DUSS DIA 303 S 운영 지침 - 페이지 2
{카테고리_이름} DUSS DIA 303 S에 대한 운영 지침을 온라인으로 검색하거나 PDF를 다운로드하세요. DUSS DIA 303 S 4 페이지. Diamond core drill
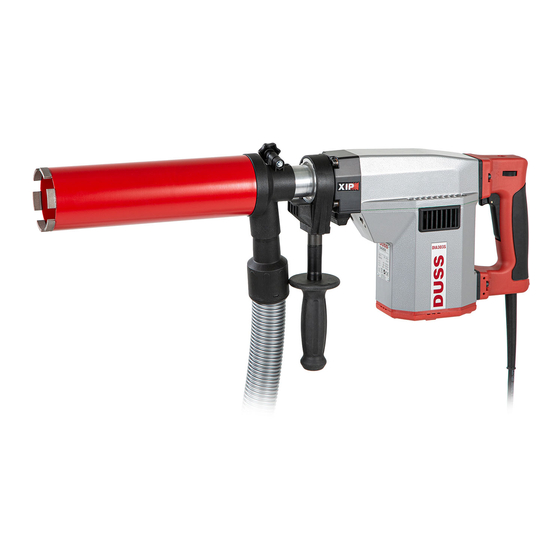
for the field of application.
Inserting and changing tools
The chuck of the diamond core drill with G 1/2" external thread is
located on the drilling spindle. Only use suitable and high-quality tools.
Use cutting tools with good cutting properties. When using diamond
core bits, ensure that the diamond segments still protrude sufficiently
from the core bit tube on the inner and outer diameter. Before mounting
the tool, apply a small amount of dry lubricant spray to the mounting
system.
Loosen the clamping ring of the SK suction head and move it to the
rearmost position. Screw the diamond core bit onto the drill spindle
and tighten it with the enclosed open-end wrench.
Gearshift
The machine features a 3-speed-gearbox, which allows the optimum
speed to be set for each drilling diameter. The preselection of the
speed is made at the gear shift lever (7). Never change gears with force
and only when the machine is running down or stopped. If the gear
lever cannot be moved to the desired position when the machine is at a
standstill, briefly touch the pushbutton switch (4) at the same time. The
recommended speeds for each tool are given in the carrying case.
Soft impact
The soft impact can be easily switched on or off using the change lever
(8) located at the bottom of the drill head. The soft impact accelerates
the work progress in hard materials. Concrete and reinforced concrete
should only be drilled with soft impact.
Symbol „drill" on change lever (8) indicates the position drilling without
soft impact
Symbol „hammer" on change lever (8) indicates the position drilling
with soft impact
Operation
Always comply with recognized accident prevention regulations
and the accompanying safety precautions. In case of functional
failure, have the machine inspected by a qualified electrician befo-
re continuing work.
Before starting work unplug the machine at the mains socket. Make
sure that the swivelling side handle (6) is firmly screwed in at the
desired position. Always hold the machine with both hands when
working and maintain a firm stance.
Continuous operation: Press the pushbutton switch (4) and depress
the trigger lock (3) upwards.
Switch off: Briefly press the pushbutton switch (4).
Infinitely adjustable speed: Pilot drilling is made easier by reducing
the speed. Afterwards, work should always be continued at full speed
and thus full power.
The adjusting dial (2) is ergonomically arranged to permit this either
before or during work.
+ = full speed
- = reduced speed
Dry drilling
Generak information
Pilot drilling always without soft impact, with low contact pressure.
If the tool jams, do not attempt to release it by switching the machine
on and off. Switch the machine off immediately and release the tool
by turning it clockwise and counterclockwise with a suitable open-end
wrench. Carefully pull the tool out of the drill hole.
When drilling, the adjusting dial (2) should always be set to full speed.
The speed should only be reduced for pilot drilling or sharpening on the
sharpening plate etc.
2
Translation of the DIA 303 S original operating instructions
Dust extraction
Dry diamond drilling must always be carried out with dust
extraction. It is necessary that the suction holes around the chuck on
the diamond drill bit are open and that the industrial vacuum cleaner
is attached to the SK suction head. The extraction system not only
enables almost dust-free drilling, but also ensures increased drilling
progress, a longer service life of the diamond core bit and optimum
cooling of the diamond segments. Drilling without dust extraction
damages the diamond segments due to overheating. An industrial
vacuum cleaner with filter cleaning and according to valid directives
(BGIA dust class M) must be used. To achieve a good suction
performance, the industrial vacuum cleaner must be cleaned at regular
intervals.
Hand-held, with centring
Before drilling, a pilot drill hole with drilling dia. 14 mm, by approx.
8 cm deep, must be drilled in the centre of the planned drill hole.
This serves to guide the supplied ZST centring rod, which should be
inserted into the chuck or extension. For pilot drilling with the ZST
centring rod inserted, drill to a depth of approx. 2 cm with the tool,
switch off the machine, remove the ZST centring rod and continue
drilling.
When using the optional SZ quick centring bit, adapted to the tool
length, the pilot drilling is not necessary.
A wooden plate with sawn-in prism in which the core bit is guided can
also serve as a centring aid.
Stand mounted
The machine can be fixed in the BS 160 drill stand (up to max. drilling
range 202 mm) with the mounted side handle (6). For stand mounted
dry drilling, the TBS dry extraction system (optional) must also be
mounted between the chuck and the diamond core bit. This must be
lubricated from time to time with dry lubrication spray.
For easy pilot drilling, attach the optional BS 160-ABH centring aid to
the drill stand (necessary for large diameters).
Drilling
Work with sufficient contact pressure when drilling without soft
impact. If it is too low, the diamonds tend to polish. In this case, the
drilling progress becomes less and less until finally no more material
is removed. This can only be corrected by briefly drilling in the SP
sharpening plate.
Drilling with soft impact
Select moderate contact pressure when drilling with soft impact, let the
core bit „work" in conjunction with the soft impact. Especially as soon
as reinforcement is drilled through in order to reduce vibrations.
Ergonomic work
A holder (1) is located on the power tools switch handle, into which an
auxiliary handle (included in the scope of delivery) can be screwed in.
This ensures a comfortable, back-saving posture when working down-
wards (compressor setting).
Overload indicator
The overload indicator (5) is located at the lower part of the switch
handle and serves to check the machine load. The display of the
different operating modes is done by means of a green LED light.
Functional description
Continuous green light:
Unit switched on and machine load is low to optimum.
Flashing green light, slow:
Machine is overloaded, the contact pressure must be reduced.
Flashing green light, fast:
Machine has reduced speed due to overload. The contact pressure
must be reduced.
Green light went out:
Machine has switched off due to overload and must be switched off
and on again. Alternatively, the machine is not switched on.
www.duss.de