BD Sensors DMK 351 운영 매뉴얼 - 페이지 2
{카테고리_이름} BD Sensors DMK 351에 대한 운영 매뉴얼을 온라인으로 검색하거나 PDF를 다운로드하세요. BD Sensors DMK 351 2 페이지. Pressure transmitter
BD Sensors DMK 351에 대해서도 마찬가지입니다: 설치 지침 (2 페이지), 운영 매뉴얼 (2 페이지)
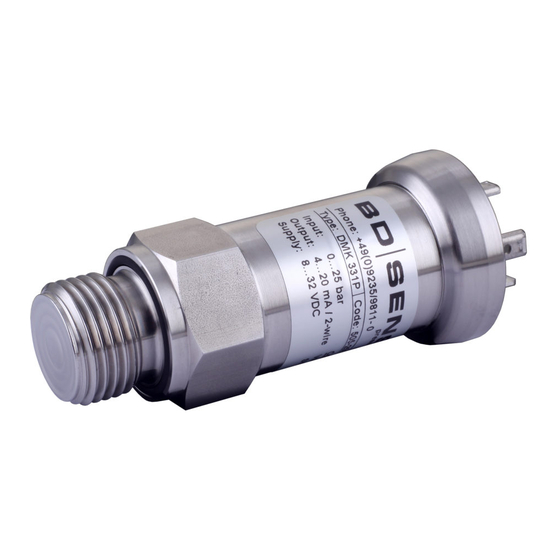
3.4 Installation steps for EN 837
- Use a suitable seal, corresponding to the medium and the
pressure input (e. g. a cooper gasket).
- Ensure that the sealing surface of the taking part is per-
fectly smooth and clean. (R
6.3)
Z
- Screw the device into the corresponding thread by hand.
- Tighten it with a wrench (for G1/4": approx. 20 Nm; for
G1/2": approx. 50 Nm).
- The indicated tightening torques must not be
exceeded!
- Note: permitted pressure ranges according to
EN 837!
for G1/4" and G1/2" according to EN837:
G1/4"
Counterpart has to be
P
≤ 600 bar
N
EN837
of steel according to
DIN17440 with stren-
G1/2"
gth
P
≤ 1000 bar
EN837
N
Rp0,2 ≥ 190 Nmm2
G1/4"
P
> 600 bar,
Counterpart has to be
N
EN837
P
≤ 1000 bar
of steel according to
N
DIN17440 with stren-
G1/2"
P
> 1000 bar,
N
gth
EN837
P
≤ 1600 bar
N
Rp0,2 ≥ 260 Nmm2
3.5 Installation steps for NPT
- Use a suitable seal (e. g. a PTFE-strip).
- Screw the device into the corresponding thread by hand.
- Tighten it with a wrench (for 1/4" NPT: approx. 30 Nm; for
1/2" NPT: approx. 70 Nm).
- The indicated tightening torques must not be
exceeded!
3.6 Installation steps for flare
- Cut the end at right angle to the piping and remove all
internal and external burrs.
- Make the flare; depending on the usage, the device has
to be tightened with max. 10 Nm.
- The indicated tightening torques must not be
exceeded!
3.7 Installation steps for internal threads M20x1.5 and
9/16" UNF (for DMP 334)
- Screw the high pressure connection into the internal
thread of the DMP 334 and tighten it properly with approx.
160 Nm.
DANGER! The high pressure tube seals metal-to-
metal in the chamfer of the pressure port. No fur-
ther seal is allowed with this high pressure con-
nection. A wrong installation can cause enor-
mous danger!
3.8 Installation steps for dairy pipe
- Check to ensure that the O-ring fits properly into the in-
tended groove in the mounting part.
- Center the dairy pipe connection in the counterpart.
- Screw the cup nut onto the mounting part.
- Then tighten it with a hook wrench.
3.9 Installation steps for Clamp and Varivent
- Use a suitable seal corresponding to the medium and the
pressure input.
