Miller 900 860 Посібник із швидкого старту - Сторінка 8
Переглянути онлайн або завантажити pdf Посібник із швидкого старту для Зварювальна система Miller 900 860. Miller 900 860 15 сторінок.
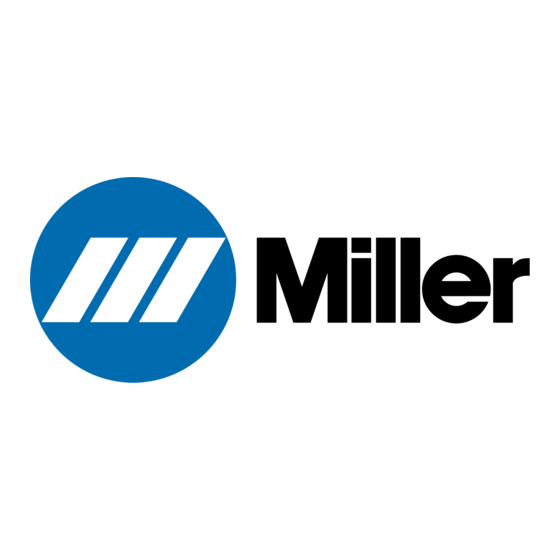
SECTION
4-
FUNCTION
OF CONTROLS
4-5.
CONTACTOR
CONTROL
RECEPTACLE
(Figure
4-1)
Whenever
a
Remote Contactor
Control
is
to
be
used,
make
connections
to
the
CONTACTOR CONTROL
Receptacle
on
the
welding
power
source
as
instructed
in item
3-5.
In order
for
a
Remote Contactor
Control
to
operate the
contactor
in
the
welding
power
source,
the
Remote Contactor Control
must
be able
to
supply 115
volts
ac
to
the
CONTACTOR
CONTROL
Receptacle
whenever weld
output
is
desired.
Also,
whenever suspension
of weld output
is
desired,
the
Remote Contactor
Control
must
be able
to
cut-off the 115
volts
ac
supply
to
the
receptacle.
NOTE
A
thermostat
is
connected
in
series with the
con
tactor
coil in order
to
provide
overload
protection.
Should
an
overload condition
occur,
the
thermostat would
open
and thus
cause
the
contactor
to
drop
out
and
suspend
weld output.
Once the thermostat has
opened,
it will
not
be
possible
to
energize
the
contactor
until
the-
welding
power
source
has cooled
to
a
proper tempera
ture.
Usually
a
five minute
idling period
is
a
sufficient
period-of
time
for
the
welding
power
source
to
cool in
order
to
permit
the
thermostat
to
close.
Figure
4-1. Front Panel View
Placing
the POWER Switch
in
the ON
position
will
energize
the
welding
power
source
fan and control
circuitry
and
place
the
welding
power
source
in
a
ready-to-weld
status.
Placing
the POWER
Switch
in
the OFF
position
will shut the
welding
power
source
down.
Even
though
the POWER
Switch
is in
the OFF
posi
tion
and
the
welding
power
source
is
apparently
elec
trically
shut
down,
electrical
input
power
is
still
present
on
all
circuitry
up
to
the POWER
Switch.
To
completely
cut-off all electrical
power
to
the
welding
power
source,
it will
be necessary
to
place
the line
disconnect switch
in
the OFF
position
or
remove
the
inputcircuitfuses.
The
Range
Switch
provides
the
capability
of
being
able
to
select from five
coarse
open-circuit voltage
ranges. The maxi
mum
open-circuit voltage
that
can
be
obtained
from each
switch
position
is
displayed
on
the
welding
power
source
nameplate.
chan ge the
pos
in
A
an
ge
Switch while
welding
or
under load
as
this will
cause
the
contacts
of
the switch
to
arc.
Arcing
across
the
contacts
will
cause
the
contacts~to
become
pitted
and
thereby eventually
to
become
inoperative.
4-3.
VOLTAGECONTROL(Figure4-1)
The
Voltage
Control
provides
the
capability
of
being
able
to
select the desired
open-circuit voltage
within the entire range
of the
welding
power
source.
Rotating
the
Voltage
Control
in
a
clockwise direction will increase the
open-circuit voltage.
4-4.
OPEN-CIRCUIT VOLTS INDICATOR
(Figure
4-1)
An
indicator,
labeled
OPEN-CIRCUIT
VOLTS,
is
provided
on
the front
panel
to
display
the open-circuit
voltage
selec
ted. The
reading
on
the OPEN-CIRCUIT VOLTS Indicator
will
change
when the
Voltage
Control
is
rotated.
4-6.
METERS
(Figure
4-1)
The
welding
power
source
is
equipped
with
a
dc
ammeter
and
a
dc voltmeter. These
meters
are
internally
connected
to
the
welding
power
source
output
welding
terminals. The volt
meter
will
indicate
the dc
voltage
at
the
secondary
terminals,
but
will
not
necessarily
indicate
the actual
voltage
at
the
welding
arc.
If the
welding
cables
are
excessively long,
or
have
poor,
loose
connections,
the difference
between actual
arc
voltage
and
the
voltage
at
the
welding
power
source
secondary
terminals may be considerable,
4-7.
DUTY CYCLE
(Figure
4-2)
zuutJ
Welding
power
sources
are
rated
on
a
percent
duty cycle
based
on
10
minute
intervals.
For
example:
A
60
percent
duty
cycle
simply
means
that the
welding
current
is off for 4
minutes,
on
again
for 6
minutes,
and
so
on.
It
must
be
kept
in
mind that
time
intervals of other than
10 minutes
will
yield
different
test
rating
results. As the output
is reduced
or
increased,
the
duty
cycle
will increase
or
decrease.
Figure
4-2 enables the operator
to
determine the safe output
of the
welding
power
source at
various
duty cycles.
,.,~&p
.....
,~5-0L_j_
E
1000
~__E
E E E
I I
u~j
icnn
1~sn
-~
r
~-
DC
Voltmeter
DC Ammeter
\
Fuse
F2
Range
Switch
Open-Circuit
Volts
Indicator
Voltage
Control
Power Switch
115 Volts AC
Duplex
Receptacle
115 Volts
AC
Twit
tlock
Receptacle
tactor
Control
Receptacle
TB-039
388
Negative
Secondary
Terminal
PositIve
Secondary
Terminal
I
I
4-i.
POWER
SWITCH
(Figure
4-1)
U
I
4-2.
RANGE SWITCH
(Figure
4i)
IMPORTANT
Exceeding
the
indicated
duty cycle
will
cause
the
welding
power
source
to
overheat
thereby causing
damage
to
the
welding
power
source.
LU
LU
0~
5
(3
0
-J
LU
0
15
20
25
30
%DUTY CYCLE
40
50
60
70 80
100
Figure
4-2.
Duty Cycle
Chart
Page
8