Duro Dyne CCD-110N Owner's Manual - Page 2
Browse online or download pdf Owner's Manual for Welding System Duro Dyne CCD-110N. Duro Dyne CCD-110N 8 pages. Pinspotter
Also for Duro Dyne CCD-110N: Owner's Manual (17 pages)
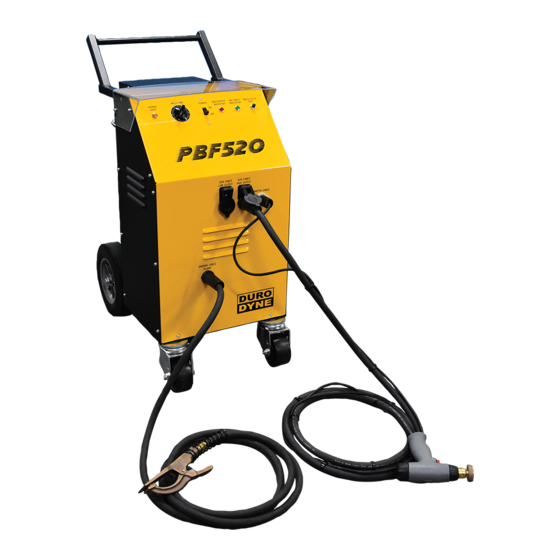
SET UP
SET UP
1. Plug the gun cable camlock
connector into either the high
or low gun female camlock (A).
(The HIGH tap produces about
10 volts, typically used for long
pins or heavy gauge material.
The LOW produces 5 volts,
typically used for light gauge
material.)
2. Plug the switch cable into the
switch cable socket (B).
3. Plug the ground cable cam
lock connector into the ground
female camlock (C).
ELECTRICAL REQUIREMENTS
ELECTRICAL REQUIREMENTS
Connect the PBF520 to a 100 amp power supply. (208-
230 volts - 60 cycle). The PBF520 unit uses 208-230 volt
single phase. To wire to 208-230 volt single phase, the green
lead is ground and the white and black leads are power. It is
suggested that the unit be permanently wired into a 100 amp
disconnect box fitted with 100 amp slow blow fuses. Note:
due to inherent inrush current, it is recommended to use the
next size gauge wire over codes when possible.
PBF520 AS A BENCH TOOL
PBF520 AS A BENCH TOOL
To use your work bench as a welding table, set the PBF520
alongside the work bench. Cover the bench top with a copper
sheet, (.025 inch) which will act as a permanent ground when
the duct work is placed on the table top. Attach the ground
clamp to the duct work or copper bench top. The Clip Pins
will quickly weld every time with no burn marks or wasted
pins due to misfires.
WHEEL PBF520 TO THE WORK
WHEEL PBF520 TO THE WORK
Where the duct is too large to put on a bench, snap the
ground clamp onto the duct and secure the insulation quickly
by welding the Clip Pins inside or outside of the ducts as
required. Eliminate the heat mark on the duct by using the
simple "heat sink" included on opposite the side of weld.
SERVICE
SERVICE
The PBF520 has been designed and built to withstand rugged
shop usage. The Indicator lights on the front panel will help you
to diagnose minor problems. If your PBF520 fails to operate,
follow this simple procedure to find the defective component.
1. Pull the trigger and watch the lights, the green light (24 volts)
and then the red light (220 volts) should flash on and off.
2. If only the green light comes on, go to step 4
3. If neither light comes on, press the WELD CYCLE TEST
switch on the front panel.
a. If both lights flash and the transformer does not hum
go to step 5.
b. If both lights flash and the transformer hums, the
problem is either a bad trigger switch or bad switch
cable.
c. If only the green light flashes, go to step 4
d. If neither light flashes, replace the 24 volt
transformer.
4. Replace the weld activator.
5. The problem is probably a bad weld transformer. Call
technical service for further assistance.
(1-800-899-3876)
TIMER ADJUSTMENT
TIMER ADJUSTMENT
The timer dial facing you on the front panel of the unit, deter-
mines the duration of the weld cycle. For maximum efficiency
of the unit, the weld cycle should be set for the shortest
Timer
length of time necessary to provide a good weld. An excessive
amount of time does not improve the weld. On the contrary,
A
the resulting weld may not be an acceptable one. It is recom-
mended that at the start of a production run, using a given
B
length of pin with a given gauge of metal, the operator take
a few moments to determine the minimum timer setting to
perform the job and leave the timer at that point.
C
NOTE: There is a common misconception that the longer the
weld time, the stronger the weld. This is not true. It is impor-
tant that you follow the above instructions for maintaining
the minimum weld time.
MAINTENANCE
MAINTENANCE
The PBF520 has been designed and built to withstand rugged
shop usage. Constant, trouble-free operation is assured with
a minimum of maintenance. The GUN TIP , the GROUND CLAMP
and all CABLE CONNECTIONS should be kept clean to maintain
a good electrical contact. Wire brush the parts to remove
any oxidation or adhesive that may have accumulated during
the fastening operation.
INSTALLING CLIP PINS
INSTALLING CLIP PINS
Clip Pins are welded as easily as "A", "B", "C".
"A"
"A"
Position the Clip pin on the
Magnetic tip of hand gun.
"B"
"B"
Press down through the insu-
lation, twist the gun, pull the
trigger. Do not release the
trigger until the timer cycle
has ended.
"C"
"C"
The Clip Pins are permanently
welded in position flush with the
insulation.