Drain-All 870100 Installation Manual - Page 3
Browse online or download pdf Installation Manual for Control Unit Drain-All 870100. Drain-All 870100 12 pages.
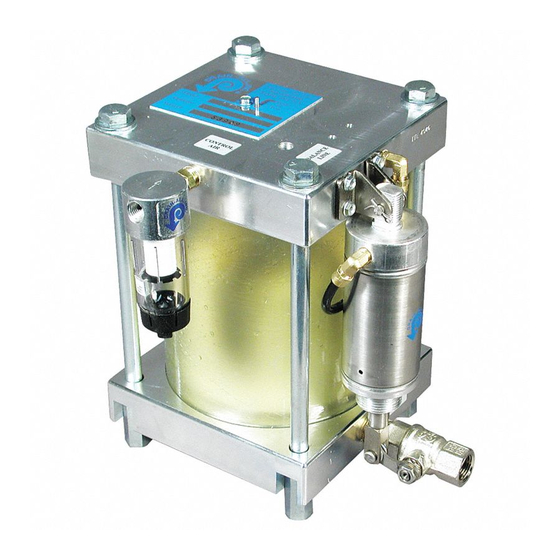
- 1. Table of Contents
- 2. Specifications
- 3. Installation
- 4. Start-Up & Troubleshooting
- 5. Dimensional Print
- 6. Product Technology How It Works
- 7. Component Parts Drawing
- 8. Parts & Materials of Construction
- 9. Frequently Asked Questions
- 10. Drain-All Solves Problems
- 11. Warranty
- 11. Drain-All, Inc
- 11. PO Box 609
- 11. Louisville, TN, USA
START-UP
1. Close control air line and balance line
needle valves as well as inlet isolation
shut-off valve.
2. Bring up system pressure.
3. Fully open control air needle valve.
Check for leaks in control air line. Push
the "Push to Test" button on top of the
Model 1700
to verify the air cylinder
TM
strokes, opening the discharge ball valve.
Leave control air needle valve open.
4a. Applications where the balance line
is connected back to vessel being
drained. Fully open the balance line nee-
dle valve. Check for air leaks on balance
line and fittings. Leave balance line nee-
dle valve fully opened. The needle valve
can be used as an isolation shut-off valve.
4b. Applications where the balance line
needle valve is vented to atmosphere
or connected to a header pipe leaving
the vessel being drained. Open the bal-
ance line needle valve only enough to
ensure a small amount of air can flow
through it. This will be adjusted in a later
step.
5. Gradually open the inlet isolation shut-
off valve to the full open position to
allow liquid to enter the Model 1700
The reservoir will fill until the float is
raised to the upper position actuating the
control circuit extending the air cylinder
and opening the ball valve. Once the dis-
charge starts, the liquid level in the
Drain-All reservoir begins to lower. This
lowers the float back to its original posi-
tion which deactivates the control circuit
closing the ball valve.
6a. Applications where the balance line
needle valve is vented to atmosphere
or connected to a header pipe leaving
the vessel being drained. With liquid in
the reservoir and the liquid discharge ball
valve in the closed position, close the
balance line needle valve. As you slight-
ly open the balance line needle valve,
look into the translucent sleeve just
above the inlet port and look for a trickle
022802 Model 1700-IG
START-UP & TROUBLESHOOTING
of small bubbles. Continue to open the
needle valve until you see these bubbles
indicating a proper setting for the balance
line needle valve. Remember that bub-
bles will only be seen if there is a pres-
sure differential (when balance line is
vented to atmosphere or to a header leav-
ing the vessel being drained).
6b. When the balance line is connected
back to the vessel being drained, there is
no pressure differential between the inlet
and balance line and there will be no
bubbles in the liquid. In this application
keep the balance line needle valve in this
connection fully open. The top of the
Model 1700
of the vessel being drained.
7. Once properly installed, no further
adjustments to the Model 1700
essary. The Model 1700
matic, discharging on demand as needed
when liquid accumulates.
TROUBLESHOOTING
1. Water does not enter.
A. Balance line isolation shutoff valve is
closed which does not allow liquid to
enter the Model 1700
Solution: Adjust balance line needle
valve per installation instructions.
.
TM
B. Liquid inlet shut-off valve is closed.
Solution: Fully open liquid inlet shut-off
valve.
C. Vessel drain, and/or pipe from vessel
drain to Model 1700
Solution: Clear obstruction.
D. Location of balance line connection
causes higher balance line pressure than
liquid inlet pressure. Model 1700
"back flowing".
Solution: Refer to installation instruc-
tions for proper balance line installation.
2. Fills and will not drain.
A. Control air line needle valve is closed,
or not fully open.
Solution: Fully open control air needle
valve to full open.
must be below the bottom
TM
are nec-
TM
is fully auto-
TM
.
TM
inlet is plugged.
TM
TM
Page 3
B. Lack of adequate air pressure on con-
trol air line.
Solution: Provide more than the mini-
mum required PSIG to control air line
connection per the product specification.
If there is not enough control air pressure
available, there are lower control air
pressure options available - contact your
distributor for details.
C. Hole in valve stem clogged.
Solution: Clear obstruction. Do not alter
hole diameter.
D. Filter element clogged or dirty.
Solution: Replace part.
3. Discharge ball valve stays open.
A. Center tube magnet installed upside
down, i.e., north and south poles
reversed.
Solution: Reinstall center tube magnet
rotating it 180 degrees, end for end.
B. Bleed hole for air cylinder clogged.
Solution: Clear bleed hole on side of air
cylinder located on opposite side from
control air connection to the cylinder. Do
not alter hole diameter.
C. Center tube magnet stuck or not prop-
erly sealing against valve stem. This can
result from excessive oil and water con-
taminates allowed to get into the control
air lines and then into the center tube,
thereby coating the center tube magnet
and causing it to stick.
Solution: Clean center tube and center
tube magnet and reassemble. Also, if
possible, connect the control air line to a
clean dry air source which will prevent
reoccurrence.
4. Excessive bubbling action in reser-
is
voir.
A. Air leak in balance line and/or fittings.
Solution: Refer to installation instruc-
tions and start-up procedures.
B. Balance line needle valve opened too
far.
Solution: Adjust balance line needle
valve per installation instructions.