Miller ARC PAK 350 Manuale d'uso - Pagina 14
Sfoglia online o scarica il pdf Manuale d'uso per Sistema di saldatura Miller ARC PAK 350. Miller ARC PAK 350 40.
Anche per Miller ARC PAK 350: Manuale d'uso (47 pagine)
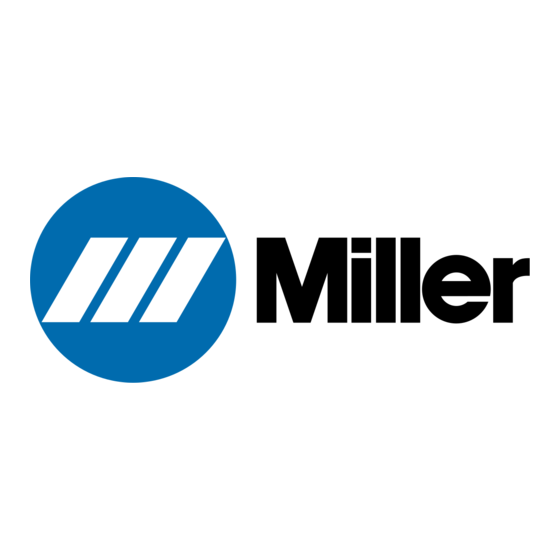
1.
For
Shielded
Metal Arc
Welding (SMAW) (Electrode
Positive/Reverse
Polanty)
a.
Connect
end of electrode holder cable
to
POSI
TIVE
(+)
weld
output
terminal.
b.
Connect
one
end of work cable
to
NEGATIVE
()
weld
output
terminal and
remaining
end
to
workpiece.
-
IMPORTANT: For Electrode
Negative/Straight Polarity
connections,
reverse
cable connections to weld
output
terminals;
electrode becomes
negative.
2.
Fo~
Gas Metal Arc
Welding (GMAW),
Flux Cored
Arc
Welding (FCAW),
and
Submerged
Arc
Welding
(SAW) (Electrode
Positive/Reverse
Polarity)
a.
Connectneendofweldcableto
POSITIVE(+)
weld
output
terminal and
remaining
end
to ter
minal
on
drive
housing
of wire feeder
(see
wire
feeder Owners
Manual for
location).
b.
Connect
one
end of work cable
to
NEGATIVE
()
weld
output
terminal and
remaining
end
to
workpiece.
IMPORTANT: For Electrode
Negative/Straight Polarity
connections,
reverse
cable connections
to
weld
output
terminals;
electrode becomes
negative.
3.
For Gas
Tungsten
Arc
Welding (GTAW) (Electrode
Negative/Straight Polarity)
a.
Connect torch cable
or
connector
to
NEGA
TIVE
()
weld
output
terminal.
b.
Connect
one
end of work cable
to
POSITIVE
(+)
weld
output
terminal and
remaining
end to work-
piece.
IMPORTANT: For Electrode
Positive/Reverse
Polarity
connections,
reverse
cable connections
to
weld
output
terminals;
electrode
(torch)
becomes
positive.
4.
For Air Carbon Arc
Cutting
And
Gouging (ACA)
(Electrode
Positive/Reverse
Polarity)
a.
Connect
torch cable to
POSITIVE
(+)
weld
out
put
terminal.
b.
Connect
one
end of work cable to
NEGATIVE
()
weld
output
terminal and
remaining
end
to
workpiece.
IMPORTANT: For Electrode
Negative/Straight Polarity
connections,
reverse
cable connections
to
weld
output
terminals;
electrode
(torch)
becomes
negative.
4.4.
ELECTRICAL INPUT
CONNECTIONS
INPUT
AA
WARNING: ELECTRIC SHOCK
can
kIll.
Do
not
touch live electrical
parts.
Shutdown
welding
powersource, and discon
nect
input
power
employing lockout/tagging
procedures
before
inspecting
or
installing.
Lockout/tagging procedures
consist of
pad
locking
line disconnect switch in
open
position,
removing fuses from fuse
box,
or
shutting
off and
red-tagging
circuit breaker
or
other disconnect-
ing
device.
A.
ElectrIcal
Input Requirements
Operate
the
welding
power
source
from
a
three-phase,
or
single-phase
if
derated,
50/60
Hertz,
ac
power
supply.
The
input voltage
must
match
one
of the electrical
input
voltages
shown
on
the
input
data label
on
the unit
name
plate.
Contact the local electric
utility
for information
about the
type
of electrical service
available,
how proper
connections should be
made,
and
inspection required.
B.
Jumper
Link InstallatIon
(FIgure
4-1)
a
WARNING: Read and follow
safety
Info
rma
tlon
at
beginning
of entire SectIon 4-4 before
proceedIng.
Jumper
links
are
used to allow the
equipment
to
operate
from different line
voltages.
The
jumper
links may be in
a
bag
attached
to
the
input
terminal board and terminal
strip
11
or
installed for the
highest voltage
shown
on
the
input voltage
label.
1.
Remove
top
cover
and
left
side
panel.
2.
Compare position
of
jumper
links
on
the
input
termi
nal board and terminal
strip
1 T to
the
voltage
link
ar
rangement
shown
on
input voltage
label.
a
CAUTION:
INCORRECT INPUT VOLTAGE
JUMPER LINK PLACEMENT
can
damage
unit.
Position
jumper
links
as
shown
on
the
input
voltage
label
(see Figure 4-1).
Store unused
jumper
links
across
linked
terminals.
3.
Install
jumper
links
onto
the
input
terminal board and
terminal
strip
iT to match
the available
input
line
voltage.
4
Reinstall and
secure
left side
panel
and
top
cover
onto unit.
C.
Welding
Power Source
Input
Power Connec
tions
(Figure 4-1)
a
WARNING: ELECTRIC SHOCK
can
kill.
Do
not
touch live electrical
parts.
Install
a
fusible line disconnect switch
in the
input
circuit
to
the
welding
power
source.
Connect
input
conductors
to the
welding
power
source
before
connecting
to
single-
phase
or
three-phase input
power.
Read and follow
safety
information
at
be
gin-
fling
of entire
Section
4-4
before
proceeding.
The line disconnect switch
provides
a
safe and
convenient
means
to
completely
remove
all
electrical power from the
welding
power
source
whenever it is
necessary
to
inspect
or
service
the unit.
OM-126 853
Page
10