Datalogic S80-MH-5-YL09 Instruction Manual - Page 2
Browse online or download pdf Instruction Manual for Accessories Datalogic S80-MH-5-YL09. Datalogic S80-MH-5-YL09 2 pages. Distance sensor with laser emission and time of flight measurement.
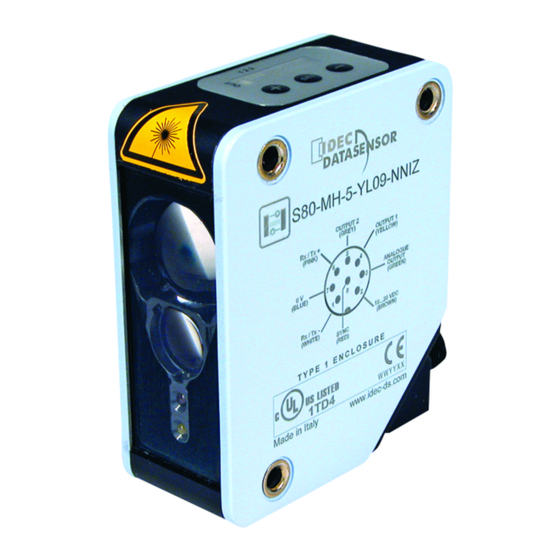
SETTING OF THE PARAMETERS
OUT
Display
Keyboard
OR
1
2
3
Dig1
Dig2
Dig3
Dig4
+
SET
1
9
4
5
Press the SET pushbutton for at least 8s to enter into the parameter setting menu.
The "MEnu" message appears.
OR
1
2
3
Dig1
Dig2
Dig3
Dig4
+
SET
M
E
n
u
Pressing the + and – pushbuttons the user and run up and down the menu, reading the
following messages.
- Maximum distance visualization
- At each pressure of the SET pushbutton, the user can run through the options of the selected level.
OR
1
2
3
Dig1
Dig2
Dig3
Dig4
+
SET
D
_
H
I
DISTANZA
7
0
0
0
- Minimum distance visualization
- At each pressure of the SET pushbutton, the user can run through the options of the selected level.
OR
1
2
3
Dig1
Dig2
Dig3
Dig4
+
SET
d
_
L
o
DISTANZA
0
3
0
0
- Delay setting
- At each pressure of the SET pushbutton, the user can run through the options of the selected level.
OR
1
2
3
Dig1
Dig2
Dig3
Dig4
+
SET
d
-
0
0
d
-
0
5
d
-
1
0
d
-
2
0
d
-
3
0
d
-
4
0
- The delay value setting is in common to both outputs.
- When a delay value, different from zero, is set, the outputs will be maintained active for a
minimum time equal to the number of milliseconds visualised on the display.
- Visualisation of the channel 1 data
- At each pressure of the SET pushbutton, the user can run through the options of the selected level.
OR
1
2
3
Dig1
Dig2
Dig3
Dig4
+
SET
C
H
-
1
THRESHOLD
1
9
4
5
MODE
L/d
-
O
n
- Visualisation of the channel 2 data
At each pressure of the SET pushbutton, the user can run through the options of the selected
level.
OR
1
2
3
Dig1
Dig2
Dig3
Dig4
+
SET
C
H
-
2
THRESHOLD
1
9
4
5
MODE
L/d
-
O
n
- Serial output deactivation
At each pressure of the SET pushbutton, the user can run through the options of the selected
level.
OR
1
2
3
Dig1
Dig2
Dig3
Dig4
+
SET
S
-
o
n
S
-
o
f
- Memorisation of the parameters set
OR
1
2
3
Dig1
Dig2
Dig3
Dig4
+
SET
S
A
V
E
S
A
V
E
- Pressing the SET pushbutton (the SAVE message blinks for 2s, 4Hz) all the changed values
are saved and the user exits from the menu, and returns to the normal mode.
- One of the +/- pushbuttons has to be pressed to return to the setting menu.
- Exit from the parameter setting menu
After a 10 s inactivity of the pushbuttons, the sensor returns to the normal mode visualising the
distance.
REMOTE FUNCTION
KEYLOCK function (SET pushbutton block)
The keyboard block function is activated at powering on, connecting the SYNC terminal to the positive
power supply (+Vdc) for at least 1 s.
-
After the first second, the SYNC input is ready for the normal synchronisation operations (refer to next
paragraph)
To deactivate the keyboard block, the sensor has to be turned off and re-powered maintaining the
SYNC wire not connected or ground connected (GND).
SYNC input (synchronisation)
-
The connection of the SYNC wire to +Vdc corresponds to the passive logic status while SYNC not
connected or connected to 0 V corresponds to the active logic status.
SYNC passive = +Vdc ; SYNC active = 0V
The synchronisation signal allows to calculate the beginning and ending instants of the measurement.
The reading cycle begins after the transition of the SYNC signal from passive to active and the sensor
outputs are updated after max. 400μs.
