KitchenAid KDTE104ESS3 Технический паспорт - Страница 10
Просмотреть онлайн или скачать pdf Технический паспорт для Посудомоечная машина KitchenAid KDTE104ESS3. KitchenAid KDTE104ESS3 12 страниц.
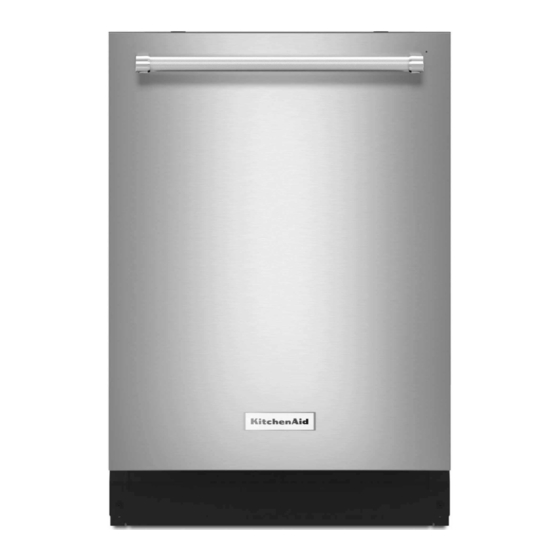
Customer
Potential Causes
Description
Won't Accept Key
Control Lockout
Presses and
feature accidentally
Control Lock LED
turned on by
On
customer.
One or More Keys
1. Stuck key or short
Won't Respond or
circuit(s) in keypad or
Unusual LED/
in control's input lines
Display/Key
that read the keys.
Behavior
2. Capacitive touch
keypad adhesive
coming loose from
console.
3. Loose connections
between keypad and
control and/or bent or
contaminated
connector pins.
4. Excessive
condensation on user
interface parts due to
vent and/or fan
problem.
5. Defective user
interface.
Dishwasher Beeps
1. User opened door
Constantly (for
during cycle and
Models with
closed door without
Beepers)
pressing Start/
Resume to resume
cycle.
2. Normal beeper
operation is excessive
to customer.
Long Cycles and/
1. As part of normal
or Stuck in Certain
operation, the
Part of Cycle
dishwasher pauses 2
or 3 times during the
cycle for thermal
holds and advances
once temperature is
met.
2. OWI soil sensor
picking high soil cycle
too often.
3. Diverter problem
prevented water from
heating (plastic tub
models only).
4. A water heating
problem could cause
long cycles but will
typically cause a
"water heating fault."
Check
Related
Error
Code
Instruct customer. Refer to
Use and Care Guide. Press
and hold Control Lock key
5 seconds to turn On/Off.
Refer to "Service Error
2-1
Codes" table.
1. Unplug dishwasher or
disconnect power.
2. Inspect keypad board for
separation from console.
Replace keypad and
console if separation is
seen.
1. Unplug dishwasher or
2-2
disconnect power.
2. Inspect connections in
user interface circuits.
Reconnect loose
connections. Replace
part(s) if pins are damaged
or contaminated.
- Check error history for
10-3
10-3 fan error.
- Refer to "Service Error
Codes" table.
- Verify presence of vent
current if model has a vent
wax motor.
- Refer to "Leaks or Drips
Onto Cabinet or Floor."
1. Unplug dishwasher or
disconnect power.
2. Replace user interface
console assembly.
Instruct customer.
Dishwasher control is
designed to beep if
dishwasher is in Cycle
Interrupt mode with door
latched. Control will stop
beeping when door is
opened and/or Start/
Resume key is pressed to
resume cycle.
Instruct customer how to
turn beeper off and on.
Press and hold Hi Temp
key for 3 seconds (tone
sounds).
Instruct customer. Explain
thermal holds and how the
cycle pauses when they
occur.
1. Run Service Diagnostics
cycle to check if OWI is
showing high soil with clear
water.
2. Check lens surface.
Clean if needed.
3. Unplug dishwasher or
disconnect power.
4. Replace OWI and run
diagnostics after installing
new OWI to force
calibration on next wash
cycle.
Refer to "Service Error
9-1
Codes" table.
9-2
Refer to "Service Error
7-1
Codes" table.
Customer
Potential Causes
Description
Long Cycles and/
5. Heater takes a long
or Stuck in Certain
time to heat water
Part of Cycle
with low voltage.
(cont.)
6. Incoming water
under 84ºF (29ºC).
7. Suds or air in pump
requires repeated
wash periods.
8. Motor problems
force cycle to start
and stop repeatedly.
9. OWI or NTC sensor
problem.
LEDs or Displays
1. Unit is in Sales
Run For Short
Demo mode.
Time (but No
Loads Running)
and Then Shuts Off
2. Open F8 (Wash
motor fuse) or F9
(Triac load fuse) on
control disabled
loads.
Can Start a Cycle,
1. Control canceled
but Only Runs for a
cycle due to error
Short Time - Cycle
detected with wash
Does Not
motor.
Complete (Clean
2. Unit in Sales Demo
LED or Completed
mode.
May Blink)
Will Not Drain, or
1. Drain loop check
Excess Water Left
valve not sealing.
in Dishwasher.
NOTE: Check error
history. If no error
codes for
electrical
problems, problem
is mechanical. Do
2. Customer
not replace
misunderstands water
control.
level after drain.
3. Draining problem.
10
Check
Related
Error
Code
Check for at least 100 VAC
at power source.
1. Be sure dishwasher is
connected to the hot water
supply.
2. Confirm temperature at
sink (recommend 120°F
[49°C]). Instruct customer
to run water at sink before
running dishwasher.
3. Unplug dishwasher or
disconnect power and
check all connections and
measure resistance in
Temperature Sensing
circuit. Replace OWI if
resistance is high.
Refer to "Service Error
6-3
Codes" table.
Refer to "Service Error
Codes" table.
3-1
Refer to "Service Error
3-3
Codes" table.
Check operation of Cancel
key. If there is no Cancel
LED response to multiple
Cancel key presses, the
control is likely in Sales
Demo mode. Run Service
Diagnostics Cycle to clear
Demo mode.
Refer to "Fuse Service and
Resistance Checks" in
"Meter Check of Loads and
Fuses" section.
Refer to "Service Error
4-3
Codes" table.
Run Service Diagnostics
cycle to clear Demo mode.
1. Disconnect drain hose at
plumbing connection.
2. Elevate hose above
dishwasher and fill with
water. If water flows into
dishwasher, replace entire
drain loop. Install as high
as possible.
Instruct customer. Sump
will normally have about
1" (2.4 cm) of water
remaining in filter cup hole
after cycle.
1. Unplug dishwasher or
8-2
disconnect power.
2. Check for blockages
from sump check valve to
customer's plumbing.
Potential problems,
plugged garbage disposer
or plug not knocked out,
drain loop check valve
stuck, and/or plugged
hoses.
3. Remove drain pump and
check impeller (normally
there is some uneven
resistance). If it is stripped,
replace drain pump.
4. Refer to "Service Error
Codes" table for 8-2.