Dynabrade 50348 Посібник з експлуатації - Сторінка 2
Переглянути онлайн або завантажити pdf Посібник з експлуатації для Шліфувальна машина Dynabrade 50348. Dynabrade 50348 4 сторінки. 2 hp right angle disc sander
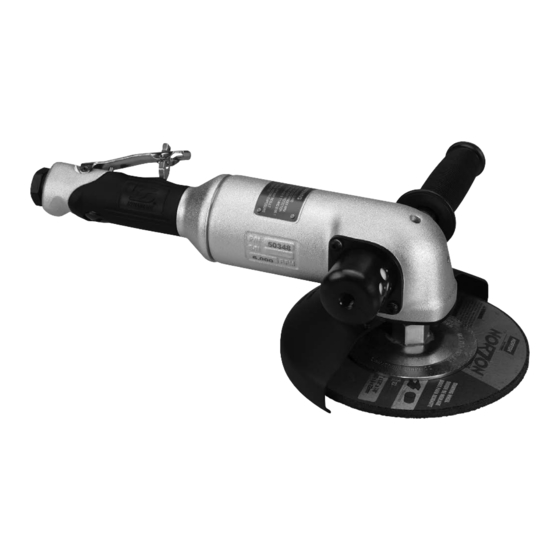
MAINTENANCE INSTRUCTIONS
Important: To keep tool safe, a Preventative Maintenance Program is
recommended. The program should included inspection of the tool and all related
accessories and consumables, including air lines, pressure regulators, filters, oilers,
etc. refer to ANSI B186.1 for additional maintenance information. If accessory or tool
breakage occurs, investigate failure to determine the cause and correct before
issuing tool for work. Use the following schedule as a starting point in developing a
Preventative Maintenance Program. If tool does not operate properly (RPM,
Vibration, Start/Stop) after these scheduled checks or at any time, the tool must
be repaired and corrected before returning tool to use.
INSTALLATION
• To ensure long life and dependable service, use a Closed Loop Air System
and Filter-Regulator-Lubricator as diagramed below.
• Each tool should have its own dedicated hose connected to an air supply
manifold. Quick disconnects should be installed at the manifold in an effort to
reduce contamination into the tool.
• It is strongly recommended that all Dynabrade rotary vane air tools be used
with a Filter-Regulator-Lubricator to minimize the possibility of misuse due to
unclean air, wet air or insufficient lubrication. Dynabrade recommendsthe
following: 10690 Air Line Filter-Regulator-Lubricator — Provides accurate air
pressure regulation, two-stage filtration of water contaminants and micro-mist
lubrication of pneumatic components.
• Dynabrade recommends one drop of air lube per minute for each 20 SCFM
(example: if the tool specification states 40 SCFM, set the drip rate on the
filter-lubricator to 2 drops per minute) Dynabrade Air Lube
(P/N 95842: 1pt/473ml) is recommended.
MAINTENANCE SCHEDULE
Daily (every 8 hours):
• Inspect tool and accessories for damage or broken parts.
Replace items as necessary to ensure proper operation and safety.
• Lubricate motor as recommended. Use Dynabrade Air Lube (P/N 95842:
1pt/473ml) 10W/NR. (1 Drop per minute of air lube per 20 SCFM.)
• Check air line pressure with a gage. (MAX. 90 PSIG or 6.2 Bar operating
pressure at the air inlet of the tool.)
• Right angled gear and wick system through gear case grease fitting with
3 plunges of gear oil (P/N 95848) and grease gun (P/N 95541).
(Prime grease gun prior to greasing.)
• Check tool for proper operation: If operating improperly or demonstrates
unusual vibration, the tool must be serviced and problem corrected before
further use.
Every 20 Hours or Once a Week Which Ever Comes First:
• Check free speed of tool without the abrasive accessory mounted. Measure
RPM (speed) with tachometer and with air pressure set at 90 PSIG while the tool
is running. If a governed tool is operating at a higher speed than the RPM
marked on the tool housing, the tool must be serviced and corrected before use.
A non-governed tool may exceed the RPM marked on the tool by 10% when
operated at free speed with no accessories.
• If tool is running fast look for worn, damaged or missing governors, air control
rings and silencers. Special care must be taken when servicing governors and
speed control devices. Injection molded governor assemblies are non-
serviceable and must be replaced.
• If tool is running slow look for clogged inlet screen, air stream, silencer(s) or a
malfunctioning governor(see concerns for servicing governors).Service as required.
Every 50 Hours:
• Lubricate planetary gears through gear case grease fitting
with 3 plunges of grease (P/N 95542) and grease gun (P/N 95541).
(Prime grease gun prior to greasing.)
REPAIR
• Use only genuine Dynabrade replacement parts to ensure quality. To order
replacement parts, specify Model#, Serial# and RPM of your air tool.
• Mineral spirits are recommended when cleaning the tool and parts.
Do not clean tool or parts with any solvents or oils containing acids, esters,
ketones, chlorinated hydrocarbons or nitro carbons.
• DO NOT clean or maintain tools with chemicals that have a low flash point
(example: WD-40
®
).
• A Motor Tune-Up Kit is available which includes high wear and medium wear
motor parts.
• Air tool markings must be kept legible at all times, if not, reorder housing and
replace. User is responsible for maintaining specification information.
• After maintenance is performed on tool, add a few drops of Dynabrade
Air Lube (P/N 95842) to the tool inlet and start the tool a few times
to lubricate air motor. Verify RPM (per 20 hr maintenance schedule),
vibration and operation.
