Dover Wilden Advanced Series Engenharia, exploração e manutenção - Página 8
Procurar online ou descarregar pdf Engenharia, exploração e manutenção para Bomba de água Dover Wilden Advanced Series. Dover Wilden Advanced Series 19 páginas. Metal pumps
Também para Dover Wilden Advanced Series: Engenharia, exploração e manutenção (19 páginas)
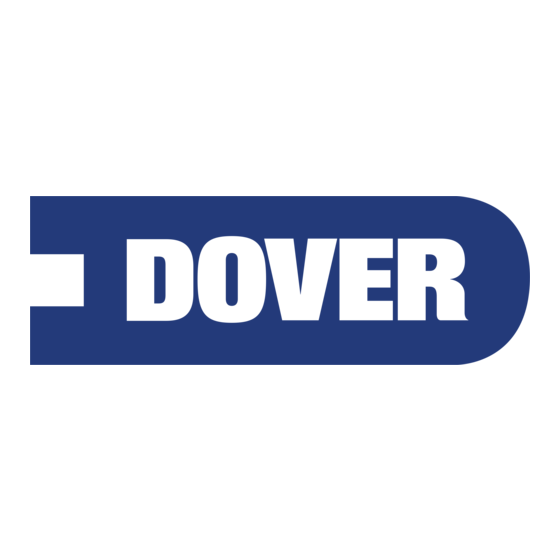
SECTION 6A
SUGGESTED INSTALLATION
The H25/1600S has a 13 mm ( ₁ ⁄₂") inlet and 6 mm
( ₁ ⁄₄") outlet and is designed for discharge pressure to 110.3
bar (1600 psig). Refer to Section 5 for performance charac-
teristics. The H25/1600S pump is manufactured with
wetted parts of aluminum. The H25/1600S is available with
an aluminum air valve.
The suction pipe size should be at least 13 mm ( ₁ ⁄₂")
diameter or larger if highly viscous material is being
pumped. The suction hose must be non-collapsible, rein-
forced type as the H25/1600S is capable of pulling a high
vacuum. Discharge piping should be at least 6 mm ( ₁ ⁄₄") and
must have a minimum pressure rating of 110.3 bar (1,600
psig); larger diameter can be used to reduce friction losses.
It is critical that all fittings and connections are airtight or a
reduction of pump suction capability will result.
All wiring used to operate the pump should be placed and
connected according to all applicable electrical codes. It is
important that the wiring be of adequate gauge to carry the
current required to operate the pump. In addition, it is
necessary that the electrical power supply be large enough
to supply the current required to operate the pump. Wiring
should be above ground level if possible (in case of fluid
spill or leakage), and all wiring and connections which
could become wet or damp should be made watertight.
INSTALLATION: Months of careful planning, study, and
selection efforts can result in unsatisfactory pump perfor-
mance if installation details are left to chance.
Premature failure and long term dissatisfaction can be
avoided if reasonable care is exercised throughout the
installation process.
LOCATION: Noise, safety, and other logistical factors
usually dictate where equipment will be situated on the
production floor. Multiple installations with conflicting
requirements can result in congestion of utility areas, leav-
ing few choices for additional pumps.
Within the framework of these and other existing conditions,
every pump should be located in such a way that five key
factors are balanced against each other to maximum
advantage.
ACCESS: First of all, the location should be accessible. If
it's easy to reach the pump, maintenance personnel will
have an easier time carrying out routine inspections and
adjustments. Should major repairs become necessary, ease
of access can play a key role in speeding the repair process
and reducing total downtime.
AIR SUPPLY: Every pump location should have an air line
large enough to supply the volume of air necessary to
achieve the desired pumping rate (see Section 5). Use air
pressure up to a maximum of 8.6 bar (125 psig) depending
on pumping requirements.
For best results, the pumps should use a 5µ (micron) air
filter, needle valve and regulator. The use of an air filter
before the pump will ensure that the majority of any pipeline
contaminants will be eliminated.
ELEVATION: Selecting a site that is well within the pump's
dynamic lift capability will assure that loss-of-prime trou-
bles will be eliminated. In addition, pump efficiency can be
adversely affected if proper attention is not given to site
location.
PIPING: Final determination of the pump site should not be
made until the piping problems of each possible location
have been evaluated. The impact of current and future
installations should be considered ahead of time to make
sure that inadvertent restrictions are not created for any
remaining sites.
The best choice possible will be a site involving the short-
est and straightest hook-up of suction and discharge
piping. Unnecessary elbows, bends, and fittings should be
avoided. Pipe sizes should be selected so as to keep fric-
tion losses within practical limits. All piping should be
supported independently of the pump. In addition, the
piping should be aligned so as to avoid placing stress on
the pump fittings.
If the pump is to be bolted down to a solid location, a
mounting pad placed between the pump and the founda-
tion will assist in minimizing pump vibration.
If the pump is to be used in a self-priming application, be
sure that all connections are airtight and that the suction lift
is within the model's ability.
When pumps are installed in applications involving flooded
suction or suction head pressures, a gate valve should be
installed in the suction line to permit closing of the line for
pump service.
THE MODEL H25/1600S SHOULD NOT BE USED WITH
MEDIA CONTAINING SOLIDS. WHENEVER THE POSSIBIL-
ITY EXISTS THAT SOLID OBJECTS MAY BE SUCKED INTO
THE PUMP, A STRAINER SHOULD BE USED ON THE
SUCTION LINE.
CAUTION: THE H25/1600S PUMP IS DESIGNED FOR
OPEN LOOP SYSTEMS.
CAUTION: DO NOT EXCEED 8.6 BAR (125 PSIG) AIR
SUPPLY PRESSURE.