FIBARO ROLLER SHUTTER 2 Operating Manual - Page 2
Browse online or download pdf Operating Manual for Controller FIBARO ROLLER SHUTTER 2. FIBARO ROLLER SHUTTER 2 2 pages. Universal, 2-wave compatible, electric
motor controller
Also for FIBARO ROLLER SHUTTER 2: Operating Manual (2 pages)
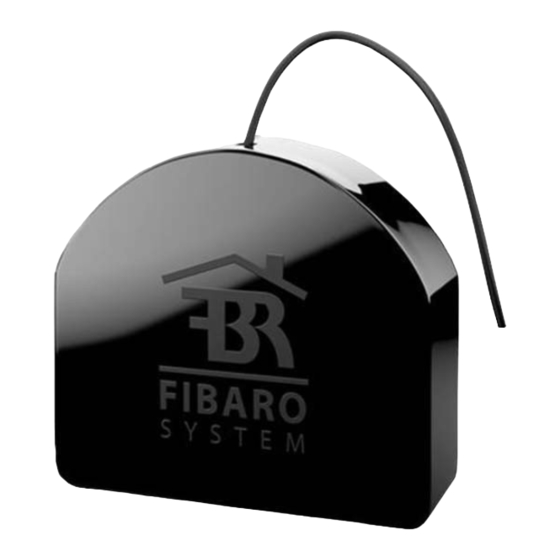
Fibaro
Roller
Shutter provides
three
association groups:
1
association group is triggered
through
a momentary swltch
click,
or a toggle switch position change.
II
association group is triggered through a momentary switch hold
NOTE
II
association group is inactive when toggle
switches
are used or in Gate Controller mode (parameter 10).
In case of controlling Venetian
Blinds, control
commands are
sent
in Fibar Command
Class
standard.
III association group reports the module
status.
Only one device
may be assigned to this group, main controller by default. Jt's not
recommended to modify this group's
settings.
Fibaro Roller Shutter allows for commanding other Roller
Shutters,
associated into
I
or ll assoclation
group,
through clicking or holding a
switch key. For example, this mechanism atlows for operating a
Roller Shutter connected to
the
switch with a button
click,
and
operating the devices associated in
II
association group by a button
hold.
In
addition, when operating Venetian
Blinds,
it's possible to
synchronize many
devices.
USING
ASSOCIATIONS
TO OPERATE
ANOTHER
ROLLER
SHUTTER
OR ANY
OTHER
Z-WAVE
DEVICE.
1 ASSOCIATION GROUP:
Clicklng
Ä
button,
connected to S1 terminal will inltiate up
movement in associated Roller Shutters, or send
Turn
On command
frame to the devices associated in l-st association group.
Clicking
... button,
connected to S2 terminal will initiate down
movement in associated Roller Shutters, or send
Turn
Off command
frame to the devices associated in 1-st associatlon group.
II
ASSOCIATION GROUP:
Holding
Ä
button,
connected to S1 terminal will move the
connected roller blind up, and after 1 second delay initiale up
movement in associated Roller
Shutters,
or send
Turn
On command
frame to the devices associated in 11-nd association
group.
Holding
...
button,
connected to S2 terminal will move the
conected rolled blind
down,
and after 1 second delay initiale down
movement in asSociated Roller Shutters, or send Turn Off command
frame to the devices associated in
11-nd
association
group.
USING ASSOCIATIONS
TO
OPERATE
ROLLER
SHUTTERS CONNECTED
TO VENETIAN
BUNDS.
Using association mechanism to operating venetian blinds require&
configuring
both,
l-st and 11-nd association groups.
1
ASSOCIATION
GROUP
Clicking
A
button,
connected to S1 terminal will initiate up
movement of the connected venetian blind and other
device~
associated in 1-st association group.
Clicking
...
button,
connected to S2
terminal
will initiate
down
movement of the connected venetian blind and other
devices
associated in 1-st association
group.
II ASSOCIATION
GROUP
(relevant for momentary switches only)
Holding
A
button,
connected to S1
terminal
will initiate
slats
rotation up, of the connected venetian blind as well as the other
devices associated in 11-nd association group.
Holding
...
button,
connected to S2 terminal will initiate
slats
rotation down, of the connected venetian blind as well as
the
other
devices associated in
ll-nd
association group.
&
NOTE
Once the assoclated devices are already
moving,
they will be stopped if any of the buttons is pressed
and held
XIII.
