Dover Wilden Hornet HU38 Ingegneria, funzionamento e manutenzione - Pagina 4
Sfoglia online o scarica il pdf Ingegneria, funzionamento e manutenzione per Pompa dell'acqua Dover Wilden Hornet HU38. Dover Wilden Hornet HU38 4.
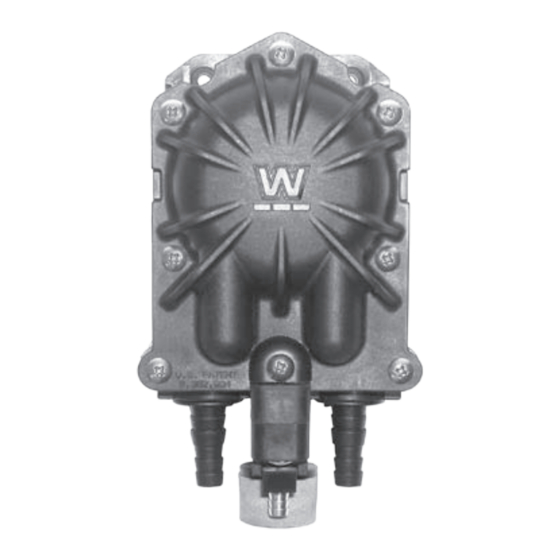
T R O U B L E S H O O T I N G
Pump will not run or runs slowly.
1.
Ensure air pressure is at least 0.3 bar (5 psig) above start
up pressure and differential pressure (the difference
between air inlet and liquid discharge pressures) is not
less than 0.7 bar (10 psig).
2.
Check air inlet filter for debris. A 5μ (micron) air filter
must be installed at the air inlet of the pump to prevent
air compressor particulate from entering and damaging
the air distribution system.
3.
Check for air leakage (blow by) at the exhaust of the
pump. This could indicate worn seals/bore in the air
valve.
4.
Disassemble pump and check for obstructions in the
air passage-ways or objects which would obstruct the
movement of internal parts.
5.
Check for sticking check valves.
pumped is not compatible with pump elastomers,
swelling may occur. Also, as the check valves wear,
they become smaller and can become stuck in the
seats.
6.
Diaphragms may have a pinhole allowing air to escape
to the liquid side of the pump reducing performance.
Pump runs but little or no product flows.
1.
Check for pump cavitation; slow pump speed down to
allow thick material to flow into liquid chambers.
2.
Verify that vacuum required to lift liquid is not greater
than the vapor pressure of the material being pumped
(cavitation).
w a R R a N T y
Each and every product manufactured by Wilden Pump & Engineering, LLC is built to meet the highest standards of quality.
Every pump is functionally tested to insure integrity of operation. Wilden Pump & Engineering, LLC warrants that pumps,
accessories and parts manufactured or supplied by it to be free from defects in material and workmanship for a period
of five (5) years from date of installation or six (6) years from date of manufacture, whichever comes first. Failure due to
normal wear, misapplication, or abuse is, of course, excluded from this warranty. Since the use of Wilden pumps and parts is
beyond our control, we cannot guarantee the suitability of any pump or part for a particular application and Wilden Pump &
Engineering, LLC shall not be liable for any consequential damage or expense arising from the use or misuse of its products
on any application. Responsibility is limited solely to replacement or repair of defective Wilden Pump & Engineering, LLC. All
decisions as to the cause of failure are the sole determination of Wilden Pump & Engineering, LLC. Prior approval must be
obtained from Wilden for return of any items for warranty consideration and must be accompanied by the appropriate MSDS
for the product(s) involved. A Return Goods Tag, obtained from an authorized Wilden distributor, must be included with the
items which must be shipped freight prepaid. The foregoing warranty is exclusive and in lieu of all other warranties expressed
or implied (whether written or oral) including all implied warranties of merchantability and fitness for any particular purpose.
No distributor or other person is authorized to assume any liability or obligation for Wilden Pump & Engineering, LLC other
than expressly provided herein.
3.
Check for sticking check valves.
pumped is not compatible with pump elastomers,
swelling may occur. Also, as the check valve wear, they
become smaller and can become stuck in the seats.
4.
Pump may be operating (cycling) too fast.
situation, to prime the pump you must lower the air
inlet pressure to achieve maximum suction lift. Once
pump is primed the inlet air pressure can be raised to
meet system requirements.
Pump air valve freezes.
1.
Check for excessive moisture in compressed air
line. Either install a dryer or hot air generator at the
compressor. A coalescing filter may also be used to
remove the water from the compressed air line some
applications.
If material being
Air bubbles in pump discharge.
1.
Check for ruptured diaphragm.
2.
Check tightness of fasteners and integrity of o-ring
and seals.
3.
Ensure hosing connections are airtight.
Product comes out air exhaust.
1.
Check for diaphragm rupture.
If material being
In this
WIL-11260-E-03