Danfoss VFG 2 Series Kurulum Kılavuzu - Sayfa 6
Kontrolör Danfoss VFG 2 Series için çevrimiçi göz atın veya pdf Kurulum Kılavuzu indirin. Danfoss VFG 2 Series 20 sayfaları.
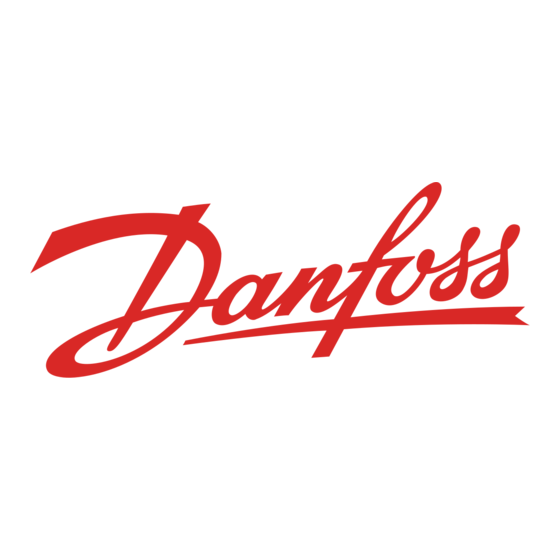
Installation Guide
LANGUAGE
ENGLISH
Safety Notes
Prior to assembly and commissioning to
avoid injury of persons and damages of
the devices, it is absolutely necessary to
carefully read and observe these instructions.
Necessary assembly, start-up, and maintenance
work must be performed only by qualified,
trained and authorized personnel.
Prior to assembly and maintenance work on the
controller, the system must be:
- depressurized,
- cooled down,
- emptied and
- cleaned.
Please comply with the instructions of the
system manufacturer or system operator.
Disposal instructions
This product should be
dismantled and its components
sorted, if possible, in various
groups before recycling or
disposal.
Always follow the local disposal regulations.
Definition of Application
The controller is used for diffe rential pressure
control of water and water glycol mixtures for
heating, district heating and cooling systems.
The technical data on the ra ting plates
determine the use.
Scope of Delivery ❶
*) Impulse tube AF, accessory
Assembly
Admissible Installation Positions ❷
DN 15-80 ①:
medium temperatures up to 120 °C:
Can be installed in any positi on.
DN 100-250 and DN 15-80 ②:
medium temperatures > 120 °C.
Installation permitted only in horizontal
pipelines with the actuator oriented
downwards.
Installation Location and Installation
Scheme ❸
Return mounting ①
Flow mounting ②
Valve Installation ❹
1. Install strainer ① before the controller.
2. Rinse system prior to installing the valve.
3. Observe flow direction ② on valve body.
Flanges ③ in the pipeline must be in
parallel position and sealing surfaces
must be clean and without any damage.
4. Install valve.
5. Tighten screws crosswise in 3 steps up to the
max. torque.
6
DEN-SMT/SI
AFP/VFG 2(21) DN 15-250
Valve Actuator Installation
Valves DN 150-250
The actuator stem must be screwed into
the valve stem.
Observe the Installation In structions for the
valves DN 150-250.
Valves DN 15-125 ❺
1. Place actuator at the valve.
2. Align actuator, observe position of impulse
tube connection to the valve ①
3. Tighten union nut ② Torque 100 Nm
Impulse Tube mounting
When installing seal pots ❻①, please
observe the Installati on Instructions for
the seal pots.
• Which impulse tubes to use?
The impulse tube set AF (2×) ❻② can be
used: Order No.: 003G1391
or use the following pipes:
Stainless steel
Ø 10×0,8
Steel
Ø 10×1
Copper
Ø 10×1
• Connection ❼ of impulse tubes ① in the
system
Installation in return flow ②
Installation in supply flow ③
• Connection ❽ to the pipeline ①
No connection downwards ②, could be
chocked by dirt.
• Impulse Tube Installation (Copper) ❾
1. Cut pipe into rectangular sections ① and
deburr.
2. Insert sleeves ② on both sides.
3. Verify the correct position of the cutting
ring ③.
4. Press impulse tube ④ into the threaded
joint up to its stop.
5. Tighten union nut ⑤. Torque 40 Nm
Insulation ❿
For medium temperatures up to 100 °C the
pressure actua tor may be insulated ①.
Dimensions ⓫
Flanges:
connection dimensi ons acc. to
DIN 2501, seal form C
Dismounting ⓬
Danger
Danger of injury by hot water
Valve without actuator is open ①, Seal ② is in
the ac tuator.
Prior to dismounting depres surize system!
Carry out dismounting in re verse order to
mounting.
VI.CA.K2.1I
Leak and Pressure Test ⓭
Pressure must be constantly increased
at the +/- connec tion ①. Never increase
− pressure above + pressure.
Observe max. permitted pressure, see below.
Non-compliance may cause damages at the
actuator or valve.
Max. test pressure [bar] with connected
impulse tu bes
AFP cm
2
bar
In case of higher test pressu res, remove impulse
tubes at the pipelines ①.
Close connections with plugs G ¼ ISO 228.
Observe nominal pressure ② of the valve.
Max. test pres sure is 1,5 × PN
Filling the System, Start-up ⓮
The return flow pressure ① must not
exceed the supply flow pressure ②.
DIN 17458,
Non-compliance may cause damages at the
DIN 2391
controller ③.
DIN 2391
1. Open shut-off devices ④ that are possibly
DIN 1754
available at the impulse tubes.
2. Slowly open valves in the system.
3. Slowly open shut-off devices ⑤ in the
supply flow.
4. Slowly open shut-off devices ⑥ in the return
flow.
Putting out of Operation
1. Slowly close shut-off devices ⑤ in the supply
flow.
2. Slowly close shut-off devices ⑥ in the return
flow.
Differential Pressure Setting ⓯
Set-point range see rating plate ①
1. Start-up of system, see section ⓮.
2. Set flow rate on a motorised valve ③ by
which the differential pressure is controlled,
to about 50 % ②
3. Adjustment
• Observe pressure indica t ors ④.
• Turning to the right ⑤ increases the set-
point (stressing the spring)
• Turning to the left ⑥ redu ces the
set-point (unstressing the spring)
4. The set-point adjuster ⑦ may be sealed.
80
250
630
25
25
16
District Energy