GAC ESD5500E Series Handmatig - Pagina 3
Blader online of download pdf Handmatig voor {categorie_naam} GAC ESD5500E Series. GAC ESD5500E Series 9 pagina's. Speed control unit
Ook voor GAC ESD5500E Series: Handmatig (9 pagina's)
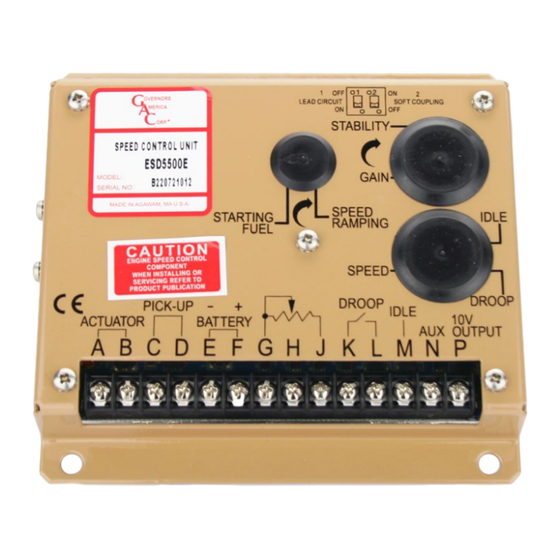
4
WIRINg (CONTINUED)
An overspeed shutdown device, independent of the governor system, must be provided to prevent loss of engine control which
may cause personal injury or equipment damage. Do not rely exclusively on the governor system to prevent overspeed. A
secondary shutoff device such as a fuel solenoid must be used.
When wiring eSD5500e Series controllers:
1.
use shielded cable for all external connections to the eSD controller.
2.
One end of each shield, including the speed sensor shield, should be grounded to a single point on the ESD case.
3.
Terminal A, B, E,and F should be 16 AWG or larger. Long cables require increased wire size to minimize voltage drops.
4.
Battery positive (+) Terminal F should be fused for 15 A.
5.
Magnetic speed sensors Terminals C and D must be twisted and or shielded for the entire length.
6.
The gap between the speed sensor and the ring gear teeth should be smaller than 0.02 in [0.5 mm] usually backing out 3/4 turn after
touching ring gear teeth. Speed sensor voltage should be at lease 1 V AC RMS during cranking.
7.
If auto synchronization is used alone, not with a load sharing module, use a 3 Ω resistor between Terminal N and P to match the voltage
between the speed control unit and the synchronizer.
8.
When operating at the upper end of the control unit frequency range, add a jumper wire between Terminal G and J to increase the fre-
quency range of the control unit over 7000 Hz.
9.
Terminal P is used to supply +10 V DC regulated supply to accessories. No more than 20 mA of current can be drawn from this supply.
Ground reference is Terminal G. A short circuit in this terminal can damage the speed control unit.
10. Do not over-tighten terminals. Torque to no greater than 9.0 in-lb ±2.5 [1.01 ±0.28 N∙m].
termInaL DefInItIon
A & B
Actuator (+/-)
Magnetic Speed Pickup
C & D
(D is ground)
E & F
Battery Power (-/+)
G
Ground Signal
H
For 12 V systems with actuator currents above 5 A, may sometimes require a jumper between Terminals H and G
J
Variable Speed
K & L
Droop Select
M
Idle Select
N
Accessory Input
P
Accessory Power Supply
aDDInG a PotentIometer
Use a single remote speed adjustment potentiometer to adjust engine
speed. Select the desired speed range and the corresponding potenti-
ometer value. If the exact range is not found select the next higher range
potentiometer. Connect the potentiometer as shown in the potentiometer
diagram.
noteS
16 AWG [1.3mm
] or larger wire
2
•
Wires must be twisted and/or shielded for their entire length
•
Gap between speed sensor and gear teeth should not be smaller than 0.02 in. (.51mm)
•
Speed sensor voltage needs to be at least 1 V RMS during crank
•
16 AWG [1.3mm
] or larger wire
2
•
A 15 A fuse must be installed in the Positive battery lead to protect against reverse voltage
•
Battery positive (+) input is Terminal F
5 kΩ resistive nominal.
Active when closed
Close for Idle
Load Sharing/Synchronizing, 0-10 V DC (5V Nominal, Reversed, 148 Hz/V). Shielded cabling recommended.
10 V DC Output To Power GAC Load Sharing and Synchronizing Modules
3
ESD5500E Series Speed Control Unit 2-2021-F2 PIB1002
Governors America Corp. © 2021 Copyright All Rights Reserved