Elektra Beckum hobbymaster MIG/MAG 160 Operating Instructions Manual - Page 7
Browse online or download pdf Operating Instructions Manual for Welding System Elektra Beckum hobbymaster MIG/MAG 160. Elektra Beckum hobbymaster MIG/MAG 160 10 pages.
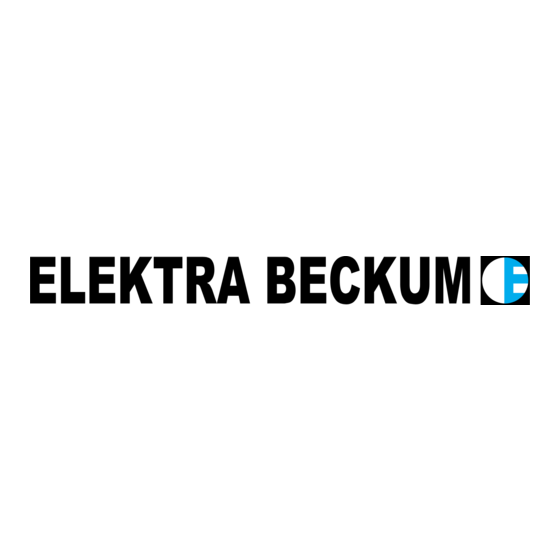
Care and Maintenance
The unit is nearly maintenance-free.
B
Danger – Voltage!
Disconnect from power before servicing!
· Check feed roller, pressure roller and wire lead-
in nozzle at regular intervals for dirt build-up,
clean if necessary.
· At appropriate intervals the complete torch
including torch leads should be cleaned, as
rubbed-off parts and dust build-up inside.
· The torch's contact tip is a wearing part. If its ori-
fice has enlarged the contact tip must be
replaced.
· On the inside of the plug-on gas shroud spatters
build up. These have to be removed when nec-
essary. An anti-spatter spray eases this job and
keeps spatters from sticking to the shroud.
· Replace damaged cables without delay.
Trouble Shooting
Mechanical faults are mostly indicated by an irregu-
lar or completely blocked wire feed. Electrical faults
cause a malfunction of the unit, in part or complete.
B
Danger - Voltage!
Electrical fault finding must be left to a quali-
fied electrician.
Further fault finding can proceed according to the
wiring diagram supplied.
Fault find should first start with the unit de-ener-
gized, and in the following order:
1. Check of the power supply cable connection
and all other connections on switches, trans-
former and choke, as well as all plug-and-socket
connections and soldered connections for tight-
ness.
2. Check of fuse for continuity and contact.
3. Visual check for possible shorts or overloads of
windings (discoloring).
MIG/MAG 140/160
Fault, Likely causes
•
Noisy or unstable arc?
Incorrect welding volt-
age
Too much/too little wire
feed
Earth clamp loose or
high contact resistance
(rust, paint)
Contact tip worn or
incorrect diameter
Incorrect gas flow rate
setting
Workpiece not clean in
seam area
Power unit faulty
Spiral liner dirty
Wire feed faulty
•
Excessive spattering
Wire feed rate too high
Welding voltage too
high
Workpiece not clean
•
Wire feed motor does not run
No power
Welding step switch in
"0" position
Torch trigger switch not
activated
Fuse blown
Motor faulty
• No wire feed
Pressure roller loose
Wire kinked at wire
feed
Groove in feed roller
worn
Electrode wire stuck to
contact tip
• Machine shuts down, overload control light
comes on
Duty cycle exceeded
Power unit faulty
Remedy
Correct with welding step
switch
Correct with wire feed pot
Ensure good contact
between earth clamp and
workpiece
Replace
Correct
Remove paint, rust, grease
etc.
Have machine checked by
service centre
Clean or replace
See below
Correct with wire feed pot
Correct with welding step
switch
Clean
Check power supply
Set to a welding step
Activate torch trigger switch
Have replaced by a qualified
electrician
Have repaired by service
centre
Increase pressure of leaf
spring with knurled thumb
screw
Adjust wire lead-in nozzle
Replace
Replace contact tip, if wire is
deformed, reduce pressure
of pressure roller
Let machine cool down,
observe duty cycle stated on
nameplate
Have repaired by service
centre.
1.5