)
8*
:
)
9*
:
)
10*
:
)
11*
:
)
12*
:
)
13*
:
)
14*
)
:
15*
)
:
16*
)
:
17*
)
:
1-17*
)
= Number of flashing pulses in short sequence
Monitoring Features
- If the motor does not stand still within 10 sec during brake function
the monitoring relay 1 will indicate this. The brake function is stopped
latest after 15 sec if there is no standstill detection, and the motor
is separated from the mains.
A restart resets the monitoring relay 1. If this error occurs for the third
time the device changes into the error mode. The red LED will flash
code 9.
t
t 1
- The brake current switches off after 0.5 sec standstill detection.
- On power up the mains frequency, phase sequence and presence
of all 3 phases is checked.
M5663
- Internal temperature monitoring protects the thyristors. With the
function "motor overtemperature" a bimetall switch or PTCs are
monitored. By switching on or off of the power supply this fault can
be reset after the temperature has dropped.
- Monitoring of phases and phase shift protects the motor or the
system. After removing the fault this error can be reset by switching
the power supply on and off.
- After connecting the power supply or after braking until restart a
check will be done if L1, L2 or L3 of the device are separated
from the mains (to ensure that contactor K1 or relay 3 are not welded).
It is detected if 2 or 3 phases are connected in a wrong way.
- Monitored current to protect the power part and the relays at heavy duti
start or blocked motor.
Notes
Variation of speed is not possible with this device. Without load a softstart
cannot be achieved. It is recommended that the softstart is protected by
superfast semiconductor fuses rated as per the current rating of the softstart
or motor. However, standard line and motor protection is acceptable, but
for high starting frequencies motor winding temperature monitoring is
recommended. The softstarter must not be operated with capacitive load
e.g. power factor compensation on the output.
In respect to safety of persons and plant only qualified staff is allowed to
work on this device.
2
- Error
- Overtemperature on thyristor (internal)
- Overtemperature on motor or broken
wire in sensor circuit P
/P
1
2
- Short circuit on sensor circuit P
- Phase failure
- Incorrect phase sequence, exchange
connections on L1 and L2
- Incorrect frequency
- Incorrect brake circuit
- Incorrect safety monitoring
- Braking time 3 x higher than 10 s
- Incorrect RAM
- Incorrect RUN-input (start switch
welded)
- Device not separated from mains (2 or
3 phases occur before start)
- Overcurrent in semiconductors
- Brake current to high
- Overcurrent at end of ramp up
- Communication error
- Overcurrent on bridging relay
11.01.21 en / 335A
/P
1
2