Miller ANALOG 300 Owner's Manual - Page 5
Browse online or download pdf Owner's Manual for Welding System Miller ANALOG 300. Miller ANALOG 300 34 pages.
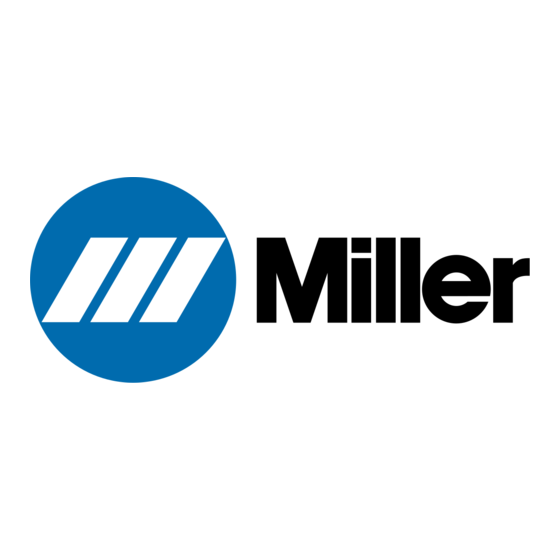
SECTION
1-SAFETY RULES FOR
OPERATION
OF ARC WELDING
POWER SOURCE
1-1.
INTRODUCTION
We
learn
by experience. Learning safety through personal
experience
like achild
touching
ahot
stove
is
harmful,
waste
ful,
and unwise. Let the
experience
of others teach
you.
Safe
practices developed
from
experience
in the
use
of weld
ing
and
cutting
are
described in this manual.
Research,
devel
opment, and field
experience
have
evolved
reliable
equipment
and safe
installation, operation,
and
servicing
practices.
Acci
dents
occur
when
equipment
is
improperly
used
or
main
tained. The
reason
for the safe
practices
may
not
always
be
given.
Some
are
based
on
common
sense,
others may
require
technical volumes
to
explain.
It is wiser
to
follow the rules.
Read and understand these safe
practices
before
attempting
to
install,
operate,
or
service the
equipment. Comply
with
these
procedures
as
applicable
to
the
particular equipment
used and their instruction
manuals,
for
personal
safety
and
for the
safety
of others.
Failure
to
observe these safe
practices
may
cause
serious in
jury
or
death. When
safety
becomes
a
habit,
the
equipment
can
be used with confidence.
Responsibilities
of
installer,
user,
and
serviceman.
Installa
tion, operation,
checking,
and
repair
of this
equipment
must
be done
only by
a
competent person,
experienced
with such
equipment.
These
safe
practices
are
divided
into
two
Sections:
1
-
General
Precautions,
common
to
arc
welding
and
cutting;
and
2- Arc
Welding
(and
Cutting)(only).
Reference standards: Published Standards
on
safety
are
also
available for additional and
more
complete procedures
than
those
given
in
this manual.
They
are
listed in the Standards
Index in these
safety
rules. ANSI Z49.1 is the
most
complete.
The
National Electrical
Code,
Occupation Safety
and Health
Administration,
local
industrial
codes,
and local
inspection
requirements
also
provide
a
basis for
equipment
installation,
use,
and service.
1-2.
GENERAL PRECAUTIONS
A.
Burn Prevention
Wear
protective
clothing
-
leather
(or asbestos)
gauntlet
gloves, hat,
and
high safety-toe
shoes. Button shirt collar
and
pocket flaps,
and
wear
cuffless
trousers
to
avoid entry of
sparks
and
slag.
Wear helmet with
safety goggles
or
glasses
with side shields
underneath, appropriate
filter lenses
or
plates (protected
by
clear
cover
glass).
This is
a
MUST for
welding
or
cutting, (and
chipping)
to
protect the
eyes from radiant energy
and
flying
metal.
Replace
cover
glass
when
broken, pitted,
or
spattered.
See 1-3A.
Avoid
oily
or
greasy
clothing.
A
spark
may
ignite
them.
Hot metal
such
as
electrode
stubs and
workpieces
should
never
be handled without
gloves.
Medical first aid and
eye
treatment.
First aid
facilities and
a
qualified
first aid person should be available for each shift
unless medical
facilities
are
close
by
for immediate
treatment
of flash burns of
the eyes
and skin burns.
Ear
plugs
should be
worn
when
working
on
overhead
or
in
a
confined space. A hard
hat should
be
worn
when others work
overhead.
Flammable hair
preparations
should
not
be used
by
persons
intending
to
weld
or
cut.
B.
