Dynabrade 56715 Bezpieczeństwo, obsługa i konserwacja - Strona 6
Przeglądaj online lub pobierz pdf Bezpieczeństwo, obsługa i konserwacja dla Szlifierka Dynabrade 56715. Dynabrade 56715 8 stron. 4 hp right angle die grinder. trimmable shroud/right anglerear exhaust
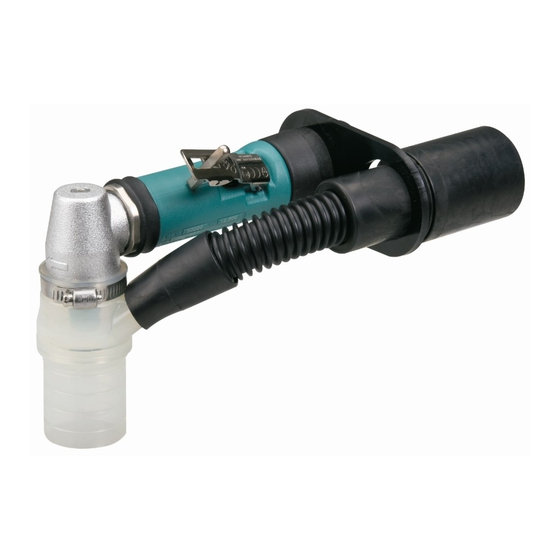
Disassembly/Assembly Instructions - .4 hp/Vacuum Die Grinders (cont.)
11. Install the 01476 Cylinder so that it rests against the 01478 Bearing Plate. Note: Make sure that the air inlet passage of the cylinder properly aligns with the air inlet
passage in the 02676 Rear Bearing Plate.
12. Use the 96242 Bearing Press Tool so that it pushes against the inside race of the 02696 Bearing and install the rear bearing/plate assembly onto the rotor with the arbor
press. Important: Carefully press the rear bearing/plate assembly onto the rotor until it just touches the 01476 Cylinder. A "snug" fit should exist between the bearing plates
and cylinder. If it is too tight the rotor will not turn freely and cause damage to the bearings. If it is too loose the proper bearing preload will not be achieved.
13. Apply a small amount of white grease to the seal of the 02696 Rear Bearing and place the 02679 Shield against the seal of the bearing.
14. Install the motor assembly into the valve housing so that the air passage of the rear bearing plate aligns with the air passage opening inside the valve housing.
15. Place the 52296 Repair Collar around the valve housing and position it in a vise with the pinion gear pointing up. Apply a small amount of Loctite #243 (or equivalent) to the
threads of the valve housing and the 02031 Housing. Install the 01461 Lock Ring onto the 02031 Housing. When connecting these parts, be aware of the right and left
hand threads. Connect the 01461 Lock Ring and angle housing to the valve housing. Use a 34mm (or an adjustable wrench) to tighten the lock ring and angle housing to
the valve housing. (Torque to 34 N•m/300 in. lbs.) SEE: Throttle Positioning Procedure for information on proper throttle lever positioning. Note Steps 4-6.
Motor Assembly Complete.
Angle Housing Assembly:
1. Press the 01041 Gear Oil Fitting into the 02041 Plate.
2. Carefully apply two drops of Loctite #680 (or equivalent) to the recessed area of the 02031 Housing and press the 02041 Plate along with gear oil fitting into the housing.
(Allow 30 minutes for the adhesive to cure.)
3. Press the 02033 Needle Bearing into the housing.
4. Position the 96239 Bearing Press Tool so that it rests against the inside race of the 54520 Bearing and press the bearing onto the spindle.
5. Align the hex shape of the gear with the hex shape of the spindle and press the gear onto the spindle.
6. Apply a small amount of Loctite #243 (or equivalent) to the mating threads of the 02031 Housing. When connecting these parts be aware of the right and left hand threads.
7. Place the 52296 Repair Collar around the valve housing and position the tool in a vise with the angle housing pointing up.
8. Use a 34 mm (or adjustable wrench) to tighten the 01461 Lock Ring while holding the angle housing stationary with one hand. Note: The throttle lever can be located to
any 360˚ position desired. Allow for additional rotation when tightening the lock ring. (Torque to 34 N•m/300 in. lbs.)
9. Position the tool in the vise with the opening for the 02035 Lock Nut facing up.
10. Soak the wicks in the 95848 Gear Oil before installing them into the 02031 Housing. Install the top wick first followed by the bottom wick. Position truncated side of each
wick toward the end of the pinion gear.
