Armstrong 4360 설치 및 운영 지침 매뉴얼 - 페이지 8
{카테고리_이름} Armstrong 4360에 대한 설치 및 운영 지침 매뉴얼을 온라인으로 검색하거나 PDF를 다운로드하세요. Armstrong 4360 14 페이지. Vertical in-line pump
Armstrong 4360에 대해서도 마찬가지입니다: 설치 및 운영 지침 매뉴얼 (12 페이지)
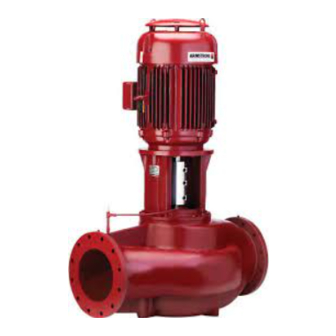
i n sta l l at i on &
op era t i ng i n str u ct i on s
8
In open systems, test suction line for air leaks before starting;
this becomes essential with long suction line or static lift.
Install, at the pump suction, a straight pipe of a length
equivalent to 4 or 6 times its diameter; this becomes essential
when handling liquids above 120°f (49°c). Armstrong suction
guides may be used in place of the straight pipe run and in-
line strainer.
Install an isolation valve in both suction and discharge lines on
flooded suction application; these valves are used primarily to
isolate the pump for inspection or repair.
Install a non-slam non-return check valve in discharge line
between pump and isolation valve to protect pump from
excessive back pressure and to prevent water running back
through the pump in case of driver failure on open systems.
An Armstrong Flo-Trex valve may be used in place of non-
return check valve and isolation valve on pump discharge.
caution:
Only the discharge valve is to be used to throttle pump
A
flow, not the suction valve. Care must be taken in the
suction line layout and installation, as it is usually the
major source of concern in centrifugal pump applications.
2 . 4 alignment
Alignment is unnecessary on close-coupled pumps, Series
4360 & 4380, as there is no shaft coupling.
Series 4300 units are accurately aligned at the factory prior to
being shipped and do not need re-aligning when installed.
Alignment on a Series 4300 unit may be verified by assuring an
equal and parallel gap between coupling halves on both sides of
the coupling.
oper ation
2 .5 starting the pump
Ensure that the pump turns freely by hand, or with
some gentle mechanical help such as a strap or Allen
key in coupling bolt.
Ensure that all protective guarding is securely fixed in position.
Commercial pumps Series 4300, 4360 and 4380
Vertical In–Line pumps
The pump must be fully primed on start up. Fill the pump cas-
ing with liquid and rotate the shaft by hand to remove any air
trapped in the impeller. On Series 4300 any air trapped in the
casing as the system is filled must be removed by the manual
air vent in the seal flush line. Ensure entrained air is removed
from series 4300 pumps, prior to starting, through the air
vent on the seal flush line. Open vent until clear of air.
Series 4360 & 4380 units are fitted with seal flush/vent lines
piped to the pump suction area. When these units operate re-
sidual air is drawn out of the pump towards the suction piping.
'Bump' or energize the motor momentarily and check that the
rotation corresponds with the directional arrow on the
pump casing.
To reverse rotation of a three phase motor, interchange any
two power leads.
Start the pump with the discharge valve closed and the suction
valve open, then gradually open the discharge valve when the
motor is at operating speed. The discharge valve may be open
slightly at start up to help eliminate trapped air.
When stopping the pump: Close the discharge valve and
de-energize the motor.
Do not run the pump against a closed discharge valve for an
extended period of time (a few minutes maximum).
Star-Delta motor starters should be fitted with electronic/me-
chanical interocks that have a timed period of no more than 40
miliseconds before switching from star (starting) to delta (run)
connection yet allow the motor to reach full star (starting)
speed before switching to delta (run).
Should the pump be noisy or vibrate on start-up a common
reason is overstated system head. Check this by calculating the
pump operating head by deducting the suction pressure gauge
value from the discharge gauge reading. Convert the result into
the units of the pump head as stated on the pump nameplate
and compare the values. Should the actual pump operating
head be significantly less than the nameplate head value it is
typically permissable to throttle the discharge isolation valve
until the actual operating head is equal to the nameplate value.
Any noise or vibration usually disappears. The system
designer or operator should be made aware of this as some
adjustment may be required to the pump impeller diameter or
drive settings, if applicable, to make the pump suitable for the
system as installed.