Miller Copilot Manual do Proprietário - Página 8
Procurar online ou descarregar pdf Manual do Proprietário para Sistema de soldadura Miller Copilot. Miller Copilot 48 páginas. Collaborative welding system
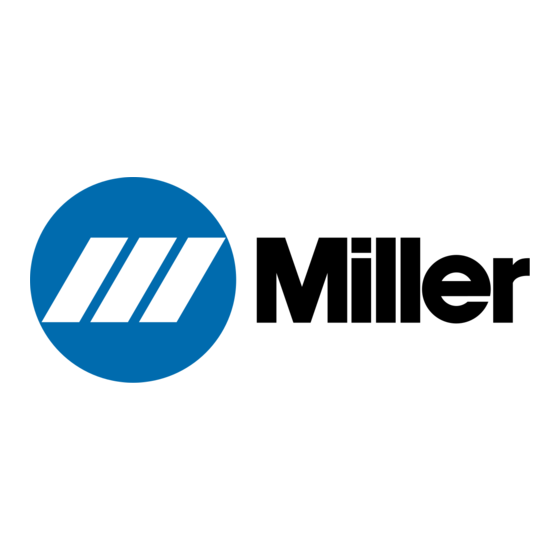
ARC WELDING can cause
interference.
� Electromagnetic energy can interfere with sensitive
electronic equipment such as microprocessors,
computers, and computer-driven equipment such
as robots.
� Be sure all equipment in the welding area is electromagnetically
compatible.
1-4.
Maintenance and Repair
MAINTENANCE and REPAIR WORK
must follow all safety instructions in
this manual.
Maintenance, calibration, and repair work must be
performed in accordance with the latest versions of
Service Manuals.
Follow all regional and national safety requirements and always test
whether all safety functions work properly.
Prior to operating the Cobot manipulator or control box, please follow
the procedures and warnings below:
� Before
performing
maintenance,
procedures.
� Remove the main input power cable from the control box to ensure
the power is off.
� Check the grounding connection before switching on the power of
the Cobot system.
1-5.
California Proposition 65 Warnings
WARNING – This product can expose you to chemicals in-
cluding lead, which are known to the state of California to
cause cancer and birth defects or other reproductive harm.
1-6.
Principal Safety Standards
Safety in Welding, Cutting, and Allied Processes, American Welding
Society standard ANSI Standard Z49.1. Website: http://www.aws.org.
Safe Practice For Occupational And Educational Eye And Face Pro-
tection, ANSI Standard Z87.1, from American National Standards In-
stitute. Website: www.ansi.org.
Safe Practices for the Preparation of Containers and Piping for Weld-
ing and Cutting, American Welding Society Standard AWS F4.1.
Website: http://www.aws.org.
National Electrical Code, NFPA Standard 70 from National Fire Pro-
tection Association. Website: www.nfpa.org.
Safe Handling of Compressed Gases in Cylinders, CGA Pamphlet P-
1 from Compressed Gas Association. Website: www.cganet.com.
Safety in Welding, Cutting, and Allied Processes, CSA Standard
W117.2 from Canadian Standards Association. Website:
csagroup.org.
Standard for Fire Prevention During Welding, Cutting, and Other Hot
Work, NFPA Standard 51B from National Fire Protection Association.
Website: www.nfpa.org.
OSHA, Occupational Safety and Health Standards for General Indus-
try, Title 29, Code of Federal Regulations (CFR), Part 1910.177 Sub-
part N, Part 1910 Subpart Q, and Part 1926, Subpart J. Website:
www.osha.gov.
OSHA Important Note Regarding the ACGIH TLV, Policy Statement
on the Uses of TLVs and BEIs. Website: www.osha.gov.
Applications Manual for the Revised NIOSH Lifting Equation from the
National Institute for Occupational Safety and Health (NIOSH). Web-
site: www.cdc.gov/NIOSH.
OM-291865 Page 4
follow
lockout/tag
out
For more information, go to www.P65Warnings.ca.gov.
American National Standard for Industrial Robots and Robot Systems
– Safety Requirements, ANSI/RIA R15.06-2012, Robotic Industries
Association. Website: www.robotics.org.
Robotic Industries Association Technical Report – supplement to AN-
SI/RIA R15.06-2012, RIA TR 15.406-2014, Robotic Industries Associ-
ation. Website: www.robotics.org.
Technical Report for Industrial Robots and Robot Systems – Safety
Requirements, Task-based Risk Assessment Methodology, RIA TR
R15.306-2014. Website: www.robotics.org.
Electrical Standard for Industrial Machinery, NFPA Standard 79, from
National Fire Protection Association. Website: www.nfpa.org.
Safety Standard for Robots and Robotic Equipment, UL 1740. Web-
site:www.ulstandards.ul.com.
Industrial robots and robot systems, CAN/CSA-Z434, Canadian
www.
Standards Association (CSA). Website: www.csa.ca.
Technical Specification Robots and Robotic Devices- Collaborative
Robots, ISO/TS 15066:2016.
Safety of Machinery – General Principles for Design – Risk Assess-
ment and Risk Reduction, ISO 12100:2010.
Robots and Robotic Devices – Safety Requirements– Part 2: Industri-
al Robot Systems and Integration, ISO 10218-2:2011.
Safety of Machinery; General Requirements & Risk Assessment, AN-
SI B11.0-2010.
Low-voltage switchgear and controlgear – Part 5-5: Control circuit de-
vices and switching elements – Electrical emergency stop device with
mechanical latching function, IEC 60947-5-5.
Cobot System 2023–02
� To reduce possible interference, keep weld cables as short as
possible, close together, and down low, such as on the floor.
� Locate welding operation 100 meters from any sensitive electronic
equipment.
� Be sure this welding machine is installed and grounded according
to this manual.
� If interference still occurs, the user must take extra measures such
as moving the welding machine, using shielded cables, using line
filters, or shielding the work area.
� Observe ESD (Electro-Static Discharge) procedures when parts
of the Cobot manipulator or control box are disassembled.
� There are no serviceable parts in the controller. If service is re-
quired, please contact Miller Electric.
� Avoid disassembling the power supply connections located inside
the controller. High voltages can be present at the power supply
connections for several hours after the control box has been
switched off.
� Prevent water and dust from entering the Cobot manipulator or
controller.
� Changing torch weight can affect force limits, which can cause in-
jury. Contact Miller Welding Automation Service to determine
safety settings before changing torch weight.
� Reactivate any deactivated safety measures immediately after
maintenance work is completed.
� Document all maintenance operations completed and save for fu-
ture reference.