11. Install the 02032 Spindle into the angle housing. Apply a small amount of downward force on the spindle while rotating it back and forth checking for the proper backlash or
clearance between the gears. A small amount of backlash or clearance should exist between the bevel and pinion gear teeth. If the gear fit is tight, add shims as necessary.
Place the required thickness of shims between the outside race of the 54520 Bearing and the bearing seat in the housing.
12. Place (1) 01486 Felt Silencer into the 02035 Lock Nut. Apply a small amount of Loctite #567 (or equivalent) to the threads of the 02035 Lock Nut. Use the 50971 Lock Ring
Wrench to install the lock nut onto the 02031 Housing. (Torque to 23 N•m/200 in. lbs.)
13. Place the 52742 Shroud onto housing and secure it with the 97326 Hose Clamp.
Angle Housing Assembly Complete.
Throttle Positioning Procedure:
IMPORTANT: Perform this procedure carefully. Do not entirely separate the 02031 Housing from the valve housing. Loosen the 01461 Lock Ring only enough to make
the throttle lever adjustment.
1. Place the 52296 Repair Collar around the valve housing and secure it in a vise with the 02031 Housing pointing up.
2. Slip the 01547 Collar down onto the valve housing to expose the 01461 Lock Ring.
3. With a firm hold on the 02031 Housing use a 34 mm (or an adjustable wrench) to turn the lock ring clockwise to loosen the 02031 Housing from the valve housing.
4. Place the throttle lever in the desired position. Note: Allow for additional rotation of the 02031 Housing as the 01461 Lock Ring is tightened.
5. Grasp the 02031 Housing firmly to limit rotation. Use a 34 mm (or an adjustable wrench) to tighten the 01461 Lock Ring. (Torque to 34 N•m/300 in. lbs.)
6. Slip the 01547 Collar back over the 01461 Lock Ring.
Throttle Positioning Procedure Complete. Tool Assembly Complete.
Allow 30 minutes for adhesives to cure before operating tool.
Important: To operate the tool, place 2-3 drops of Dynabrade Air Lube (P/N 95842) directly into air inlet with throttle lever depressed. Connect the tool to the air sup-
ply and operate for 30 seconds to allow the lubricant to permeate the motor. Run the tool @ 90 PSIG (6.2 Bar) operating air inlet pressure. Use a tachometer to check
the spindle speed (RPM). If the spindle speed exceeds the RPM that is marked on the motor housing, the tool should be serviced to correct the over speed condition
before the tool is put into use.
All Dynabrade portable pneumatic power tools are rigorously inspected and performance tested in our factory before shipping to our customers. If a Dynabrade tool
develops a performance problem and an inherent defect is found during normal use and service, Dynabrade will warrant this tool against defects in workmanship and
materials for the lifetime of the tool. Upon examination and review at our factory, Dynabrade shall confirm that the tool qualifies for warranty status, and will repair or
replace the tool at no charge to the customer. Normally wearable parts and products are NOT covered under this warranty. Uncovered items include bearings, contact
wheels, rotor blades, regulators, valve stems, levers, shrouds, guards, O-rings, seals, gaskets and other wearable parts. Dynabrade's warranty policy is contingent upon
proper use of our tools in accordance with factory recommendations, instructions and safety practices. It shall not apply to equipment that has been subjected to misuse,
negligence, accident or tampering in any way so as to affect its normal performance. To activate lifetime warranty, customer must register each tool at
www.dynabrade.com. Dynabrade will not honor lifetime warranty on unregistered tools. A one-year warranty will be honored on all unregistered portable pneumatic
power tools. Lifetime warranty applies only to portable pneumatic tools manufactured by Dynabrade, Inc. in the USA. Lifetime warranty applies only to the original tool
owner; warranty is non-transferable.
All Dynabrade motors use the highest quality parts and metals available and are machined to exacting tolerances. The failure of quality pneumatic motors can most often be
traced to an unclean air supply or the lack of lubrication. Air pressure easily forces dirt or water contained in the air supply into motor bearings causing early failure. It often
scores the cylinder walls and the rotor blades resulting in limited efficiency and power. Our warranty obligation is contingent upon proper use of our tools and cannot apply to
equipment which has been subjected to misuse such as unclean air, wet air or a lack of lubrication during the use of this tool.
Lifetime Warranty
Notice
6