Miller WeldCraft W-250 Руководство пользователя - Страница 16
Просмотреть онлайн или скачать pdf Руководство пользователя для Фонарик Miller WeldCraft W-250. Miller WeldCraft W-250 25 страниц. W-250 / wp-20 series hand-held water-cooled tig (gtaw) torch
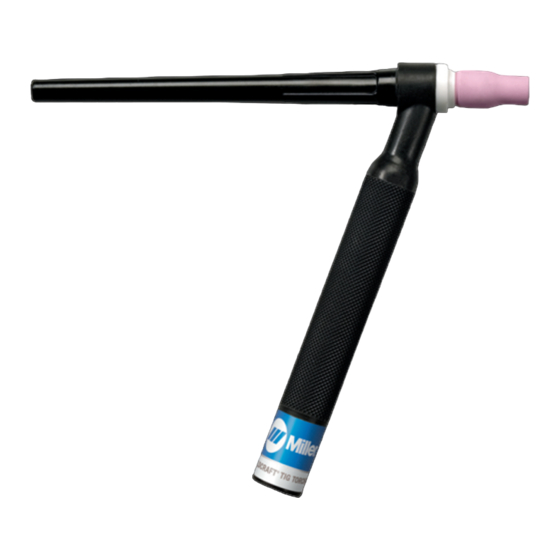
SECTION 5 − MAINTENANCE & TROUBLESHOOTING
5-1. Routine Maintenance
n = Check
* To be done by Factory Authorized Service Agent
Daily
n Nozzle For Cracks − l If Necessary
Weekly
n
Collet For Wear −
l If Necessary
n Power Cable For Cracks,
Monthly
Wear − l If Necessary
*
When using a water-cooled torch, maintain cooling equipment according to the manufacture's recommendations.
5-2. Troubleshooting
.
Before using troubleshooting table, check selection and preparation of tungsten electrode according to Section 6.
Trouble
Arc will not start. High frequency present
and visible at the torch.
Lack of high frequency; difficulty in es-
tablishing arc.
Torch gas valve not working properly (if
applicable).
No shielding gas flow from torch.
Tungsten electrode oxidizing and not re-
maining bright after conclusion of weld.
OM-225 425 Page 12
Z = Change
~ = Clean
n Collet Body Threads −
l If Necessary
n
Gas Hose For
Cracks, Leaks, Wear −
l If Necessary
n Power, Gas, And Water
Cable Connections To En-
sure They Are Tight
Check cable and work connections. Be sure weld circuit is complete (see Section 4-3).
Check and be sure shielding gas is present.
Select proper size and type tungsten. Properly prepare tungsten according to Section 6.
Check cables and torch for cracks or bad connections. Be sure that torch cables are not close to any
grounded metal. Repair or replace necessary parts.
Check torch consumables. Be sure collet and collet body are correctly installed and tightened (see Sec-
tion 4-1).
Check welding power source High Frequency control, and if necessary, check and adjust spark gaps.
Have Factory Authorized Service Station/Service Distributor check valve.
Be sure valves on gas supply are open.
Check cable for kinks or blockage.
Check and tighten all gas supply fittings.
Check cables and torch for cracked insulation or bad connections. Repair or replace (see Section 5-1).
Shield weld zone from drafts.
Increase postflow time.
Increase gas flow rate. Check manufacture's recommendations.
Check and tighten all gas fittings.
Check gas valve and flow meter/regulator.
Select proper size and type tungsten. Properly prepare tungsten (see Section 6).
!
Disconnect torch before maintaining.
l = Replace
n Check Tungsten Preparation (See Section 6)
n Gas Lens Screen −
l If Necessary
*
n
Water Hose, If Applic-
able, For Cracks, Leaks,
Wear − l If Necessary
n
Cable Cover For
Tears, Holes, Or Wear −
l If Necessary
Remedy
n Gas Valve, If Applicable −
l If Necessary
n
Back Cap O-Ring −
l If Necessary