OPERATING GATE MOTORS
Fibaro
Roller Shutter allows for operating gate
motors.
Gate motor
should be connected to 01 and 02 terminaJs according to
Fig.2.
In
the
Gate
Mode,
a momentary switch may be connected to S1
terminal.
lt's recommended
to
connect an
IR
barrier, an emergency
stop button or any alarm mechanism to S2 terminal. Opening a
contact in a
device
connected to S2 terminal will always result in
stopping a motor
in
current position (see Fig. 2).
Clicking a push button connected to S1 terminal will initiate opening
the gate. Next click of a button will stop the
gate.
Yet another cllck of
a button will close
the
gate.
According to following
seaquence;
OPEN
-
STOP
-
GLOSE
-
STOP
-
OPEN.
G;ite
' < .
X
D
DD
-
0
ow
10kWh
Fig.
5
Roller Shutter
icon In Horne
Center interface
&
NOTE
In Gate
Mode,
by
default,
the S1 terminal is set to
operate w1th a momentary switch, ignoring the
parameter
14 settings
Full opening the gate
initiales
a Roller Shutter
COUNTDOWN.
After
the
COUNTDOWN the gate will start
closing.
COUNTDOWN length
is set through the parameter
12.
In addition, if th
e
IR barrier is cut (S2
contact
opened) at the gate fully open, the gate will start closing after
a time period specified in parameter
17.
NOTE
In
both
Gate Modes,
with and without positioning,
parameters 12 and 17 are automatically set to 0. At
these settings the gate will open, but will
not
automatical!y close
.
Relevant times need to be set
manually in parameters 12 and 17 (see section
XVIII)
.
NOTE
Parameters 12 and 17 settings are automatically
modified only in Horne Center 2 controller, when
choosing one of Gate Modes. ln case of controllers
from other manufacturers·these
parameters need
to
be set manuaHy (see section XVIII)
.
NOTE
Installation
of the gate
driver
may be performed only
by certified professionals. The motor must be
equipped with the appropriate limit switches (see
Fig
2).
lt's recommended to connect a NC (normally
closed) contact of an IR barrier to S2 terminal.
Opening the contact will stop the gate.
In
addition,
it's recommened to connect an emergency stop
button to the motors
neutral
(N)
wire.
In
emergency,
pushing the emergency stop button will cut the
power and stop the gate. lt ls recomended to monitor
regulary operation of
Fibaro
Roller shutter in all
modes. Also it is recomended to regulary verificate
and maintenance connectors.
NOTE
S1 and S2 terminals react
to
mains voltage
only.
Using IR barriers with NC contacts operating an
lower voltages require
using
an additional
relay
(see
Fig. 2)
XIV.
LED INDICATOR
Fibaro
Roller Shutter has a MENU. Each MENU level is signaled
through a LED
lndicator
colour.
Ta enter MENU press and hold the
B-button for at least 2 seconds.
While the B-button is being
held,
LED
lndicator
colours will change
in the following sequence:
BLUE
- Roller Shutter calibration procedure (see section IX)
VIOLET - initiale the Z-Wave network range tester
GREEN -
reset energy consumption data memory (see section XVI)
YELLOW
- Roller Shutter reset (see section VIII)
Release the B-button to choose the desired function and confirm
your choice with the B-button
click.
XV.
Z-WAVE RANGE TESTER
Fibaro
Roller Shutter has a built in mechanism, allowing to roughly
estimate the Z-Wave network range
.
CAUTION
To allow for the Z-Wave network range
test,
the
Z-Wave network controller needs to support the
functionality and
the
module needs to be included
in the network. Z-Wave range test puts heavy strain
on the network, so it's recommended to use the
function only in special cases.
In order to test the Z-Wave network
range:
1)
Press and hold the 8-button for ca. 6 seconds, until the
LED
lndicator
glows violet.
2)
Release the B-button.
3)
Click the
B-button.
4)
LED lndicator
will signal
the Z-Wave
network range (see
description
below).
5)
Click the B-button
to
exit the Range Tester.
Network range signaling
modes:
Z-Wave network range
is
signaled by
LED
illumination colour and
behaviour.
Blinking each 1-second means the
modules
tries to
establish a direct communication with the main controller, while 2
seconds glowing means
the
test
result.
The test is pelionned in a
loop, until being stopped by the
user.
Z-Wave range test is
peliormed in three steps, signaled with green,
yellow,
violet and
red:
1) Blinking in GREEN means the modute tries to establish a direct
communication with the main
controller.
