Ametek 081275 Service- en onderdelenhandboek - Pagina 7
Blader online of download pdf Service- en onderdelenhandboek voor {categorie_naam} Ametek 081275. Ametek 081275 13 pagina's. Direct drive regenerative blower
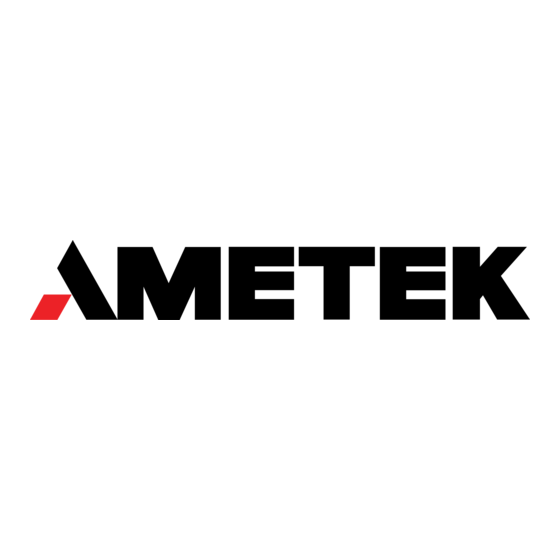
AMETEK Dynamic Fluid Solutions
100 East Erie St., Kent, Ohio 44240
Telephone: 330-673-3452 Fax: 330-677-3306
email: [email protected]
internet: www.ametekdfs.com
This AMETEK Rotron Explosion-proof Regenerative Blower may be equipped with Pilot Duty
Thermal Overload (PDTO) or Automatic Thermal Overload (ATO) protection. When properly
wired to a motor starter, this protection limits the motor winding temperature rise per the
National Electric Code (NEC) article 500. Failure to properly wire this blower is an NEC
violation and could cause an explosion. AMETEK Rotron assumes no responsibilities for
damages incurred by negligent use of this product, and will not warranty a blower on which the
PDTO is not properly connected. Some blowers 1 HP and under do not require PDTO and
have built in ATO. Consult the factory if verification of wiring connections is required.
In all cases, follow the motor controller manufacturer's instructions. The following schematic is
for conceptual understanding only, and may not apply to all motor/controller combinations.
The manufacturer's wiring diagram found on the motor takes precedent over reference
diagrams supplied by AMETEK Rotron Technical Motor Division.
Schematic
A1
Auxiliary
A2
Power
L1
L2
L3
J – Pilot Duty Thermal Overload Protection wires
L – Power leads from circuit breaker box
M – Motor leads (refer to wiring diagram inside T'box or on motor nameplate)
If you have any questions, contact AMETEK Rotron at 914-246-3401 for the location of your
area representative.
IMPORTANT: Read before wiring this Explosion-proof Blower
Push Start
Magnetic Coil
Contacts
Current
Overloads
.
EXPLOSION-PROOF BLOWERS
Push Stop
J
J
M1
Motor
M2
M3
The schematic is shown for a
three phase motor. For a
single phase motor disregard
L3 and M3. Pushing the
START button completes the
auxiliary control circuit,
allowing current to flow
through the magnetic coil.
The contacts are
magnetically closed, starting
the motor and latching the
auxiliary circuit. The motor
will continue to run until the
STOP push button is
depressed, the motor
reaches the overload
temperature, or the current
sensing overloads trip out.
6/1/16 Rev. F