- ページ 4
水ポンプ ARO PP30A SeriesのPDF 取扱説明書をオンラインで閲覧またはダウンロードできます。ARO PP30A Series 13 ページ。 3" dry powder diaphragm pump
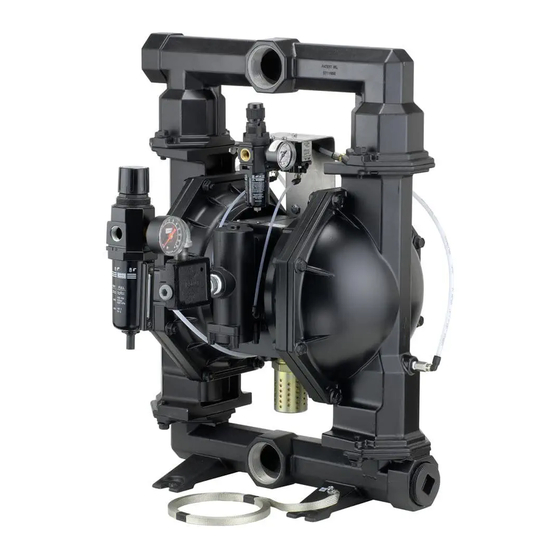
excess material before the pump shuts down. Restart can
compress some powders to a solid that may cause the pump
to fail. The pump should cycle until most of the powder has
been purged before it is shut down.
Calibration procedure on initial start-up:
NOTE: Once these parameters are established for your spe-
cific application, they should not need to be changed.
1. Turn the flow and pressure on the (248) filter / regulator
all the way up.
2. Slowly decrease pressure and flow until pump begins to
labor (work harder).
3. Increase pressure and flow back to a point where the
pump begins to run smoothly. This will optimize the air-
to-powder mix and will help to establish the most effi-
cient working parameters.
If the pump should begin to cycle slowly (bog down), the
powder can be purged by depressing restart button. This will
stop the pump and restart the aeration cycle and allow time
to increase air flow to the aeration ports for proper material
movement.
IMPORTANT
SHUT DOWN PROCEDURE - TO HELP PREVENT PACK-OUT
It is good operating practice to dry cycle the pump 5 - 10
seconds at the end of each dispense cycle. This can be ac-
complished by closing off the powder source at the suction
of the pump or pull wand from material. This will help clear
the pump chambers of any residual powder.
Failure to insure proper fluidization can
CAUTION
result in internal parts breakage and pump failure.
MAINTENANCE
Refer to the part views and descriptions as provided on page
6 through 11 for parts identification and Service Kit informa-
tion.
Keep good records of service activity and include pump
y
in preventive maintenance program.
Certain ARO "Smart Parts" are indicated which should be
y
available for fast repair and reduction of down time.
Service kits are divided to service two separate dia-
y
phragm pump functions: 1. AIR SECTION, 2. FLUID SEC-
TION. The FLUID SECTION is divided further to match
typical part MATERIAL OPTIONS.
Provide a clean work surface to protect sensitive internal
y
moving parts from contamination from dirt and foreign
matter during service disassembly and reassembly.
Before disassembling, empty captured material in the
y
outlet manifold by turning the pump upside down to
drain material from the pump.
y Loctite® and 242® are registered trademarks of Henkel Loctite Corporation y ARO® is a registered trademark of Ingersoll-Rand Company y
y Santoprene® is a registered trademark of Monsanto Company, licensed to Advanced Elastomer Systems, L.P. y 271™ is a trademark of Henkel Loctite Corporation y
Page 4 of 12
y Lubriplate® is a registered trademark of Lubriplate Division (Fiske Brothers Refining Company) y
SCHEMATIC CIRCUIT
Air / Nitrogen
95077
119309-103
Left
CP10-B
Exh 24130
TROUBLESHOOTING
Product discharged from exhaust outlet.
Check for diaphragm rupture.
y
Check tightness of (14) diaphragm screw.
y
Motor blows air or stalls.
Check (176) check valve for damage or wear.
y
Check for restrictions in valve / exhaust.
y
Low output volume, erratic flow, or no flow.
Check air supply.
y
Check for plugged outlet hose.
y
Check for kinked (restrictive) outlet material hose.
y
Check for kinked (restrictive) or collapsed inlet material
y
hose.
Suction hose must be a non-collapsing type, conductive
y
and capable of pulling a high vacuum (up to 30" mer-
cury).
Check all joints on the inlet manifolds and suction con-
y
nections. Connection must be air tight.
Inspect the pump for solid objects lodged in the dia-
y
phragm chamber or the seat area.
4 2
12
14
A212PD
2
2
Right 4
4
1
2
H254PS
1
94977
3
Figure 2
PP30A-XXX-XXX (en)
CP10-B