Miller 900 860 Snelstarthandleiding - Pagina 6
Blader online of download pdf Snelstarthandleiding voor {categorie_naam} Miller 900 860. Miller 900 860 15 pagina's.
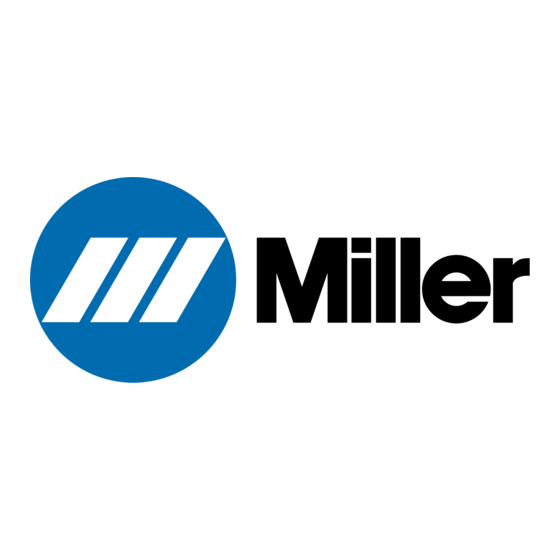
Holes
are
provided
in
the
welding
power
source
base
for
mounting
purposes.
Figure
3.1
gives
overall dimensions and
the base
mounting
hole
layout.
On
most
welding
power
sources
a
lifting
device is
provided
for
moving
the unit.
However,
if
a
fork
lift
vehicle is used for
lifting
the
unit,
be
sure
that the lift forks
are
long enough
to
extend
completely
under the base.
IMPORTANT
The
use
of lift forks
too
short
to
extend
out
of the
opposite
side of the base will expose internal
com
ponents
to
damage
should
the
tips
of the lift forks
~
penetrate
the bottom of the unit.
3-2.
ELECTRICAL INPUT CONNECTIONS
NOTE
It is recommended that
a
Line
Disconnect Switch
be
installed
in the
input
Circuit
to
the
welding
power
source.
This
would
provide
a
safe
and convenient
means
to
completely
remove
all electrical
power from
the
welding
power
source
whenever it is necessary
to
~
perform
any internal
function
on
the unit
CAUTION__j
Before
making
electrical
input
conons
to
the
welding
power
source,
machinery
lockout
proce
dures
should be
employed,
If the
connection is
to
be
made from
a
line disconnect
switch,
the switch should
be
padlocked
in the open
position.
If the
connection is
made from
a
fuse box,
remove
the fuses from the box
and
padlock
the
cover
in the
closed
position.
If lock
ing
facilities
are
not
available,
attach
a
red
tag
to
the
line disconnect
switch
(or
fuse
box)
to
warn
others
that the circuit is
being
worked
on.
A.
Input
Electrical
Requirements
This
welding
power
source
is
designed
to
be
operated
from
a
three
phase,
60
Hertz,
ac
power
supply
which has
a
line
voltage rating
that
corresponds
with
one
of the
primary
volt
ages shown
on
the
welding
power
source
nameplate.
Consult
the local electric
utility
if there is
any
question
about the
type of electrical system available
at
the installation site
or
how proper connections
to
the
welding
power
source
are
to
be made.
B.
Input
Conductor Connections
CAUTION__I!
1
Do
not
connect
the
input
conducto~he
three-
phase
power
supply
until all
input
electrical
connec
~~ions
have been made
to
the
welding
power
source
It is recommended that the
input
conductors be of the
heavy
rubber covered type
or
be installed in solid
or
flexible
con
duit. Select
theproper
size
input
conductors and fuse from
Table 3-1.
Table 3-1.
Input
Conductor and Fuse Size
Input
Conductor
Size.
A6IG
Fuse
Size
(AmperesjJ
Model
208V
230V
460V
575V
208V
230V
460V
575V
750
Amp
(81
181
(8)
175
150
70
60
1000
Amp
(8)
(81
181
200
200
90
80
Numbers
in
I
I
are
ground
conductor
sizes
Insert the three
input
conductors
plus
one
ground
conductor
through
the
access
hole
on
the
rear
panel.
This hole will
accept standard conduit
fittings.
See
Figure
3-2 for hole loca
tion
and size.
NOTE
J
I
It
is recommended that
a
terminal
lug
of
adequate
1
amperage
capacity
be
attached
to
the ends of the
input
and
ground
conductors. The hole diameter
in
the terminal
lug
must
be
of
proper size
to
accommo
date the
line
and
ground
terminal studs
on
the
primary
terminal
board.
Connect the three
input
conductors
to
the terminals
on
the
primary
terminal board labeled L
or
LINE
and
connect
the
ground
conductor
to
the terminal
labeled GRD (See
Figure
3-2).
The
remaining
end of the
ground
conductor should be
connected
to
a
proper
ground.
Use whatever
grounding
method
that
is
acceptable
to
the local electrical
inspection
authority.
CAUTION
The terminal labeled GAD is
connecte~e
welding
power
source
chassis
and
is for
grounding
purposes
only.
Do
not connect
a
conductor from the terminal
labeled GAD
to
any
one
of the L
or
LINE
terminals~as
this will result
in
an
electrically
hot
welding
power
source
chassis.
Figure
3-2.
Input
Conductor Connections
Input
Voltage
Jumper
Links
C.
Matching
The
Welding
Power Source To The Avail
able
Input
Voltage
The
input voltage
umper
links
provided
on
the
primary
ter
minal board
permit
the
welding
power
source
to
be
operated
from various line
voltages.
The various
voltages
from which
this
welding
power
source
may be
operated
are
stated
on
the
welding
power
source
nameplate,
and
on
the
input voltage
label. See
Figure
3-2 for location. The
input voltage
jumper
links
on
this
welding
power
source are
positioned
for the
highest
of the
voltages
stated
on
the
nameplate.
If the
weld
ing
power
source
is
to
be
operated
from
a
line
voltage
which
is
lower than the
highest
voltage
for which the
unit
was
de
signed,
the
jumper
links will have
to
be moved
to
the proper
position
before
operation
of the
welding
power
source
com
mences.
Figure
3-3 shows the various
positions
for which the
jumper
links
may
be
set
on
the standard
welding
power
source.
If the
input voltages
on
the
welding
power
source
nameplate
differ
from those shown in
Figure 3-3,
the
input
voltage
jumper
links
must
be
positioned
as
shown
on
the in
put
voltage
label.
Ground
Line Terminals
Terminal
TA-900
872-2A
Page
6