Duff-Norton 6415 Series Kurulum, Çalıştırma ve Bakım Talimatları Kılavuzu - Sayfa 6
Kontrolör Duff-Norton 6415 Series için çevrimiçi göz atın veya pdf Kurulum, Çalıştırma ve Bakım Talimatları Kılavuzu indirin. Duff-Norton 6415 Series 16 sayfaları. Electromechanical linear actuators
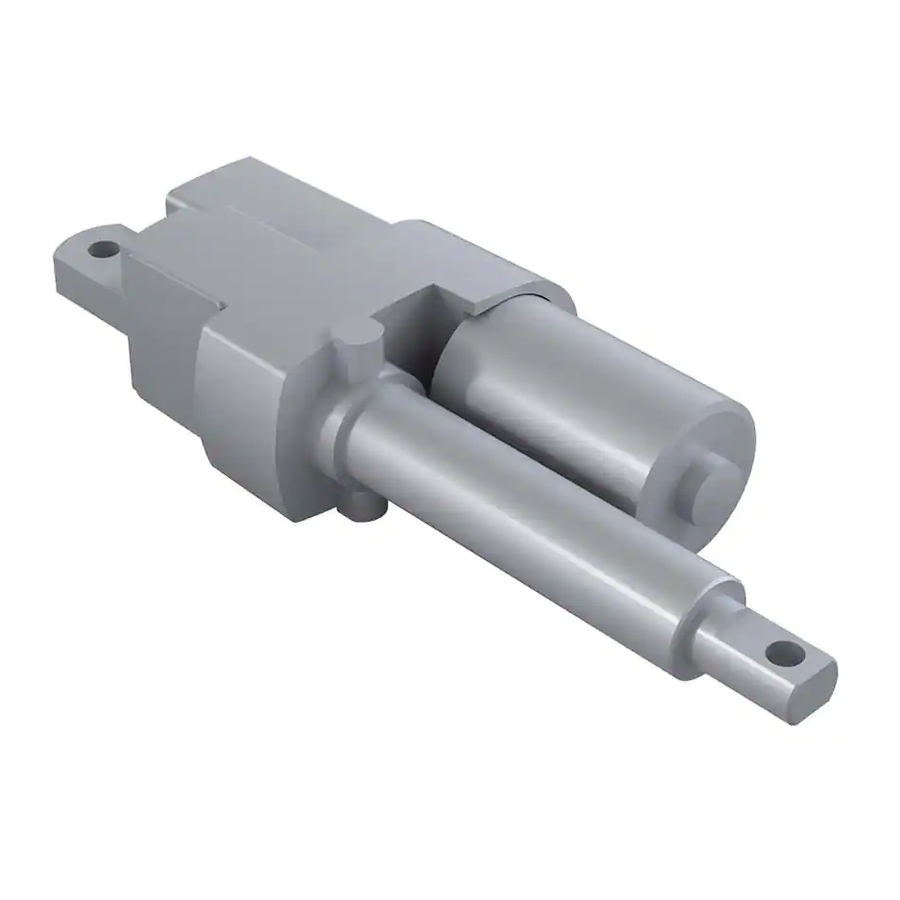
i.
Turn pot shaft counterclockwise until resistance
between terminal S and CCW is approximately
100 ohms. This will be the pot's full retracted
position.
ii. Being careful not to turn the pot shaft, slide it into
engagement with the plastic worm and tighten
locknut.
iii. Re-check resistance. If necessary loosen locknut
slightly and twist pot to re-establish 100 ohm
resistance. Pot does not have end of travel stops,
but has a 20˚ deadband between the two ends
of the resistive element. No continuity will be
measured to terminal S if the slider is in the
deadband.
iv. Run actuator to full extension (do not let
tube rotate) until it is stopped by its limit switch.
v.
Check resistance between S and CCW to be
sure the slider is still on the element and the
resistance is greater than 100 ohms. The pot
has enough rotation for 9.43 inches of travel.
(For strokes shorter than 9 inches, the retracted
resistance can be increased so that pot
adjustment is less critical.
5b. FOR TRAVELS GREATER THAN 9 inches
(multi-turn pot):
3-1. Operational Procedures
This motor is an intermittent duty type motor. Since
the motor draws approximately the same amperage at
no load as at full rated load, it only takes 10 minutes
of cntinuous running, regardless of how light the load
may be, before the thermal overload relay cuts out. It
then takes about 10 minutes before the motor cools
sufficiently for the thermal relay to close. Make sure that
the duty cycle to which the actuator is subjected is not
too severe for the motor.
Avoid using low voltage supply for the motor. All wiring,
switches etc. must be of sufficient capacity to carry the
required current.
The axis of the clevis pins should be parallel so that the
actuator can pivot without binding. The preset brake will
provide consistent braking for the actuator. However,
in the event the brake friction surfaces become worn
as indicated by excessive drift, the brake will require
rebuilding. To aid in rebuilding, a repair kit with step
by step instructions is available through Duff-Norton
Company under repair kit part number SK-6415-41.
i.
Turn pot shaft counterclockwise until it reaches
its stop. Now turn shaft back clockwise 1/4 turn.
ii.
Without turning pot shaft, slide pot onto
engagement with the plastic worm and tighten
locknut.
iii. Starting 1/4 turn from the end, the 3-turn pot has
enough rotation for 25" of actuator travel.
6. With this set-up, potentiometer will have increasing
resistance from S to CCW (and decreasing resistance
from S to CW) as the actuator extends.
2-5. Digital Position Indicator (Duff-Norton
part no. SK6300-4K)
The model SK6300-4K is a highly versatile, panel mount,
digital readout device that provides a very precise
indication of actuator position. It can be programmed
to display percentage, inches, or any other desired
unit. The indicator is self calibrating with no need for
measurements or calculations.
See detailed instructions with the SK6300-4K indicator
for installation and programming instructions.
Potentiometer terminal CCW should be connected to
indicator Common, CW to Excitation Voltage, and S to
Signal Voltage Input.
Section III
Operation
The repair can be performed by the customer or by any
authorized repair station.
This actuator is not recommended for use in
applications where it can be jammed. Examples of
jamming include overtraveling the limit switches
and thus jamming the nut and screw internally at the
extreme ends of the stroke, and driving the actuator
against an immovable object and thus severely
overloading it. This actuator can jam a limited number
of times without damage. Therefore, consult Duff-
Norton Engineering if jamming is expected.
Do not operate actuator before setting limit switches.
Some actuator external surface temperatures may
reach 230˚F at or near maximum allowable duty cycle.
6
WARNING