Duff-Norton DM3804 Installation, Operation And Maintenance Instructions - Page 10
Browse online or download pdf Installation, Operation And Maintenance Instructions for Controller Duff-Norton DM3804. Duff-Norton DM3804 16 pages. Rotating ball screw actuators
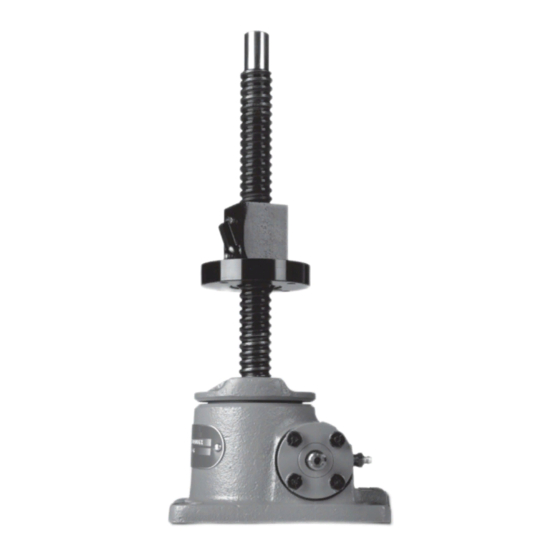
away from ball screw threads.
6. Thread locknut (20) on ball screw (5) and tighten
securely against worm gear (6). Make certain
that this assembly is tightly drawn up.
Note
On some locknuts the tapped set screw hole is
not centered. In this case assemble the locknut
with the tapped hole farthest away from the
worm gear face.
7. Install set screw (21) in locknut (20) locking the
nut in place (some models do not utilize a set
screw).
Note
If new parts have been installed it may be
necessary to respot holes fro set screws.
8. Press worm bearings (15) on worm (14) making
sure that bearings are seated properly against
worm shoulder.
Note
When tapered roller bearings are used, the
small end of the cones should point to the end of
the worm shaft.
9. Inverted units only - Install guide bushing (16) in
shell (3). Guide bushings must be flush with
base. With a center punch, lock guide bushing in
place by peening on thread O.D. of bushing and
shell.
10. Install bottom load bearing (8) in shell (3).
Note
For actuators with tapered roller load bearings,
install bearing cup.
11. Install worm (14) and bearing (bearing cone)
assembly (15) in shell. For units with tapered
roller worm bearings, installed bearing cups in
shell.
For 1/2-ton Models - Slide thrust race (15b),
needle bearing (15a) and second thrust race
(15b) on each end of worm (14) and position
worm in shell (3).
Note
For some units it is easier to assemble worm
(14) and bearing assembly (15) after worm gear
(6) is in place. See Step 11.
12. Press oil seals (13) in flanges (11).
Note
The sealing element of the seal should face
inward. Seals are not required on 1/2-ton mod-
els.
13. Assemble worm flanges (11) with shims (12) and
bolt in place with cap screws (9) and
10
lockwashers (10). Care should be taken to
prevent cutting of seal on worm keyway.
For 1/2-Ton Models - Slide bushings (11a) over
each end of worm shaft (14) and thread bush-
ings into shell (3) until they are positioned to
control lateral movement of worm to within .002
inches. Bushings should be equally threaded
into each end of shell. Lock bushings in place
with set screws (9a).
Note
If new parts have been installed, lightly spot-drill
bushings prior to locking in place with set
screws.
14. Install ball screw (5) and worm gear assembly
(6).
Note
For some units it is easier to install worm and
bearing assembly after worm gear (6) and ball
screw (5) assembly are in place. See Step 11.
Note
After worm, worm gear and ball screw assembly
are in place and flanges (11) are assembled,
strike each end or worm shaft sharply with a soft
face hammer to seat bearing properly. Recheck
flange bolts for tightness. Worm should turn
freely with minimum drag and end play. If too
much end play is present, remove shims as
required. If worm does not turn freely, add shims
as required.
15. Assemble top load bearing (7) on worm gear (6).
Note
For units with tapered load bearings, install
bearing cup in shell cap (2).
16. Fill shell (3) approximately one half full of grease
and install grease fitting (17).
17. Install shell cap (2) and screw down tight.
Note
Shell cap flange does not necessarily have to
bear against top of shell, there will usually be a
gap. This will put a light drag on worm. If worm
is hard to turn, back off slightly on shell cap.
18. Install set screws (1) in shell cap (2). Tap shell
cap sharply with hammer and re-tighten set
screw.
Note
If new parts have been installed, it may be
necessary to respot holes for these screws.
19. All models except those with expansion plugs -
Install pipe (4) in shell (3) for upright models or
in shell cap (2) for inverted models.