djm direct DJMMIG195 Podręcznik - Strona 6
Przeglądaj online lub pobierz pdf Podręcznik dla System spawania djm direct DJMMIG195. djm direct DJMMIG195 15 stron.
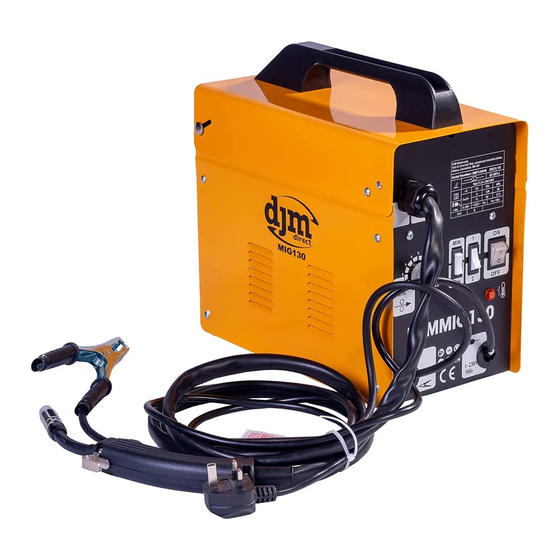
electrode circuit unless the welding power source is off. b)
Equipment without output on/off control (no contactor) Welding
power sources used with shielded metal arc welding and similar
processes may not be equipped with welding power output on/off
control devices. With such equipment the electrode is electrically
LIVE when the power switch is turned ON. Never touch the electrode
unless the welding power source is off.
g) Safety devices
Safety devices such as interlocks and circuit breakers should not be
disconnected or shunted out. Before installation, inspection, or
service of equipment, shut OFF all power and remove line fuses (or
lock or red-tag switches) to prevent accidental turning ON of power.
Do not open power circuit or change polarity while welding. If, in an
emergency, it must be disconnected, guard against shock burns, or
flash from switch arcing. Always shut OFF and disconnect all power to
equipment. Power disconnect switch must be available near the
welding power source.
6.Preparation Of The Working Area
The working area must be sufficiently spacious, not humid, and
well-ventilated as to avoid any fumes which develop from the
welding process and from incidental material adhering to the pieces
to be welded (oils, paints, tars...) which may cause annoyance to the
operator. Avoid welding by contact with humid parts nearby
combustible liquids. Least of all, do not weld upon tanks which may
contain flammable residuals.
ADDITIONAL SAFETY PRECAUTIONS FOR MIG WELDING
✔ALWAYS ensure that there is full free air circulating
around the outer casing of the machine, and that the
louvres are unobstructed.
✔Welding arc can seriously damage your eyes. Both
operator and spectators must ALWAYS use a proper
welding face shield or helmet, with suitable filter lenses.
Proper gloves and working clothes should be worn at all
times.
✔ALWAYS inspect the hose before use to ensure it is in
good condition.
✔ALWAYS keep the free length of hose outside the
work area.
✔ALWAYS remove all flammable materials from the
welding area.
✔ALWAYS Keep fire extinguisher handy....'Dry Powder,
C02 or BCF, NOT Water
✗ NEVER remove any of the panels unless the machine
is disconnected from the supply, AND never use the
machine with any of the panels removed.
✗ NEVER attempt any electrical or mechanical repair
unless your are a qualified technician. If you have a
problem with the machine contact your local dealer.
✗ NEVER use or store in a wet/damp environment. DO
NOT EXPOSE TO RAIN.
✗ NEVER continue to weld, if, at any time, you feel
even the smallest electric shock.
Stop welding IMMEDIATELY, and DO NOT attempt to use
the machine until the fault is diagnosed and corrected.
✗ NEVER point the MIG torch at any person or animal.
✗ NEVER touch the MIG torch nozzle until the welder is
switched OFF and the nozzle has been allowed to cool
off.
✗ NEVER connect, disconnect, or attempt to service
the MIG torch,
until the machine is switched OFF and disconnected
from the mains
supply.
✗ NEVER allow the cables to become wrapped around
the operator or any person in the vicinity.
DANGER – ELECTRIC SHOCK CAN BE FATAL.
A Person qualified in first aid should always be
present in the working area. If person is unconscious
and electric shock is suspected, do not touch the
person if he or she is in contact with the welder or
cables. Disconnect the welder from the power
source and then use first aid . Dry wood, or other
insulating material can be used to move cables, if
necessary, away from the person.
7.Safety Equipment
A comprehensive range of safety equipment for use
when welding is available from your local dealer.
NO-GAS WELDING – PRINCIPLES OF OPERATION
MIG (Metal Inert Gas) welding is a process in which a
power wire electrode is fed continuously into the weld
pool at a controlled, constant rate.
The wire is connected to the negative side of a rectified
voltage supply. The workpiece is connected to the
positive side of the supply.
When the wire is fed, it comes into contact with the
workpiece and an arc is struck. The arc melts the wire
and the material, fusing it together.
The wire, which is fed by the wire feed motor is fed into
the weld pool, burning itself off at a rate dependent
upon the selected wire feed speed.
5