HANDLING & STORAGE
• Use of tool rests, hangers and/or balancers is recommended.
• Protect tool inlet from debris (see Notice).
• DO NOT carry tool by air hose or near the tool throttle lever.
• Store accessories in protective racks or compartments to prevent damage.
• Follow the handling instructions outlined in the operating instructions when
carrying the tool and when changing accessories.
• Protect accessories from exposure to water, solvents, high humidity,
freezing temperature and extreme temperature changes.
END OF USE / DISPOSAL
When tool has reached its end of useful service, disassemble tool into its
primary components (i.e. steel, aluminum and plastic part) and recycle or
discard per local, state and/or federal regulations as to not harm the environment.
NOTICE
All Dynabrade motors use the highest quality parts and metals available and
are machined to exacting tolerances. The failure of quality pneumatic motors
can most often be traced to an unclean air supply or the lack of lubrication.
Air pressure easily forces dirt or water contained in the air supply into motor
bearings causing early failure. It often scores the cylinder walls and the rotor
blades resulting in limited efficiency and power. Our warranty obligation is
contingent upon proper use of our tools and cannot apply to equipment
which has been subjected to misuse such as unclean air, wet air or a lack
of lubrication during the use of this tool.
DISASSEMBLY/ASSEMBLY INSTRUCTIONS
IMPORTANT: The manufacturer's warranty is void if the tool is
disassembled before the warranty expires.
NOTICE: All of the special repair tools referred to in these instructions can
be ordered from Dynabrade Inc. Please refer to the parts page for proper
part identification.
RIGHT ANGLE AND MOTOR DISASSEMBLY
1. Shut the air supply valve and disconnect the disc grinder from the air supply hose.
2. Remove the 07139 Flange with the 95051 Hex Key (3/8").
Remove the Type 27 Wheel and the 52176 Back-Up Flange.
3. Remove the 52169 Handle.
4. Use the 95331 Hex Key (4mm) to remove the 95897 Screws (5),
and the 52149 Guard from the 52146 Housing.
5. Pull the 52131 Spindle along with the associated components out of the 52146 Housing.
6. Hold the 52146 Housing in a vise with aluminum or bronze jaws by holding
the housing between the handle mounting boss & the 52164 Exhaust Cover.
7. Roll back the 07136 Grip to expose the wrench flats on the 52123 Adapter.
Use the 96079 Wrench (32mm) or an adjustable wrench to remove the 52123
Adapter from the 52146 Housing by turning it counterclockwise.
8. Pull the motor assembly out of the 52146 Housing.
9. Very carefully hold the pinion gear stationary in the aluminum of bronze jaws.
Use an adjustable wrench to remove the governor assembly by turning it
clockwise. (Left Hand Threads)
10. Fasten the 96346 Bearing Separator (2") around the portion of the 52139
Cylinder that is closest to the 52140 Bearing Plate.
11. Position the motor assembly with the separator in the 96232 Arbor Press (#2)
so that the pinion is pointing down.
Note: Use additional blocking under the bearing separator to provide clearance
for disassembling the air motor.
12. Use a 3/16" dia. flat end drive punch as a press tool along with the arbor press
to push the rotor out of the 01266 Bearing.
13. Use the 96214 Bearing Removal Tool to remove the 01266 Bearing from the
52140 Bearing Plate.
14. Remove the 95998 Retaining Ring from the pinion gear. Position the flat side
of the bearing separator toward the gear teeth and fasten it to the pinion gear.
Place the bearing separator along with the remaining motor components in the
arbor press so that the pinion gear is pointing up.Use a 1/4" dia. flat end drive
punch to push the 07108 Rotor out of the pinion gear.
15. Remove the 52136 Bearing Plate, 52184 Bearing and the 52141 Shims from the rotor.
16. Use a 1/4" dia. flat end drive punch to remove the 50497 Washer and the 02649
Bearing from the 52146 Housing.
17. Hold the flats on the 52131 Spindle in the vise with aluminum or bronze jaws
and use an adjustable wrench to remove the 52118 Spindle Nut by
turning it counterclockwise.
18. Use the bearing separator and the arbor press to remove the 50505 Bearing
and the bevel gear.
Right Angle and Motor Disassembly Complete.
VALVE DISASSEMBLY
1. Remove the 07147 Plug by turning it counterclockwise.
2. Remove the 07146 Packing, the 07145 Spring, and the 07168 Valve Stem Assembly.
3. Remove the 01017 Pin and the 01089 Safety Throttle Lever.
Valve Disassembly Complete.
MUFFLER DISASSEMBLY
1. Use the 95266 Hex Key (3mm) to remove the 50511 Screws (2),
01791 Washers (2), 52180 Clamp and the 52164 Exhaust Cover.
2. Remove the 55245 Felt Silencer and the 52165 Gasket.
Muffler Disassembly Complete.
Clean and inspect all parts before assembling.
MUFFLER ASSEMBLY
1. Install the 52164 Gasket onto the 52146 Housing.
2. Install the 52167 Felt Silencer into the 52164 Exhaust Cover and attach these to
the 52146 Housing with the 52180 Clamp,50511 Screws (2) & the 01791 Washers (2).
Muffler Assembly Complete.
VALVE ASSEMBLY
1. Install the 07146 Packing onto the 07147 Plug.
2. Insert the 07145 Spring into the 07168 Valve Stem Assembly and install
these into the 07141 Valve Body.
3. Hold the valve components in place with the 07147 Plug.(Torque to 17 N•m/150 in. lbs.)
2
(continued on page 4)