Addison DC Series Manual de instalação, operação e manutenção - Página 13
Procurar online ou descarregar pdf Manual de instalação, operação e manutenção para Ar condicionado Addison DC Series. Addison DC Series 19 páginas. High efficiency packaged air conditioning systems
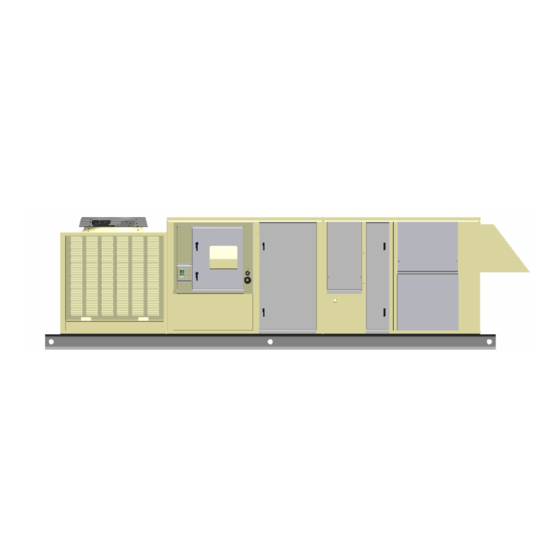
TROUBLE SHOOTING GUIDES
General Refrigeration Circuit
SYMPTOM
1. Power off, loose electrical connections or fuse open.
2. Compressor contactor not closing.
A.Compressor will not start
3. Internal compressor thermal overload open.
4. Compressor defective.
5. High or low pressure switch open or defective.
6. Oil pressure control open or defective.
1. Low refrigerant charge
2. Airflow restricted.
B.Compressor starts but cuts out on
low pressure switch.
3. Restriction in liquid line.
4. Defective low pressure switch.
1. Refrigerant overcharge.
2. Condenser fan control has incorrect setting.
3. Fan motor defective.
C. Compressor starts but cuts out on
4. Condenser coil inlet obstructed or dirty.
high pressure switch.
5. Air or non-condensables in system.
6. Defective high pressure switch.
7. Restriction in discharge or liquid line.
1. Low voltage.
2. Sustained high discharge pressure.
3. High suction and discharge pressures.
D. Compressor cuts out on thermal
4. Defective compressor overload.
overload.
5. Defective run capacitor.
6. Improper refrigerant charge.
7. Bearings or pistons too tight.
8. Allow time for compressor to cool.
1. Low oil level.
E. Compressor cuts out on oil failure
2. Defective oil pump.
control (semi-herm.)
3. Defective control.
4. Liquid refrigerant is entering crankcase.
1. Scroll compressors are rotation sensitive.
2. Refrigerant overcharge.
3. Excessive or insufficient oil in compressor
F. Noisy compressor.
4. Liquid floodback.
5. Tubing rattle.
6. Compressor defective.
12
POSSIBLE CAUSE
1. Check disconnect switch, fuses and wiring. Replace parts or repair as necessary.
2. Check voltage to contactor coil, transformer, slave relay, system. Replace parts as necessary.
3. If compressor is hot, allow 2 hours to cool. See thermal overload below.
4. Check compressor for electrical failure. Compressor may be seized, check for L.R.A.
5. Check calibration of high or low pressure switch, re-calibrate or replace.
6. Check oil failure control. See oil failure control below.
1. Check sightglass and check pressures.
2. Check for dirty evaporator coil, dirty filters, dampers closed, iced evaporator, proper belt
adjustment, proper motor amps, duct design
3. Check head pressure, check and adjust TXV if not functioning properly, check pressure drop
across filter drier.
4. Check calibration of switch.
1. Check pressures, charge by sub cooling.
2. Check calibration of low ambient control.
3. Check fan motor.
4. Check coil and inlet clearances and for possible air recirculation.
5. Check high side equalized pressure reading with equivalent outdoor temperature.
6. Check calibration of switch.
7. Check discharge and liquid line pressures, check TXV.
1. Check voltage.
2. Check running amperage and conditions described under "high discharge pressure."
3. Check TXV setting, check for air in system.
4. Allow compressor to cool for two hours if compressor is hot. Recheck for open circuit.
5. Check run capacitor for compressor and fan motor.
6. Check subcooling.
7. Check for low oil level.
8. Check dome temperature of the compressor.
1. Check crankcase sightglass - add oil to bring level to midway in sightglass.
2. Check oil pump.
3. Check oil failure control for calibration.
4. Compressor will be wet. Check crankcase heater or cause for liquid feedback.
1. Reverse wiring at disconnect switch, recheck for correct evaporator blower rotation.
2. Check pressures and subcooling.
3. Check oil level in hermetic compressors. Check total e
4. Check TXV setting. Check for refrigerant overcharge. oil as recommended.
5. Dampen tubing vibration by taping or clamping. Bend tubing away from contact where possible.
6. Check internal parts (semi-herm.)
REMEDY
crankcase.