Dynabrade 10746 Bezpieczeństwo, obsługa i konserwacja - Strona 2
Przeglądaj online lub pobierz pdf Bezpieczeństwo, obsługa i konserwacja dla Szlifierka Dynabrade 10746. Dynabrade 10746 8 stron. 5" random orbital buffer
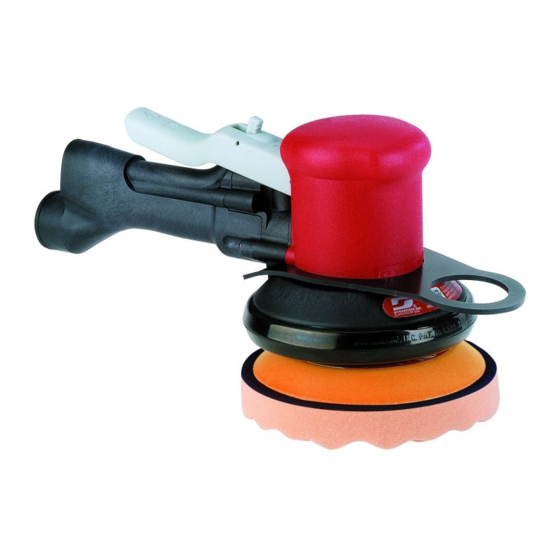
• Secure inlet bushing on air tool with a wrench before attempting to install the air fitting to avoid damaging housing assembly.
• BEFORE MOUNTING AN ACCESSORY, after all tool repairs and whenever a 5" Random Orbital Buffer is issued for use, check tool RPM (speed) with tachometer with air
pressure set at 90 PSIG while the tool is running. If tool is operating at a higher speed than the RPM marked on the tool housing, or operating improperly, the tool must be
serviced and corrected before use.
• Caution: Tool RPM must never exceed abrasive/accessory RPM rating. Check accessory manufacturer for details on maximum operating speed or special
mounting instructions.
• With power source connected at the air tool relieve hose of air pressure and disconnect tool from air supply when changing recommended accessories.
• Connect air tool to power source. Be careful NOT to depress throttle lever in the process.
• Do not expose air tool to inlet pressure above 90 PSIG or (6.2 Bars).
• Caution:After installing the accessory, before testing or use and/or after reassembling tool, the 5" Random Orbital Buffer must be started at a reduced speed to check for
good balance. Gradually increase tool speed. DO NOT USE if tool vibration is excessive. Correct cause, and retest to insure safe operation.
• Use only coated abrasive sanding discs or sheets properly secured to the backing pad provided with the air sander. Ensure that self-fixing sanding discs
are mounted concentrically.
• Make sure that work area is uncluttered, and visitors are at a safe range from the tools and debris. Potentially explosive atmospheres can be caused
by dust and fumes resulting from sanding or grinding. Always use dust extraction or suppression systems which are suitable for the
material being processed.
• Proceed with caution in unfamiliar surroundings. Hidden hazards may exist, such as electricity or other utility lines.
• Air tools are not intended for use in explosive atmospheres and are not insulated for contact with electric power sources.
• Use a vise or clamping device to hold work piece firmly in place.
• Caution:This tool is not to be run at free speed for any length of time. The tool is specifically designed to be low in vibration under load. Running the tool at free speed may
cause the buffing pad to become dislodged from the back-up pad.
• All initial set-up and maintenance to the tool should be done with the air line disconnected from the tool.
• Install air fitting into inlet bushing of tool. The inlet bushing is a 1/4" NPT, for optimal performance of the tool. Either directly couple the air line to the tool or use a quick
couple fitting with a large inlet hole such as Dynabrade's P/N 95675. Important: Secure inlet bushing of tool with a wrench before attempting to install the air fitting to avoid
damaging valve body housing.
• While there may be other applications suited for this tool it has been specifically designed for the automotive market to be used as the second step of a special two step
operation to remove paint imperfections in the clear coat of automotive finishes. The correct back-up pad and buffing pad are required to correctly operate the tool. Attach a
back-up pad to the tool that is compatible with the paint system. A variety of 3M 5" Hook-It pads with a 5/16"-24 male stud have been successful as well as Dynabrade pads,
for best results contact a Dynabrade or 3M representative.
• A waffle pad such as 3M P/N 01912 is required to be attached to the back-up pad. Pre-condition a virgin pad thoroughly with 3M Final Finish Finesse-It Compound 3M P/N
82876 before attaching it to the tool. Once the pad has been conditioned this process need not be done until a new waffle pad is required either due to wear or the com
pound has been allowed to set up rendering the pad useless.
• Apply a small (15mm) dab of Final Finish on the repaired area, and position tool on the repair surface. Apply approximately a 10 pound load on the pad before throttling the
tool on. Adjust the force on the pad as required to feel the "sweet spot" (low vibration). Buff 10-12 seconds flat followed by 2-3 seconds with the tool tipped up on an angle.
Release the throttle lever and then remove the tool from the work piece.
• Installing a new waffle pad can be safely accomplished when the tool is connected to the air line if when holding the tool upside down the operator places their fingers
between the housing and the lever. Holding the tool in this manner eliminates any possibility of the tool turning on during the pad changing operation. It is recommended to
practice this grip with the air line disconnected from the tool to become comfortable with the procedure before performing operation with the air line connected.
• When carrying the tool which is still connected to the air line the operator should insert their thumb between the handle and lever to eliminate possibility of activating the tool.
• Work may generate hazardous dust.
• Do not apply excessive force on tool or apply "rough" treatment to it.
• Always work with a firm footing, posture and proper lighting.
• Ensure that debris resulting from work do not create a hazard.
• This tool is rear exhaust. Exhaust may contain lubricants, vane material, bearing grease, and other materials flushed thru the tool.
Report to your supervisor any condition of the tool, accessories, or operation you consider unsafe.
Regulator
Filter
90 PSIG
(6.2 Bar)
• Dynabrade Air Power Tools are designed to
operate at 90 PSIG (6.2 Bar/620 kPa) maximum
air pressure at the tool inlet, when the tool is
running. Use recommended regulator to control
air pressure.
• Ideally the air supply should be free from moisture.
To facilitate removing moisture from air supply,
the installation of a refrigerated air dryer after the
compressor and the use of drain valves at each
tool station is recommended.
OPERATING INSTRUCTIONS (continued)
Air System
Lubricator
(Sloped in the direction of air flow)
To Tool Station
Drain
Valve
2
Closed Loop Pipe System
Regulator
Filter
Lubricator
Ball
Valve
➤
Drain
Air Hose
Valve
Air Tool
90 PSIG MAX
Drain
(6.2 Bar)
Valve
LUBRICATOR SETTING
1 DROP/MIN.
20 SCFM
Air Flow
Refrigerated
Air Dryer
Ball
Valve
Air Flow
Air Compressor
and Receiver