Toxic Fume
Prevention
Adequate
ventilation. Severe
discomfort,
illness
or
death
can
result
from
fumes,
vapors,
heat,
or
oxygen enrichment
or
depletion
that
welding
(or
cutting)
may
produce.
Prevent
them with
adequate
ventilation
as
described
in
ANSI Stan
dard Z49.1
listed
1
in
Standards index. NEVER ventilate
with oxygen.
Lead, cadium, zinc,
mercury, and
beryllium bearing
and simi
lar
materials,
when welded
(or cut)
may
produce
harmful
concentrations
of
toxic fumes.
Adequate
local exhaust venti
lation
must
be
used,
or
each person in the
area
as
well
as
the
operator
must
wear an
air-supplied respirator.
For
beryllium,
both
must
be used.
Metals coated
with
or
containing
materials that emit toxic
fumes should
not
be heated unless
coating
is removed from
the work
surface,
the
area
is well
ventilated,
or
the operator
wears
an
air-supplied respirator.
Work
in
a
confined
space
only
while it is
being
ventilated
and,
if necessary, while
wearing
an
air-supplied respirator.
Gas leaks
in
a
confined space should be avoided. Leaked gas
in
large quantities
can
change
oxygen
concentration
danger
ously.
Do
not
bring
gas
cylinders
into
a
confined space.
Leaving
confined space, shut OFF gas
supply
at
source.
The
space will then be safe
to
re-enter, if downstream valves have
been
accidently opened
or
left
open.
Vapors
from chlorinated solvents
can
be
decomposed by
the
heat of the
arc
(or flame)
to
form
PHOSGENE,
a
highly
toxic
gas,
and other
lung
and eye
irritating
products.
The ultra
violet
(radiant)
energy
of
the
arc
can
also
decompose
tn
chloroethylene
and
perchloroethylene
vapors
to
form
phos
gene.
DO NOT
WELD
or
cut
where solvent vapors
can
be
drawn into the
welding
or
cutting
atmosphere
or
where the
radiant energy
can
penetrate
to
atmospheres containing
even
minute
amounts
of
trichlorethylene
or
perchlorethylene.
C.
Fire and
Explosion
Prevention
Causes of
fire and
explosion
are:
combustibles reached
by
the
arc,
flame, flying sparks,
hot
slag
or
heated
material;
misuse
of
compressed
gases and
cylinders;
and short circuits.
Be
aware
that
flying
sparks
or
falling slag
can
pass
through
cracks, along
pipes, through
windows
or
doors,
and
through
wall
or
floor
openings,
out
of
sight
of the
goggled
operator.
Sparks
and
slag
can
fly
35 feet.
To prevent fires and
explosion:
Keep
equipment
clean
and
operable,
free of
oil,
grease, and
(in electrical
parts)
of metallic
particles
that
can
cause
short
circuits.
If combustibles
are
in area, do
NOT weld
or
cut.
Move the
work if
practicable,
to
an
area
free of combustibles. Avoid
paint
spray rooms,
dip tanks,
storage areas, ventilators. If the
work
can
not
be
moved,
move
combustibles
at
least 35 feet
away
out
of reach
of
sparks
and heat;
or
protect
against
ignition
with suitable and
snug-fitting,
fire-resistant
covers
or
shields.
Walls
touching
combustibles
on
opposite
sides should
not
be
welded
on
(or cut).
Walls,
ceilings,
and
floor
near
work
should be
protected
by
heat-resistant
covers or
shields.
Fire
watcher
must
be
standing by
with
suitable
fire
ex
tinguishing equipment during
and for
some
time after weld
ing
or
cutting
if:
a.
appreciable
combustibles
(including building
construc
tion)
are
within
35
feet
b.
appreciable
combustibles
are
further than
35
feet but
can
be
ignited
by sparks
c.
openings
(concealed
or
visible)
in floors
or
walls within 35
feet may expose combustibles
to
sparks
d.
combustibles
adjacent
to
walls,
ceilings,
roofs,
or
metal
partitions
can
be
ignited by
radiant
or
conducted heat.
Hot work
permit
should
be
obtained before
operation
to
ensure
supervisors
approval
that
adequate precautions
have
been
taken.
After work is
done,
check that
area
is free of
sparks, glowing
embers,
and flames.
An empty container that held
combustibles,
or
that
can
pro
duce flammable
or
toxic vapors
when
heated,
must
never
be
welded
on
or
cut, unless container has first been cleaned
as
described
in
AWS
Standard AGO,
listed 3
in
Standards
index.
OM-21 5
Page
1