Positive test result is
signaled by a 2 second glowing in
GREEN,
after which the test
is
repeated (step 1 ). In
practice,
if the module is able
to
establish a
dlrect communication with the main contro!ler, the
LED
will glow
GREEN,
without blinking.
2) lf
the module
is
not able to establish a direct connection with the
main controller, it will try to establish a routed connection, through
another, intermediary, Z-Wave network devices. LED indicator will
change the illumination colour to RED.
Positive
test
result is
signa!ed with glowing in YELLOW. After 2 seconds the module will
retry
establishing a direct communication (step 1 ).
[I]
NOTE
The
module may mod1fy the main controller
commumcat1
on from direct to routed and vice
versa
,
espec1alty 1f 1t's
located
at the direct
commun1cat1
on
range
hmit
3) lf the module is not able to establish a routed connection with
the
main controller, LED lndicator colour will change
from
YELLOW to
VIOLET. After few seconds test will end and
the LED lndicator
will
glow RED for two seconds. Whole procedure will start again and
the module will try to establish a direct connection with the main
controller (step
1
).
XVI.
CURRENT A ND HISTORICA
L
POWER
CONSUMPTl0
N
MEASURING
Fibaro Roller Shutter allows for the current load and
power
consumption
monitoring.
Data is sent to
the
main controller, e.g.
Horne Center 2.
Measuring is carried out by an independent microprocessor
dedicated exclusively for the
purpose,
assuring
maximum
accuracy
and
precision.
The
microprocessor
is
factory calibrated.
Electric power-
power consumed by an electric device in an
instant,
in Watts
f;N)
.
ElectriC energy - energy consumed
by
a
device
through a time
period. Most commonly measured in kllowatt-hours (kWh). One
kilowatt-hour
is
equal to one kilowatt of power consumed over a
period ofone hour,
1kWh
•
1000
Wh
.
·
RESETTING ELECTRICITY CONSUMPTION
MEMORY
Fibaro Roller Shutters electricity consumption memory may be
cleared in one of the following ways:
1)
Through
the module reset (see section VIII)
2) Through the
main controller menu (see main controllers
operating manual
3)
Manually
using
the following instructions:
a)
Make sure the device is connected to voltage supply.
b)
Press and hold the B-button for
ca.
10
seconds,
until
LED
1
ndicator glows
GREEN.
c)
Release the
B-button.
d)
Click the 8-button.
e) Energy consumption memory
has
been
erased.
NOTE
1)
Please contact your local supplier for the current
rat es
2)
Fibaro Roller
Shutter stores consume.d electricity
data on its memory, which
means
disconnecting the
modu1e from voltage supply does not erase the
data.
XVII.
PROTECTION
MODE
Fibaro
Roller Shutter
uses
the
Protection
Command Class v2 to
prevent from unintended motor movement.
1)
Local
Protection
Local
Protection
State:
n·:.
rio
protectiori.
ROiier Shutter 'responds t'o pUsh büttons.
1
-
not supported
2
- Local
protection active. Roller Shutter does not respond to
push buttons.
Once the
Local
Protection is activated, the module stops
responding
to S1 and S2 push buttons. SCENE 10 and association
commands will not be sent as weil. The
only
exception is the
B-button. Menu and
Z~Wave network
inclusion, after the 8-button
or S1 push button triple
click,
are still active.
WARNING
In
Protection Mode it will not be possible to control
Fibaro Roller
Shutter
from
buttons.
lt is
not
recomended to control all
Fibaro
Roller Shutters in
this
mode.
CAUTION
There's one more exception in
Local
Protection.
In
Gate
Mode,
S2 (IR Barrier) is still
active.
lt means if
the obstacle is detected, the gate will stop,
regardless
the Local Protection State set.
2) RF Protection (radio
protection)
RF Protectlon
State:
0 - No protection. Roller Shutter
responds
to
command
frames.
1 - RF
Protection
active. Roller Shutter does
not respond
to the
Z-Wave control frames.
2 - not supported.
Once the RF Protection is activated, the module stops responding
to command frames setting
the
blind position. lt's still possible
however to
configure
the
device
(advanced
configuration
parameters, protection
modes)
and checking it's current state
through polling (position, power. energy).
~VIII.
ADVA.NCED CONFIGURATION
GENERAL SETTINGS:
3.
Reports type
0
-
Blindposition
reports sent to the maln controller using Z-Wave
Command Class.
