BENDIX BA-921 COMPRESSOR-STD-CLOSED ROOM Service Data - Page 8
Browse online or download pdf Service Data for Air Compressor BENDIX BA-921 COMPRESSOR-STD-CLOSED ROOM. BENDIX BA-921 COMPRESSOR-STD-CLOSED ROOM 17 pages. Air power compressor
Also for BENDIX BA-921 COMPRESSOR-STD-CLOSED ROOM: Installation Instructions (4 pages)
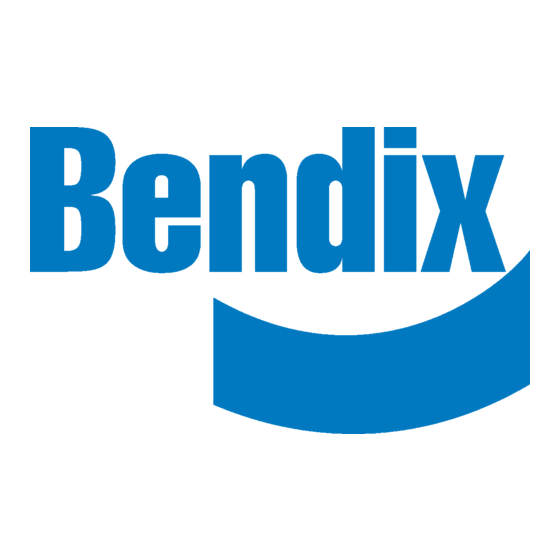
BACK / RETOUR
4. Remove the balance piston (4) and its spring (5) from
the cylinder head.
5. Remove the four hex head bolts and washers from the
cylinder head.
6. Gently tap the head and valve plate assembly with a
soft mallet to break the gasket seal. Lift the cylinder
head and valve plate assembly (12) off the cylinder
block.
7. Remove the metal reed valve/gasket (13).
8. Gently tap the head and valve plate assembly (12) with
a soft mallet to break the gasket seal. Then separate
the cylinder head from the valve plate assembly (12)
and remove the gasket (11).
9. Turn the aluminum cylinder head over to expose the in-
terior portion of the head. Push the unloader piston (8)
along with its o-rings (6, 7 & 9) out of the cylinder head.
CRANKCASE COVER
1. Remove the four crankcase cover cap screws securing
the crankcase cover to the crankcase. Using a soft mal-
let, gently tap the crankcase cover to break the gasket
seal. Remove the crankcase cover gasket (15).
REAR END COVER OR END COVER ADAPTER
1. Remove the four end cover cap screws that secure the
rear end cover or end cover adapter to the crankcase.
2. Remove the rear end cover or end cover adapter from
the crankcase. Remove the o-ring seal (14) from the
end cover.
CLEANING OF PARTS
GENERAL
All parts should be cleaned in a good commercial grade of
solvent and dried prior to inspection.
CYLINDER HEAD
1. Carefully remove all gasket material adhering to the
aluminum cylinder head, steel valve plate assembly and
cast iron cylinder block. Make certain not to deeply
scratch or mar the gasket surfaces. Pay particular at-
tention to the gasket surfaces of the aluminum head.
2. Remove carbon deposits from the discharge and inlet
cavities of the cylinder head and valve plate assembly.
They must be open and clear in both assemblies. Make
certain not to damage the aluminum head.
3. Remove rust and scale from the cooling cavities and
passages in the head and valve plate assembly (12)
and use shop air to clear debris from the passages.
4. Check the threads in all cylinder head ports for galling.
Minor chasing is permitted.
8
5. Make certain the unloader vent passage under the un-
loader cover (2) in the head is open and free of debris.
INSPECTION OF PARTS
CYLINDER HEAD & VALVE PLATE
1. Carefully inspect the cylinder head gasket surfaces for
deep gouges and nicks. If detected, the compressor
must be replaced.
2. Carefully inspect the valve plate assembly gasket sur-
faces for deep gouges and nicks. Pay particular attention
to the metal gasket surface. A metal gasket (18) is used
between the valve plate assembly and cylinder block.
This surface must be smooth and free of all but the most
minor scratching. If excessive marring or gouging is de-
tected, the compressor must be replaced.
3. Inspect the cylinder head for cracks or damage. With the
cylinder head and head gasket secured to the valve plate
assembly, apply shop air pressure to one of the coolant ports
with all others plugged, and check for leakage by applying a
soap solution to the exterior of the head. If leakage is de-
tected in the cylinder head casting, replace the compressor.
END COVER OR END COVER ADAPTER
Check for cracks and external damage. Check the crankshaft
main bearing surface in the end cover or end cover adapter,
check for excessive wear and flat spots and replace the end
cover if necessary. Check for galling of the oil port threads
and replace the end cover or end cover adapter if necessary.
Minor thread chasing is permitted but do not "recut" the
threads if they are badly damaged.
CYLINDER BLOCK
1. Check the cylinder head gasket surface on the cylinder
block for nicks, gouges, and marring. A metal gasket is
used to seal the cylinder head to the cylinder block.
This surface must be smooth and free of all but the
most minor scratching. If excessive marring or goug-
ing is detected, the compressor must be replaced.
ASSEMBLY
General Note: All torques specified in this manual are as-
sembly torques and typically can be expected to fall off
after assembly is accomplished. Do not re-torque after
initial assembly torques fall unless instructed otherwise. A
compiled listing of torque specifications is presented at the
end of this manual.
INCH POUNDS TO FOOT POUNDS
To convert inch pounds to foot pounds of torque, divide
inch pounds by 12.
12 Inch Pounds = 1 Foot Pound
Example:
12
FOOT POUNDS TO INCH POUNDS