- Put the seal onto the corresponding mounting part.
- Center the Clamp or Varivent
connection on the fitting
counterpart with seal.
- Then fit the device with a suitable fastening element (e. g.
semi-ring or retractable ring clamp) according to the sup-
plier's instructions.
3.10 Installation steps for connecting flanges
- Use a suitable seal corresponding to the medium and
pressure input. (e. g. a fiber gasket).
- Put the seal between connecting flange and counter
flange.
- Install the device with 4 resp. 8 screws (depending on
flange version) on the counter flange.
4. Electrical Installation
WARNING! Install the device in currentless condition
only!
Electrical
ISO 4400
connections
supply +
1
supply −
2
3
signal + (only for 3-wire)
shield
ground pin
communication-
RxD
-
interface
TxD
-
GND
-
digital signal
supply +
-
RS485
GND
-
pin A
-
pin B
-
shield
-
Establish the electrical connection of the device according to
the technical data shown on the manufacturing label, the
following table and the respective wiring diagram.
Pin configuration:
Wiring diagrams:
2-wire-system (current)
supply + / in +
p
I
supply – / in -
3-wire-system (current/supply)
supply + / in +
p
supply – / in -
I/U
signal + / out
!
For devices with cable gland as well as cable socket, you
have to make sure that the external diameter of the used
cable is within the allowed clamping range. Moreover you
have to ensure that it lies in the cable gland firmly and
cleftlessly!
!
For the installation of a device with cable outlet following
bending radiuses have to be complied with:
cable without ventilation tube:
static installation :
dynamic application: 10-fold cable diameter
cable with ventilation tube:
static installation :
dynamic application: 20-fold cable diameter
!
Please note for devices with ISO 4400 or Buccaneer plug,
that the cable socket has to be mounted properly to
ensure the ingress protection mentioned in the data
sheet. Please check if the delivered seal is placed
between plug and cable socket. After connecting the
cable fasten the cable socket on the device by using the
screw.
!
On devices with field housings, the terminal clamps are
situated under the metal cap. To install the device
electrically, the cap must be screwed off. Before the cover
is screwed on again, the O-ring and the sealing surface
on the housing have to be checked for damages and if
necessary to be changed! Afterwards screw the metal cap
on by hand and make sure that the field housing is firmly
locked again.
!
Prevent the damage or removal of the PTFE filter which
is fixed over the end of the air tube on devices with cable
outlet and integrated air tube.
For the electrical connection a shielded and twisted
multicore cable is recommended.
If a transition is desired from a transmitter cable with
gauge tube to a cable without gauge tube, we recommend
our terminal box KL 1 or KL 2.
5. Initial start-up
WARNING! Before start-up, the user has to check for
proper installation and for any visible defects.
WARNING! The device can be started and operated by
authorized personnel only, who have read and under-
stood the operating manual!
WARNING! The device has to be used within the tech-
nical specifications, only! (compare the data in the data
sheet)
The transmitter shall be supplied by Limited Energy
Source (per UL 61010) or NEC Class 2 Power Source.
M12x1 /
Binder 723
Binder 723
metal
(5-pin)
(7-pin)
(4-pin)
3
3
1
4
1
2
1
6
3
5
2
4
-
4
-
-
5
-
-
7
-
3
-
1
4
-
3
1
-
2
2
-
4
pressure
5
-
port
A
V
S
V
S
A / V
5-fold cable diameter
10-fold cable diameter
cable-col-
field-hou-
Buccaneer
TRIM TRIO
ours
sing
(4-pin)
DIN47100
IN +
wh (white)
1
IN –
bn (brown)
2
OUT +
gn (green)
3
ye/gn (yel-
low /
4
green)
-
-
-
-
-
-
-
-
-
-
wh (white)
-
-
bn (brown)
-
-
ye (yellow)
-
-
pk (pink)
ye/gn (yel-
low /
-
green)
Devices with an accuracy of 0.1 % FSO have micro-
controlled electronics for processing and improving the
signal. Principally, the processing takes more time as for
analogue sensors, which have only an amplifier. Due to
this longer response time, the output signal follows the
measured value discontinuously. For nearly stable
measured values, this characteristic is secondary. Please
compare the specification of the response time in the data
sheet.
