Dynabrade 52226 Bediening, onderhoud en veiligheidsinstructies - Pagina 3
Blader online of download pdf Bediening, onderhoud en veiligheidsinstructies voor {categorie_naam} Dynabrade 52226. Dynabrade 52226 4 pagina's. .7hp/7/short shank/front exhaust die grinder
Ook voor Dynabrade 52226: Belangrijke bedienings-, onderhouds- en veiligheidsinstructies (4 pagina's)
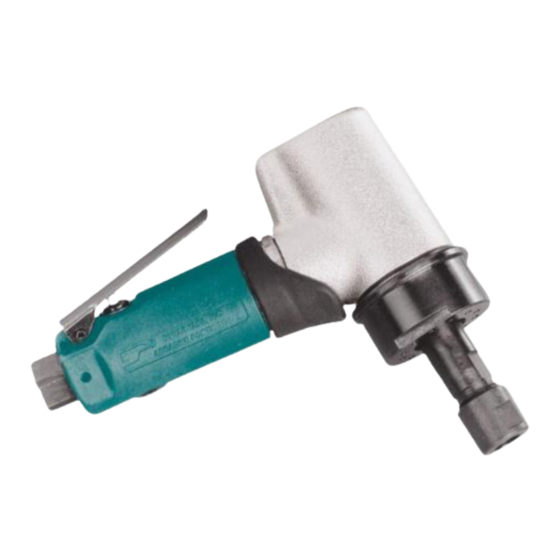
Disassembly/Assembly Instructions-.7 Hp Front Exhaust
Important: Manufacturer's warranty is void if tool is disassembled before warranty expires.
Notice: Dynabrade strongly recommends the use of their 52296 Repair Collar (sold separately) during assembly/disassembly activities. Failure to
use this collar will highly increase the risk of damage to the valve body of this tool. Please refer to parts breakdown for part identification.
Motor Disassembly:
1. Disconnect tool from power source.
2. Secure air tool in vise using 52296 Repair Collar.
3. With an open end wrench remove exhaust cover by turning counter-clockwise. Remove 01744 Silencer.
5. Remove collet assembly from rotor shaft by inserting a 3/16" hex wrench through collet assembly and into rotor shaft. Twist collet assembly from shaft.
6. Remove 01013 Cylinder, blades (4) and 01010 Spacer from rotor. Note: 01007 Bearing, 01008 Front Bearing Plate and spacer are a slip fit onto rotor.
7. Press rotor from 01743 Rear Bearing Plate. Press 02649 Bearing from bearing plate.
Motor disassembly is complete.
Valve Body Disassembly:
1. Position valve body in vise using 52296 Repair Collar with air inlet facing up.
2. Remove air fitting by securing 01494 Inlet Adapter with a wrench and twist air fitting from inlet adapter.
Important: 01494 Inlet Adapter must be secured before attempting to remove air fitting to avoid damaging valve body housing.
3. Using needle nose pliers, remove 01468 Spring, 01472 Tip Valve and seal.
4. Using a 2.5mm drift pin, tap 12132 Pin from housing and remove throttle lever.
5. Remove 95558 Retaining Ring using retaining ring pliers.
6. Push 01469 Regulator from valve body housing and remove O-rings.
Disassembly complete.
Motor Reassembly:
Important: Be sure parts are clean and in good repair before reassembly.
1. Place rotor in padded vise with a threaded spindle facing upwards.
2. Slip 01010 Spacer onto rotor.
3. Place a .002" shim into front bearing plate as an initial spacing and slip bearing into plate. Note: 01121 Shim Pak contains .001" and .002" shims.
4. Install bearing/bearing plate assembly onto rotor.
5. Tighten collet assembly onto rotor (torque to 17 N•m/150 in. - lbs.).
6. Check clearance between rotor and bearing plate by using a .001" feeler gauge. Clearance should be at .001" to .0015". Adjust clearance by repeating
steps 1-5 with different shim if necessary.
7. Once proper rotor/gap clearance is achieved, install well lubricated 01057 Blades (4) into rotor slots. Dynabrade air lube P/N 95842 is recommended
for lubrication.
8. Install cylinder over rotor. Be sure air inlet holes of cylinder face away from bearing plate.
9. Press 02649 Rear Bearing into 01743 Rear Bearing Plate. Press bearing/bearing plate assembly onto rotor. Be sure that pin and air inlet holes line-up with pin slot
and air inlet holes in cylinder.
Important: Fit must be snug between bearing plates and cylinder. If too tight, rotor will not turn freely. Rotor must then be lightly tapped at press fit end so it
will turn freely while still maintaining a snug fit. A loose fit will not achieve the proper preload of motor bearings.
10. Secure motor housing in padded vise so motor cavity faces upwards.
11. Install motor assembly into housing. Be sure motor drops all the way into housing.
12. Insert 01744 Silencer into exhaust cover and install onto motor housing (torque 17 N•m/150 in. - lbs.).
13. Motor adjustment must now be checked. With motor housing still mounted in vise, pull end of rotor and twist (10-15 lbs. force), rotor should turn freely
without drag. If drag or rub is felt, then increase preload or remove shim. Also, push end of rotor and twist (10-15 lbs. force), rotor should turn freely
without drag. If drag or rub is felt, then deload or add shim.
Valve Body Reassembly:
1. Insert 01469 Speed Regulator Assembly with O-rings into valve body. Secure with 95558 Retaining Ring.
2. Secure valve body in vise using 52296 Repair Collar with air inlet facing upwards.
3. Insert 01464 Seal into housing.
4. Line up hole in valve stem with hole in housing (looking past brass bushing). Insert 01472 Tip Valve so that the metal pin passes through the hole in the
valve stem. Install 01468 Spring (small end towards tip valve).
5. Apply Hernon #940 PST Pipe Sealant to threads of 01494 Inlet Adapter and install valve body (torque 34 N•m/200 in. - lbs.).
6. Install throttle lever and 12132 Pin.
Tool Assembly is complete. Please allow 30 minutes for adhesives to cure before operating tool.
Important: Motor should now be tested for proper operation at 90 PSI. If motor does not operate properly or operates at a higher RPM than marked on the
tool, the tool should be serviced to correct the cause before use. Before operating, place 2-3 drops of Dynabrade Air Lube (P/N 95842) directly into air inlet
with throttle lever depressed. Operate tool for 30 seconds to determine if tool is operating properly and to allow lubricating oils to properly penetrate motor
Loctite® is a registered trademark of Loctite Corp.
3