Dodge Sleevoil SSL 9 XC Instrukcja obsługi - Strona 3
Przeglądaj online lub pobierz pdf Instrukcja obsługi dla Urządzenia przemysłowe Dodge Sleevoil SSL 9 XC. Dodge Sleevoil SSL 9 XC 8 stron. Pillow blocks
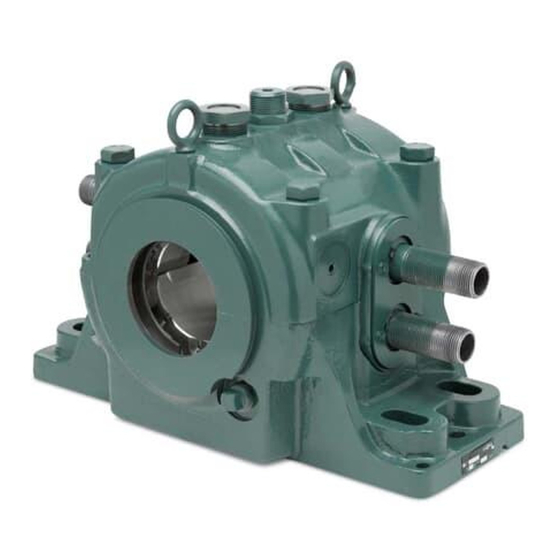
14. The oil level gauge may be located any distance from the
pillow block by the use of a coupling and pipe of the desired
length. The extended pipe must be supported so that it
remains straight and perfectly level. Use a spirit level—Do
not guess. Use pipe sealer on all connections.
NOTE: If bearing is to be arranged for circulating oil,
discard oil level gauge.
15. Remove all unused housing plugs and reinstall using pipe
sealer. Tighten securely.
16. Check construction drawing and/or equivalent manual
whether coolant pipes are to be connected. If no connection
is required, pipes can remain open. Otherwise, make pipe
connections required for coolant, making sure that all pipe
lengths are correct and unions are well aligned.
Careless fitting will result in serious preloading of bearing.
Lengths of flexible hose between pillow block and rigid
piping are recommended to avoid preloading of bearing.
If water or glycol is used for coolant, the flexible hose can be
of reduced size. A regulating valve should be placed ahead
of the inlet and a sight drain at the outlet for liquid coolants.
The recommended method of pipe connection for liquid
coolants is to connect the inlet to one pipe and the outlet to
the other pipe on the same side of the bearing. A return is
then used to connect the two pipes on the other side of the
bearings. (See illustration). Adjust coolant flow rate specified
on construction drawing or to suit conditions (See Table 1).
When using air as the cooling medium, connect an inlet to
each pipe on one side of the bearing and an outlet to the
pipes on the other side.
17. Each housing base has predrilled holes for doweling bearing
to base plate.
18. Crossover hose can be reduced to either 1/2" hose for 6
g.p.m. or less or 3/4" hose for 6 to 14 g.p.m. based on a max.
flow velocity of 10 ft./sec.
LUBRICATION and OPERATION
Since the satisfactory operation of the pillow block depends
almost entirely on the oil film being maintained between the
shaft and liner bearing surface, it is recommended that a high
grade straight mineral oil with rust and oxidation (R&O) inhibitors
and anti-foam agents be used. Check equipment specifications
for specific recommendation of oil viscosity by equipment
manufacturer. If no viscosity is recommended, the following
chart can be used as a guide. Information regarding qualities
and properties of specific oils should be referred to the lubricant
manufacturer.
Pillow
Max. Speed
Block
for Ring
Size
Oiling (R.P.M.)
①
9
1273
10
1146
12
955
Converted from 3000 F.P.M. Speeds above 3000 require Circulating Oil.
Based on 90˚F ambient temperature and 90˚F water inlet temperature. Cooler ambient and (or) water inlet temperatures require less flow.
Pressure drop across bearing—Approx. 1 P.S.I.
Based on 90˚F ambient and 90˚F are inlet temperatures. Cooler ambient and (or) air inlet temperatures require less flow.
Minimum back pressure required for proper air circulation thru the liner coolant chambers.
Flow rate required at 120˚F oil inlet temperature, 90˚F ambient temperature and at 6000 fpm shaft speed under maximum radial load.
Slower speeds and lighter loads require less flow.
Volume of oil required to fill pillow block to top of center circle in oil gage. Applies to both XC and Plain Pillow Blocks.
32 fl. oz=1 qt.=.94636 liters.
Table 1 - Coolant Flow Rate
Normal
Normal
Water Flow
Air Flow
Rate (G.P.M.)
Rate (C.F.M.)
②
③
8.00
225
9.00
207
10.00
277
Use high grade, high quality, well refined petroleum oils of the
straight mineral type, with rust and oxidation inhibitor and anti-
foam agent only.
NOTE: The recommended oil temperature at start-up is 70º
MINIMUM.
Oil film temperature in liner during operation should not exceed
180˚F. If in doubt consult equipment manufacturer. Low ambient
and operating temperatures can be as harmful to the bearing as
high temperatures. A heater and thermoswitch would be required
for such applications.
Fill the pillow block with oil to the top of the center circle in the
oil gage. Remove inspection covers and check to make sure oil
rings are bringing up oil. Operation should be checked frequently
during the first few days. After some running of base loaded
bearings only, loosen plunger screw 1/4 turn, then retighten. This
will allow the liner to align with the shaft. For cap loaded bearings
follow installation procedure. If noise develops, check alignment
of housing, collar runout, plunger screw and all operating parts.
Check all points and make sure all screws and nuts are tightened
after several days operation.
Maintain oil level at center of oil gauge at all times while unit
is in operation.
Oil Maintenance Schedule
Drain, flush, and refill with oil after 2 or 3 weeks of initial break-
in operation. Since the satisfactory operation of the bearing
depends entirely on an oil film being maintained between the
shaft and the bearing liner surface, it is recommended that an oil
analysis be performed at these regular intervals.
•
Every 3 months for 24 hour/day service
•
Every 6 months for 8 hour/day service
Acceptability of oil should be referred to the
manufacturer. If oil quality is acceptable then repeat this procedure
in 3 month intervals. Visually check oil for contamination between
oil analysis checks. Oil service life depends upon several factors
such as ambient conditions, operating temperatures and
frequency of bearing starts and stops. It is recommended that
the oil be changed at least once per year for unfiltered static
applications. Removing contaminants through the use of either
the OLF-2 (Oil Level and Filtration) Unit or a circulating oil system
can extend oil service life. Consult equipment manufacturer for
more information.
Pressure
Oil Flow
Drop Req'd for
Rate for
Air Cooling
Circ. Oil
(P.S.I)④
(G.P.M.) ⑤
.90
8.5
.35
9.0
.18
11.5
3
Oil Volume ⑥
Fl. Oz.
Qts. Approx.
⑥
⑦
Plain
XC
Plain
XC
320
320
10
10
320
640
10
20
640
704
20
22
lubricant
Liters Approx.
⑦
Plain
XC
9.50
9.50
9.50
19
19
21