Hi-Force ATDP125 Gebruiksaanwijzing - Pagina 10
Blader online of download pdf Gebruiksaanwijzing voor {categorie_naam} Hi-Force ATDP125. Hi-Force ATDP125 15 pagina's. Air driven hydrotest pumps
Ook voor Hi-Force ATDP125: Gebruiksaanwijzing (9 pagina's)
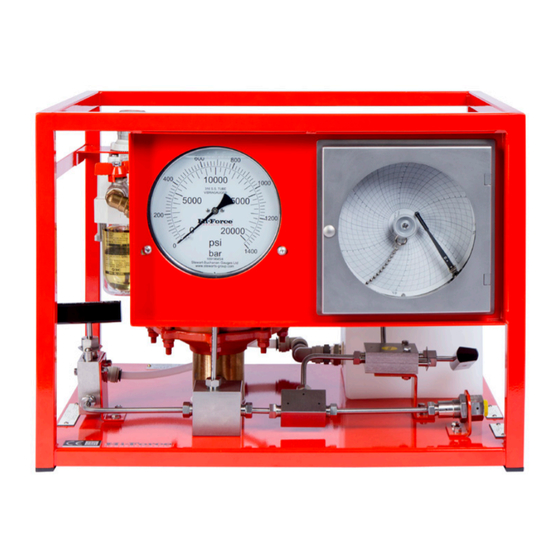
Operating Instruction Manual:
From Serial Number:
OM-ATDP-01
All
8.0 Installation / Setup
8.1 Before First Use / Preparation
It is recommended to use good quality clean & dry air (without moisture content) to drive the air driven pump
unit. As the air pressure drops at the pump exhaust ports, the air will cool and any water droplets in the air
can freeze prematurely due to temperature variation. For this reason we include and recommend the use
of 'Killfrost' at all times to be placed in the installed pump oil lubrication bottle. The lubricator bottle drop
feed rate is advised at 1 drop per 20 pump strokes. A COSHH sheet for 'Killfrost' is available on request.
If for any reason the lubricator is not used, the air motor should be disassembled, inspected and repacked
with suitable compound grease every 1 million strokes. Silicone type grease is prone to stiffening when not
in use, at a minimum the grease should be changed after a 6month idle period and every 12 months in a
scheduled routine service interval at a minimum.
Connect the hydraulic pressure outlet port to the equipment to be pressurised via a flexible hose assembly
or via a rigid pipe-work system. Ensure that all attached hose, pipe-work and fittings are rated suitably to
match, at a minimum, or exceed the maximum working pressure rating of the pump unit.
Direct the provided drain hose into a suitable container or drain.
Connect an air supply hose of at least ½" bore, to the power pack air inlet port. Use appropriately pressure
rated air hose and fittings for this purpose, these components must be rated at a higher working pressure
than the maximum supply air pressure that can be applied to the power pack. (1/2" bore air supply tubing
is the smallest size that will allow the pump to operate).
Ensure that the air on/off valve on the pump is in the closed before switching on the air supply. (Note: To
achieve the potential maximum working pressure and output flow capability, ensure an air supply of 7 bar
(100psi) is available with a flow rate of 212 SCFM (6m³/min). The use of a smaller bore air hose or a smaller
SCFM volume supply is acceptable but will diminish the maximum potential flow-rate from the pump.
Make connections to the fluid inlet port using suitably rated hose, pipe-work and fittings and a fluid isolation
valve. The fluid inlet hose and fittings bore is recommended to be not less than 1" bore.
Once the pump has raised hydraulic pressure DO NOT close the fluid inlet isolation valve.
Ensure the water supply is sufficient and only at 7 bar maximum pressure. It is advisable to ensure clean
water (fluid) is used as this prevents any possible chance of debris contaminating the pump check valves
(Y type strainer filter built in pump unit water line).
If fluid is being supplied from a tank ensure the tank is sited close to the fluid inlet port on the power pack
or sited above the level of the fluid inlet port (positive head/displacement pump).
Reducing the fluid supply inlet hose/pipe bore or supplying water from a tank at a lower level than the pump
inlet port may cause pump cavitation's and potential damage, so should always be avoided.
IMPORTANT:
Running the pump dry will result in damage.
10