Dodge HYDROIL TORQUE-ARM HXT525C Podręcznik wymiany części - Strona 5
Przeglądaj online lub pobierz pdf Podręcznik wymiany części dla Urządzenia przemysłowe Dodge HYDROIL TORQUE-ARM HXT525C. Dodge HYDROIL TORQUE-ARM HXT525C 12 stron.
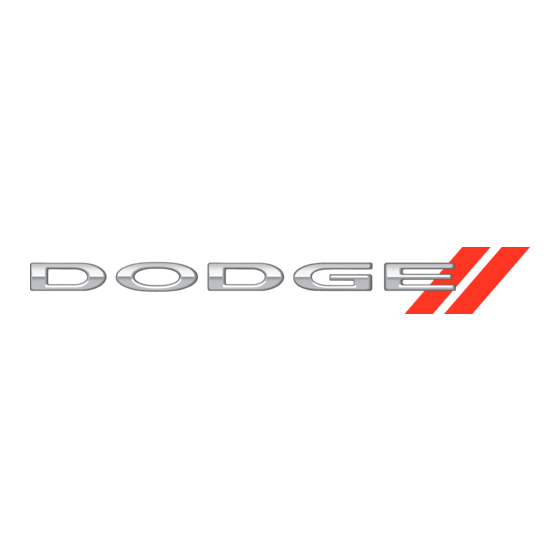
REMOVING TAPER BUSHED REDUCER FROM
SHAFT
WARNING: External loads may cause machine movement.
Block machine before removing any drive train
components. Failure to observe these precautions could
result in bodily injury.
1.
Remove bushing screws.
2.
Place the screws in the threaded holes provided in the
bushing flanges. Tighten the screws alternately and
evenly until the bushings are free on the shaft. For ease of
tightening screws make sure screw threads and threaded
holes in bushing flanges are clean.
3.
Remove the outside bushing, the reducer and then the
inboard bushing.
DISASSEMBLY
1.
Remove all bolts from housing. Drive back hollow dowel
pins on either side of housing. Remove backup plates and
snap rings on the output hub on taper bushed reducers.
Open housing evenly to prevent damage to parts inside.
2.
Lift shaft, gear and bearing assemblies from housing.
3.
Remove seals, seal carriers and bearing cups from
housing.
REASSEMBLY
1.
Output Hub Assembly: Heat gear to 325º to 350ºF for
shrinking onto output hub. Heat bearing cones to 270º to
290ºF for shrinking onto output hub.
2.
Countershaft Assembly: Heat gear to 325º to 350ºF and
bearing cones to 270º to 290ºF for shrinking onto shaft.
3.
Input Shaft Assembly: Shaft and pinion are integral. Heat
bearing cones to 270º to 290ºF for shrinking onto shaft.
4.
Drive the dowel pins back into position in the right hand
housing half.
5.
Install countershaft cover in right-hand housing half. Place
housing half on blocks to allow for protruding End of output
hub. Install bearing cups in right-hand housing half making
sure they are properly seated.
6.
Mesh output hub gear and small countershaft gear together
and set in place in housing. Set input shaft assembly in
place in the housing. Make sure bearing rollers (cones) are
properly seated in their cups. Set bearing cups for left-
hand housing half in place on their rollers.
7.
Clean housing flange surfaces on both halves, making
sure not to nick or scratch flange face. Place a new bead
of gasket eliminator on flange face and spread evenly over
entire flange leaving no bare spots. Place other housing half
into position and tap with a soft hammer (rawhide not lead
hammer) until housing bolts can be used or draw housing
halves together. Torque housing bolts per torque values
listed below
8.
Place output hub seal carrier in position without slims and
install two carrier screws diametrically opposed. Torque
each screw to 25 lb.-ins. Rotate the output hub to roll in
the bearings and then torque each screw once to 50 lb.-
ins. Do not retorque screws. Again turn output hub to roll
in the bearings. With a feeler or taper gage, measure the
gap between the housing and the carrier, clockwise from
and next to each screw. To determine the required shim
thickness, take the average of the two feeler gage readings.
Remove carrier and install the required shims. Note: Total
shim thickness per carrier should not include more than
.009" plastic shims and each plastic shim should be
inserted between two metal shims. Place a 1/8" diameter
bead of Dow Corning RTV732 sealant on the face around
the I.D. of the end shim (sealant is to be between reducer
housing and shim) and install carrier on reducer housing.
Torque carrier bolts to value shown in Table 5. Output hub
should have an axial end play of .001" to .003".
9.
Adjust the countershaft bearings using the same method
as in step 8 above. The axial end play should be .001" to
.003".
10. Again using the same procedure as in step 8, adjust the
input shaft bearings, except the axial end play should be
.002" to .004".
11. Apply sealant to the input shaft cover gasket and install
input shaft cover in right-hand housing half. Install input
and output seals. Extreme care should be used when
installing seals to avoid damage due to contact with sharp
edges on the input shaft or output hub. This danger of
damage and consequent oil leakage can be decreased by
covering all sharp edges with tape or paper prior to seal
installation. Fill cavity between seal lips with grease. Seals
should be pressed or tapped with a soft hammer evenly
into place in the carrier applying pressure only on the outer
edge of the seals. A slight oil leakage at the seals may be
evident during initial running in but should disappear unless
seals have been damaged.
12. Install bushing back-up plate and snap rings.
5