All the outputs are deactivated after max. 400μs from the active – passive transition.
-
-
-
The SYNC wire is used also to determine the transmission direction when the RS485 serial connection
is used.
RS485 serial connection
The serial communication parameters are: 9600 baud, non-parity, 8 data bits, 1 stop bit.
The refresh time of the serial port is 35 ms.
The SYNC input is used to determine the communication direction, and in particular if low (active)
direction S80->User, if high (passive) User->S80.
With SYNC active, the sensor continuously transmits the detected distance value (with a precision of
14bit) by means of a binary data format. 3 byte are used; one with bit 0 at logic level 1 identifies the less
important byte, second with bit 6 at logic level 1 and bit 7 at logic level 0 identifies intermediate byte,
third with bit 6 at logic level 1 and bit 7 at logic level 1 identifies more important byte.
7
1
1
0
0
0
-
7
0
1
D11
D10
D9
7
D6
D5
D4
D3
D2
Low signal received condition, corresponding to "FFFF" display indication, is represented on RS485
serial connection by the following sequence:
-
7
1
1
0
1
1
7
0
1
1
1
1
7
1
1
1
1
1
-
Out of range condition, corresponding to "HHHH" or "LLLL" display indication, is represented on RS485
serial connection by the following sequence:
7
-
1
1
0
0
0
7
0
1
0
0
0
7
0
0
0
0
0
The RS485 serial interface allows also the complete remote control of the sensor.
All the commands have to be sent via terminal in an ASCII format according to the following:
Phone: 800.894.0412 - Fax: 888.723.4773 - Web: www.clrwtr.com - Email: [email protected]
- Receipt of the channel status:
At any moment, at the receipt of the 'r <CR> <LF>' remote command (and SYNC passive), the
sensor configuration is restored.
- Remote configuration:
The commands available are:
@ <CR> <LF>
beginning of the remote setting mode (and SYNC passive)
c1 <CR> <LF>
channel 1 selection
distance selection, with xxxx {0...4095}
vxxxx <CR> <LF>
dark/light mode selection, with x {1, 2}
bx <CR> <LF>
e <CR> <LF>
memorisation of the configuration sequence.
q <CR> <LF>
exit from remote setting without saving the configuration.
At the receipt of the q <CR> <LF> or e <CR> <LF> commands, the sensor visualises ok <CR>
<LF>.
- Delay configuration:
The commands available are:
@ <CR> <LF>
beginning of the delay configuration (and SYNC passive)
delay selection, with x {0, 1, 2, 3, 4, 5}
dx <CR> <LF>
d0 = 0 ms
d1 = 5 ms
d2 = 10 ms
e <CR> <LF>
memorisation of the new delay value
q <CR> <LF>
exit from the delay configuration without saving the configuration.
At the receipt of the q <CR> <LF> or e <CR> <LF> commands, the sensor visualises ok <CR>
<LF>.
NOTE: the single digits have to be distanced amongst themselves at least 1 ms, during the
command transmission.
DETECTION DIAGRAMS
0
D13
D12
1
0
D8
D7
1
0
D1
D0
0
0
1
1
1
0
1
1
1
0
1
1
0
0
0
0
1
0
0
0
1
0
0
0
0
All the safety electrical and mechanical regulations and laws have to be respected during sensor
functioning. The sensor has to be protected against mechanical damages.
Place the given labels in a visible position close to the laser emission.
b1 = Dark
b2 = Light
Do not look directly into the laser beam!
Do not point the laser beam towards people!
Eye irradiation for over 0.25 seconds is dangerous; refer to class 2 standard (EN60825-1).
These sensors are not conform to safety applications!
This product is intended for indoor use only.
d3 = 20 ms
d4 = 30 ms
d5 = 40 ms
The sensors are NOT safety devices, and so MUST NOT be used in the safety control of
DECLARATION OF CONFORMITY
We Datalogic Automation declare under our sole responsibility that these products are conform to the
2004/108/CE and successive amendments.
WARRANTY
Datalogic Automation warrants its products to be free from defects.
Datalogic Automation will repair or replace, free of charge, any product found to be defective during the
warranty period of 36 months from the manufacturing date.
This warranty does not cover damage or liability deriving from the improper application of Datalogic
Automation products.
DATALOGIC AUTOMATION cares for the environment: 100% recycled paper.
DATALOGIC AUTOMATION reserves the right to make modifications and improvements without prior notification.
© 2008 – 2014 Datalogic Automation - ALL RIGHTS RESERVED - Protected to the fullest extent under U.S. and
international laws. • Copying, or altering of this document is prohibited without express written consent from Datalogic
Automation. Datalogic and the Datalogic logo are registered trademarks of Datalogic S.p.A. in many countries, including the
U.S.A. and the E.U.
SAFETY WARNINGS
the machines where installed.
826003035 Rev.F