1 -
Blind
position reports sent
to
the main controller
using Fibar
Command Class.
Parameters value shoud be set to 1 if
the
module operates in
Venetian
Blind mode.
Default setting:
O
Parameter
size:
1
[byte]
NOTE
&
To make sure whether
Fibar
Command Class is
supported by Z~Wave network main controllers
from other
manufacturers,
please contact the
controllers manufacturer.
10.
Roller Shutter operating modes:
0
~
Roller Blind
Mode,
without positioning
1 -
Roller Blind Mode, with positioning
2
-
Venetian Blind
Mode,
with positioning
3 - Gate Mode, without positioning
4
-
Gate Mode, with positioning
Default settng
:
1
Parameter size:
1 [byte]
12.
In Venetian Blindmode (parameter
10 s·et
to
2)
the parameter
determines
time
of full
turn
of the
slats.
In
Gate Mode (parameter
10
set to 3 or 4) the parameter defines the
COUNTDOWN time, i.e. the time period after whi'ch an open gate
starts closing.
In
any other operating mode
the parameter
value is
irrelevant
.
Value of O means the gate will not close
automatically.
Available settings:
0-65535
(0
-
655,35s)
Default setting: 150 (1,5 s)
Parameter size:
2 [bytes]
13.
Set slats back
to
previous positlon.
In Venetian Blind Mode (parameter 10 set to 2) the parameter
influences slats positioning in various situations.
In
any other
operating mode the parameter value is irrelevant.
0 - Slats
return
to previously set position only in case of the
main controller
operation.
1
- Slats
return
to previously set position
in
case of the main
controller
operation,
momentary switch
operation,
or when the
limit switch is
reached.
2 - Slats retum to previously set position
in
case of
the
main
controller operation, momentary switch operation, when the limit
switch is reached or after receiving a
"STOP"
control frame
(Switch
Multilevel Stop).
Default setting: 1
Parameter
size: 1
[byte]
14.
Switch
type.
The parameter settings are
relevant
for Roller Blind Mode and
Venetian
Blind
Mode (parameter 10 set to 0, 1,
2).
0
~
Momentary switches
1
-
Toggle
switches
2
-
Single, momentary
switch.
(The switch should be connected to
S1 terminal)
Default
setting:
D
Parameter
size:
1 [byte]
17.
In
Roller Blind
Mode or
Venetian Blind mode (parameter
10
set
to 0,
1,
2)
the
parameter determines
when
the Roller Shutter
relays
are
turned
off after
reaching a
limit switch.
In
Gate Mode (parameter 10 set to 3 or 4) the parameter determines
a time period after which a gate will start closing after a S2 contact
has been disconnected. In this mode, time
to turn
off the Roller
Shutter
relays
after
reaching
a
limit
switch is set
to
3 seconds and
cannot be
modified.
Value of O means the gate will note close
automatically.
Available Settings:
0
• 255 (0,1-25,5s).
Default setting:
10
(1s).
Parameter
size:
1 [byte]
18.
Motoroperation
detection.
Power threshold
to
be interpreted as reaching a
limit
switch.
Available settings:
O
•
255
(1-255 W)
The
value of O
means
reachlng a limit switch will not be detected
Default setting: 10 (10W).
Parameter size:
1 [byte]
22.
Motoroperation time.
Time
perlod
for the motor to continue
operation.
Available settings:
O -
65535
(0- 65535s)
The
value of O
means
the function is
disabled.
Default setting: 240 (240s.
-4
minutes)
Parameter
size:
2
[bytes]
29. Forced Roller
Shutter callbration.
By modifying the parameters setting from O to 1 a Roller Shutter
enters the calibration
mode.
The parameter relevant only if a Roller
Shutter is set to work in positioning mode {parameter 10 set
to
1,
2
or4).
1 - Start calibration process
Default
setting:
0
Parameter
size:
1 [byte]
ALARM
SETTINGS:
30.
Response to general
alarm
O
- No reaction.
1 - Open blind.
2 - Glose
blind.
Default setting:
2
Parameter size:
1 [byte]
31. Response to flooding
alarm
0
- No
reaction.
1 - Open blind.
2 - Glose
blind.
Default
setting:
0
Parameter size:
1 [byte)
32.
Response to
smoke,
CO or C02 alarm
0
- No
reaction.
1 -
Open blind.
2
- Glose
blind.
