Armstrong 4360 Manuale di installazione e istruzioni per l'uso - Pagina 7
Sfoglia online o scarica il pdf Manuale di installazione e istruzioni per l'uso per Pompa dell'acqua Armstrong 4360. Armstrong 4360 14. Vertical in-line pump
Anche per Armstrong 4360: Manuale di installazione e istruzioni per l'uso (12 pagine)
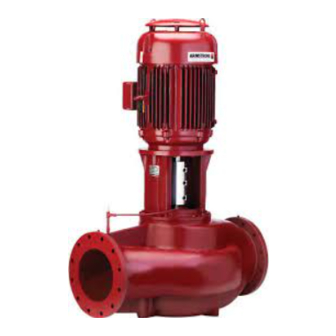
2.2.6
Where required, additional floor support may be used as shown
in Fig. 2.6. Note that the pump should not be rigidly attached
to the column. Leave a small gap between pump and column or
install a 'waffle' isolation pad under the pump. It is critical that
piping be installed in such a manner that the pump does not
become a pipe support.
2.2.7
Fig. 2.7 illustrates stanchion plates at the pump inlet and outlet
ports that may be supplied for installation convenience.
Isolation pads must be used under the legs and monitored as
pipe hangers are adjusted to ensure the pump flanges are not
supporting the piping. Bolting to the floor or housekeeping pad
is not recommended. If the stanchions are bolted down the
bolts must be isolated from the stanchion or an inertia base
and flexible pipe connectors should be used.
2.2.8
Fig. 2.8 illustrates installations with stanchion plates for seismi-
cally active regions. Seismically rated isolation pads or snub-
bers with bolts isolated from the stanchion plates are installed
to restrain the pump during a seismic event. Pipe hangers carry
the weight of the equipment as seismic components are
designed only to restrain the equipment during a seismic event.
2.2.9
Close coupled in-line units (Series 4360 & 4380) up to 15 hp /
11 kW may be installed with the shaft horizontal. (Fig. 2.9) For
horizontal mounting of large units or Series 4300 Split-Coupled
style consult the factory. (Fig. 2.9)
2.2.10
Many Vertical In-Line pumps are piped successfully into
grooved piping systems. In-line pumps are supported well by
grooved piping however flange adapter locking devices or a
welded flange at the pump should be used to prevent the possi-
bility of pipe mounted pumps rotating in the piping. Armstrong
offers grooved suction guides with cast-in outlet flanges and
triple function Flo-Trex valves with inherent locking devices to
prevent this possibility. (Fig. 2.10)
2.2.11
Do not support the unit by the motor eye bolts (Fig. 2.11) or by
any other part of the motor.
2.2.12
Connecting the pump to a permanent rigid base (Fig. 2.12). is
not recommended unless isolated from the piping by flexible
Commercial pumps Series 4300, 4360 and 4380
Vertical In–Line pump
connectors and the base isolated from the building structure
on an inertia base. (Fig. 2.12 is generally acceptable when using
plastic piping).
important:
All Series 4300 pumps contain a tapped hole in the motor
bracket above the discharge flange (see Fig. 2.13) for draining
the well. Pipe this drain hole to a floor drain to avoid overflow
of the cavity caused by collecting chilled water condensate or
from seal failure.
2 .3 pump piping – gener al
Never connect a pump to piping, unless extra care is taken to
measure and align the piping flanges well. Always start piping
from pump.
Use as few bends as possible and preferably long
radius elbows.
Do not use flexible connectors on the suction or discharge of a
Vertical In-Line pump, unless the pump is rigidly mounted to
a foundation.
Ensure piping exerts no strain on pump as this could distort
the casing causing breakage or early failure due to pump
misalignment.
All conecting pipe flanges must be square to the pipework and
parallel to the pump flanges.
Suction and discharge pipes may be increased or decreased at
pump nozzle to suit pump capacity and particular conditions of
installation. Use eccentric reducers on suction connection with
flat side uppermost.
Layout the suction line with a continual rise towards the pump
without high points, thus eliminating possibility of air pockets
that may prevent the pump from operating effectively.
A strainer of three or four times the area of the suction pipe,
installed in the suction line, will prevent the entrance of foreign
materials into the pump. C/af" (5 mm) diameter perforations in
the strainer is typical.
i n sta l la tio n &
o p er at i ng instr uct io ns
7