- ページ 4
アクセサリー Axis Industries SDU-1MのPDF 技術説明、取扱説明書をオンラインで閲覧またはダウンロードできます。Axis Industries SDU-1M 12 ページ。 Ultrasonic flow sensor
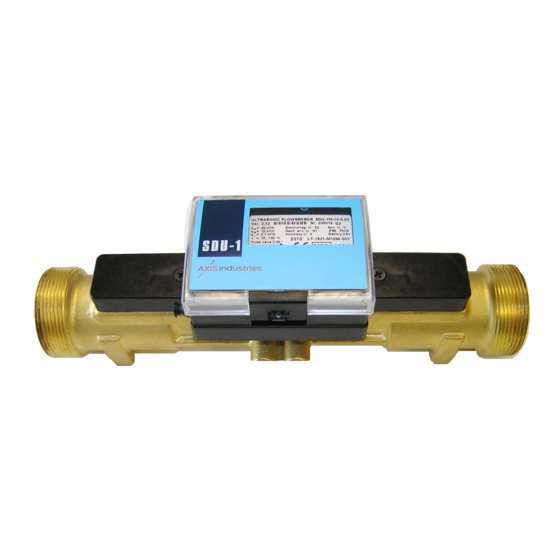
2.5.Table of default settings of the pulse value depending on the permanent flow rate and sensor size:
Permanent flow q
, m3/h
p
Pulse value, liter/ pulse
Other pulse value settings could be selected according user needs by ordering the flow sensor.
The pulse value is also indicated on the label of the flow sensor.
2.6.
The two modes of output pulse transmission are possible: passive (open drain) and active. The
output pulses can be selected by choosing the location of the jumper JP (appendix B)
2.6.1. The passive output pulse transmission mode is set when jumper JP is located on the 2 and 3
pins (lower position). The circuit of connection to the device output pulse terminal is shown below.
The drain supply voltage ranges
The maximum drain current
The output pulse circuit meets „OD" class requirements.
Load resistance R
must be chosen in accordance to avoid of exceeding the maximum drain current.
D
2.6.2. The active output pulse transmission mode is set when jumper JP is located on the 1 and 2 pins
(upper position). Such pulse transmission mode is recommended to use for transferring pulses to heat
energy calculator.
The voltage ranges during the pauses between pulse transmissions +3,0... + 3.6 V
The voltage ranges during the pulse transmission
The output pulse circuit meets „OD" class requirements.
2.6.3. In the case of normal operating of the flow sensor the output pulses are transmitted in
"meander" style frequency packages every second. The period of signal is not shorter than 4 ms, the
durations of the high and low level signal are not shorter than 2 ms.
In the cases of the opposite flow, q < 0,2 q
high and no pulse transmission appears.
In the case of device error the logical signal level is low. The external devices that can analyze
the output pulse signal level (for example: heat energy calculator SKS3) can detect the situation of
device error if the low signal level lasting longer than 2 second.
2.7.
Device status testing.
Visually the device status can be tested by pushing the test button (that is located on the inner
device panel - see appendix B) and observing the indication of green and red light emission diodes
(LED). Other way of recognizing the device status is possible by analyzing the logical status of pulse
output signal and direction (D) output signal:
Device status
Green LED
1. Normal flow
Blinking light
2. Opposite flow Blinking light
3. Empty pipe
Steady light
4. Device error
No light
5. q > 1,1 q
No light
s
6. q < 0,2 q
Steady light
i
PESDU1M02 (MID)
3,5
6
0,02
0,02
+3 ... +24 V
30 mA
(1)
(1)
Red LED
No light
Blinking light
No light
Steady light
Blinking light
Blinking light
10
15
0,05
0,05
0 ... + 0,6 V
or empty pipe condition the logical signal level is
i
Output pulse
Transmission of pulses
High level
High level
Low level
Amount of pulses
corresponds to q = 1.1 q
High level
25
40
0,2
0,2
Direction
Error
output (D)
output (E)
Low level
Low level
High level
Low level
Low level
High level
Low level
High level
Low level
Low level
s
Low level
Low level
60
0,5
4