Default setting: 1
Parameter size: 1
[byte]
33.
Response
to temperature alarm
0
- No reaction
.
1
- Open blind.
2 - Glose
blind.
Default
setting:
1
Parameter
size:
1 [byte]
35. Managing
slats in response
to
alarm.
In Venetian Blind Mode (parameter 10 set to
2),
the parameter
determines how the slats will react upon alarrn detection.
In
any
other
modes,
the parameter value is not relevant.
0
-
Da
not change slats position - slats
return
to the last set
position.
1 - Set slats to their extreme position.
Default
setting:
1
Parameter
size:
1
[byte]
POWER AND ENERGY REPORTS SETTINGS:
40.
Power reports.
Power level change that will result in new power value
report
being
sent. The parameter defines a change that needs to occur in order to
trigger the
report.
The
value is a percentage of the previous
report.
Power report threshold available settings: 1-100
(1-100%).
Value of O means the
reports
are turned
off.
Oefault
setting: 10 (10%).
Parameter size:
1 [byte]
42. Periodic power or energy reports.
The
parameter defines a
time
period between consecutive reports.
Available settings:
1-65534
(1-65534 seconds)
Value of
O
means the reports are turned
off.
Default
setting: 3600 (3600 seconds / 60
minutes).
Parameter size:
2 [bytes]
43.
Energy
reports.
Energy
level change which will result in
new
energy value report
being sent.
The
parameter defines a change that needs to occur ln
order to trigger the report
Energy
threshold available settings: 1-254 (0,01 -2,54kWh).
Value of
O
means the reports are tumed off.
Default setting
10
(0,1kWh).
Parameter size: 1
[byte]
44.
Self.measureme~t.
A Roller Shutter may include power and energy used by itself in
reports sent to the main
controller.
0 -
Self-measurement
inactive.
1 - Self-measurement active.
Default
setting:
O
Parameter size: 1
[byte]
SCENES
AND ASSOCIATIONS
SETTINGS:
50. Scenes
I
Associatlons
activation.
Par~me!er determines whether scenes or associations are activated
by the switch
keys.
0
- Associations activation
1
-
Scenes activation
Default setting:
O
Parameter size:
1 [byte]
XIX.
GUARANTEE
1.
The
Guarantee is provided by
FIBAR
GROUP S.A. (hereinafter
"Manufacturer"), based in
Poznan,
ul.
Lotnicza
1; 60-421
Poznan,
entered in the register cf the National Court Register kept by the
District Court in Poznari, VIII Economic Department ofthe National
Court
Register,
no.
553265,
NIP
7811858097,
REGON
:
301595664.
2.
The Manufacturer is responsible for equipment malfunction
resulting from
physical
defects (manufacturing or material) cf
the
Device for 12 months from the date of its
purchasing.
3.
During the Guarantee period, the Manufacturer shall remove
any
defects,
free of
charge,
by repairing or
replacing
(at the sole
discretion of the Manufacturer) any defective components cf the
Device with new or
regenerated
components
that
are free of
defects. When the repair impossible, the Manufacturer reserves the
right to
replace the
device with a new or regenerated one, which
shall be free cf any defects and its
condition
shall not be worse than
the original device owned by the Customer.
4.
ln
special cases, when the device cannot
be replaced
with
the
device of the same type (e.g. the device is no langer available in the
commercial offer), the Manufacturer
may replace
it with a different
device having technical parameters similar to the faulty one. Such
activity shall
be
considered as fulfilling the obligations of the
Manufacturer.
The
Manufacturer shall not refund money
paid
for
the
device.
5. The holder of a valid guarantee shall submit a guarantee claim
through the guarantee
service. Remember:
before you submit a
guarantee claim, contact our
technical
support using telephone or
e-mail. More than 50% of operational problems is resolved
remotely, saving time and money spent to initiating guarantee
procedure. lf
remote support is
insufficient,
the Customer shall fill
the
guarantee
claim form (using our website - www.fibaro.com) in
order to obtain claim authorization. When the guarantee claim form
is submitted correctly, the Customer shall receive the claim
confirmation
with
a
unique
number (Return
Merchandise
Authorization
-RMA).
6. The claim may be also submitted by telephone.
In
this case, the
call is
recorded
and the Customer shall be informed about it by a
consultant
before
submitting
the
claim
.
lmmediately
after
submitting the claim, the consultant shall provide the
Customer
with
the claim
number
(RMA-number).
7.