Intelligent
devices
interfaces can also be configured by these electronics.
Offset, span and damping are programmable within the
limits given in the data sheet. For configuring the device,
the programming kit CIS 510 consisting of Adapt 1, Win-
dows
compatible
P-Scale 510, power supply and connecting cable is nec-
essary. This can be ordered additionally from BD SEN-
SORS.
6. Placing out of service
WARNING! Disassemble the device only in current and
pressure less condition! Check before disassembly, if it is
necessary to drained off the media before dismantling!
WARNING! Depending on the medium, it may cause dan-
ger for the user. Comply therefore with adequate precau-
tions for purification.
7. Maintenance
In principle, this device is maintenance-free. If desired, the
housing of the device can be cleaned using a damp cloth and
non-aggressive cleaning solutions, in switched-off state.
With certain media, however, the diaphragm may be polluted
or coated with deposit. It is recommended to define corre-
sponding service intervals for control. After placing the device
out of service correctly, the diaphragm can usually be cleaned
carefully with a non-aggressive cleaning solution and a soft
brush or sponge. If the diaphragm is calcified, it is recom-
mended to send the device to BD SENSORS for decalcifica-
tion. Please note the chapter "Service/Repair" below.
!
A false cleaning of the device can cause an irreparable
damage on the diaphragm. Therefore never use pointed
objects or pressured air for cleaning the diaphragm.
8. Service / Repair
8.1Recalibration
During the life-time of a transmitter, the value of offset and
span may shift. As a consequence, a deviating signal value in
reference to the nominal pressure range starting point or end
point may be transmitted. If one of these two phenomena oc-
curs after prolonged use, a recalibration is recommended to
ensure furthermore high accuracy.
8.2 Return
Before every return of your device, whether for recalibration,
decalcification, modifications or repair, it has to be cleaned
carefully and packed shatter-proofed. You have to enclose a
notice of return with detailed defect description when sending
the device. If your device came in contact with harmful
substances, a declaration of decontamination is additionally
required. Appropriate forms can be downloaded from our
homepage www.bdsensors.com. Should you dispatch a
device without a declaration of decontamination and if there
are any doubts in our service department regarding the used
medium, repair will not be started until an acceptable
declaration is sent.
If the device came in contact with hazardous
substances, certain precautions have to be
complied with for purification!
9. Disposal
The device has to be disposed of according to the
European
Directives
2003/108/EG (on waste electrical and electronic
equipment). It is prohibited to place electrical and
electronic equipment in domestic refuse!
WARNING! Depending on the used medium, deposit on
the device may cause danger for the user and the envi-
ronment. Comply with adequate precautions for purifica-
tion and dispose of it properly.
10. Warranty conditions
The warranty conditions are subject to the legal warranty pe-
riod of 24 months from the date of delivery. In case of improper
use, modifications of or damages to the device, we do not ac-
(4-pin)
cept warranty claims. Damaged diaphragms will also not be
1
accepted. Furthermore, defects due to normal wear are not
2
subject to warranty services.
3
11. Declaration of conformity / CE
4
The
delivered
device
The applied directives, harmonised standards and documents
are listed in the EC declaration of conformity, which is available
-
-
online at: http://www.bdsensors.com.
Additionally, the operational safety is confirmed by the CE sign
-
on the manufacturing label.
-
-
-
-
with
optional
communication
programming
software
2002/96/EG
and
fulfils
all
legal
requirements.
BA_DMU-ES_OEM_E_22.08.2017