Danfoss AME 435 QM Manuale operativo - Pagina 6
Sfoglia online o scarica il pdf Manuale operativo per Azionamenti in corrente continua Danfoss AME 435 QM. Danfoss AME 435 QM 12. Ab-qm (dn 40/50) / ab-qm (dn 50) / ab-qm (dn 65-100)
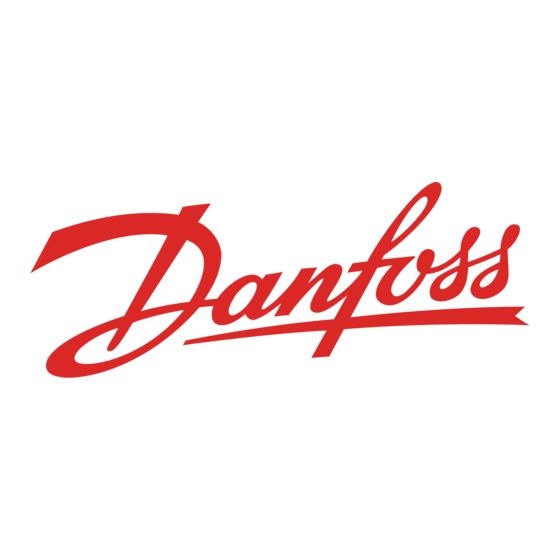
AME 435 QM
ENGLISH
Safety Note
To avoid injury of persons and
damages to the device, it is absolutely
necessary to read and observe these
instructions carefully.
Necessary assembly, start-up, and maintenance
work must be performed by qualified and
authorized personnel only.
Prior to assembly and depressurizing the
system.
Please comply with the instructions of the
system manufacturer or system operator..
Do not remove the cover before the
power supply is fully switched off.
Disposal instruction
This product should be dismantled
and its components sorted, if possible,
in various groups before recycling or
disposal.
Always follow the local disposal regulations.
Mounting and installation
Wiring
❷
Do not touch anything on the PCB!
Switch off the power line before wiring
the actuator! Lethal voltage!
Wire the actuator according to the wiring
diagram.
Part Name
Lead (Pb)
Motor
X
O: Indicates that this hazardous substance contained in all of the homogeneous material for this part is below the limit requirement in GB/T 26572;
X: Indicates that this hazardous substance contained in at least one of the homogeneous material for this part is above the limit requirement in GB/T 26572;
6 | © Danfoss | 2016.10
Functions accessible from cover
RESET ❸
By pushing STAND BY/RESET button for 5 sec.
the actuator starts self stroking procedure to
adjust to the stroke of the valve to which it is
connected.
Procedure starts with extracting the stem.
As the maximum force is detected the actuator
reverse its direction until maximum force in
opposite direction is detected.
During calibration Bi-Color LED blinks green
1/sec. After reaching fully upper end position
actuator enter normal mode and start catching
Y control signal.
Manual override
NOTE:
If manual override has been used then control and
return signal are not correct until the actuator
reaches its end position.
while actuator is mounted on the valve. This
could result in actuator damage.
DIP switch settings
❶
Jumper ①: U/I - Input signal type selector
DIP switches
Factory settings:
ALL switches are in OFF position!
NOTE:
All combinations of DIP switches are allowed.
All functions that are selected are added
consecutively.
Mercury (Hg)
Cadmium (Cd)
Hexavalent Chromium (Cr(VI))
O
O
❹
Do not change preset on AB‑QM
❺
Hazardous Substances Table
Polybrominated biphenyls (PBB)
O
SW 1: Not used
SW 2: 0/2 - Input signal range selector ②
SW 3: D/I - Direct or inverse acting selector ③
SW 4: Fast/Slow: Speed selector ④
SW 5: Not used
SW 6: Not used
SW 7: LOG/MDF - Logarithmic or modified
flow characteristic ❻
SW 8: Not used
LED function indicator
Green – initialization (RESET), set-point position,
transition indicator
Red - indicates STAND BY and Failure mode.
Green:
•
Flashing light (once every 6 sec.) ②
- actuator reached set-point acc. to Y signal
•
No light
- no operation or no power supply
•
Flashing light (~ 1Hz) ③
- self adjusting mode.
Red:
•
No light
- no operation or no power supply
•
Constant light ④
- fault condition occurred
•
Flashing light (2 Hz) ①
- STAND BY
- power supply too low
- initial self-adjusting time too short due to
too short valve strokes
- failure during self calibration.
Dismounting
❽
Dimensions
➒
Polybrominated diphenyl ethers (PBDE)
O
❼
O
VI.A7.D3.7Q