When the guarantee claim
fom,
is submitted correctly, a
representative of the Authorised Guarantee Service (hereinafter as
"AGS") shall contact the Customer.
8.
Defects
revealed
within the guarantee period shall be
removed
not
later
than 30 days from the date of delivering the
Device
to
AGS. The guarantee period shall be extended by the time
in
which
the Device was kept by AGS.
9.
The
faulty device shall be provided by the Customer with
complete
standard
equipment and
documents
proving
its
purchase.
10. Parts replaced under
the
guarantee are the property of the
Manufacturer.
The
guarantee for all parts replaced in the guarantee
proc.ess shall be equal to the guarantee period of the original
device. The guarantee period of the
replaced
part shall
not
be
extended.
11.
Costs of delivering the faulty device shall be borne by the
Customer.
For unjustified service calls,
the
Service may charge the
Customer with travel expenses and handling costs related to the
case.
12.
AGS shall not accept a complaint claim only when:
• the Device was misused or the manual was not
observed,
•
the
Device
was provided
by
the Customer
incomplete, without
accessories or nameplate,
•
it was
determined
that
the
fault was caused by other reasons than
a material or
manufacturing
defect of the
Device
•
the
guarantee document is not valid or there is no
proof
of
purchase,
13. The Manufacturer shall not be liable for damages to property
caused by defective
device.
The Manufacturer shall not be liable for
indirect, incidental, special,
consequential or punitive damages, or
for any
damages,
including, inter alia,
loss
of profits, savings, data,
lass of benefits, claims by
third
parties and any property
damage
or
personal injuries arising from or related to the
use
of the
Device.
14. The guarantee shall not cover:
• mechanical damages (cracks, fractures, cuts, abrasions,
physical
deformations caused by
impact,
falli[lg or dropping
the
device or
other object, improper
use
or not observing the operating manual);
• damages resulting frorn extemal
causes,
e.g.; flood
, storm,
fire,
lightning,
natural
disasters,
earthquakes,
war,
civil disturbance,
force majeure, unforeseen accidents, theft, water damage, liquid
leakage, battery spill, weather conditions,
sunlight,
sand, moisture,
high or low temperature, air pollution;
• damages caused by malfunctioning software, attack of a
computer virus
,
or by failure to
update
the software as recommen-
ded by
the
Manufacturer;
•
da mag es resulting from: surges in the power and/or telecommuni-
cation
network,
irnproper
connection to
the
grid in
~
manner
inconsistent with the operating manual, or from connecting other
devices not
recommended
by the Manufacturer.
•
damages caused by operating or storing the device in extremely
adverse conditions, i.e. high humidity, dust, too low (freezing) or
too
high ambient ternperature.
Detailed
permissible conditions for
operating the Device are defined in
the
operating manual;
•
damages
caused by using accessories not
recommended
by
the
Manufacturer
•
damages caused by faulty electrical installation of the Customer,
.
including the use of
incorrect
fuses;
•
damages
caused by Customer's failure to provide maintenance
and servicing activities defined in the operating manual;
• damages
resulting
from the use of spurious spare parts or
accessories
improper
for glven model, repairing and introducing
alterations by
unauthorized
persons;
•
defects caused by operating faulty Device er
accessories.
15. The scope cf the guarantee repalrs shall
not
include period ic
maintenance and
inspections,
in particular cleaning, adjustments,
operational checks
,
correction of errors or
parameter
programming
and other activities that should be performed by the user (Buyer).
The guarantee shall not cover natural wear and tear of the Device
and its components listed in the operating manual and in technical
documentation as such elements have a
defined
operational life.
16.
lf
a defect is not covered by the guarantee, the Manufacturer
reserves the
right
to remove such defect at its sole discretion,
repairing
the damaged or destroyed parts or provid ing components
necessary for repair or
replacement.
17.
This guarantee shall not exclude, limit or suspend the Customer
rights when the provided product is inconsistent with the
purchase
agreement.
CE:
This Device may be used with
all
devices
certified
with Z-Wave
certificate and
should
be
compatible
with such
devices produced by
other
manufacturers.
Any device compatible with 2-Wave may be added
to Fibaro system.
Hereby,
Fibar
Group S.A. declares
that
this Fibaro
Roller Shutter 2 is in compliance with the essential
requirements and other relevant provisions of
Directive
1999/5/EC.
FIBARGROUP
FIBARO
In case of any technical questions contact customer servlce centre
in your country.
www.fibaro.com