DIS Sensors CAN Посібник користувача - Сторінка 8
Переглянути онлайн або завантажити pdf Посібник користувача для Аксесуари DIS Sensors CAN. DIS Sensors CAN 18 сторінок. Inclination safety sensor
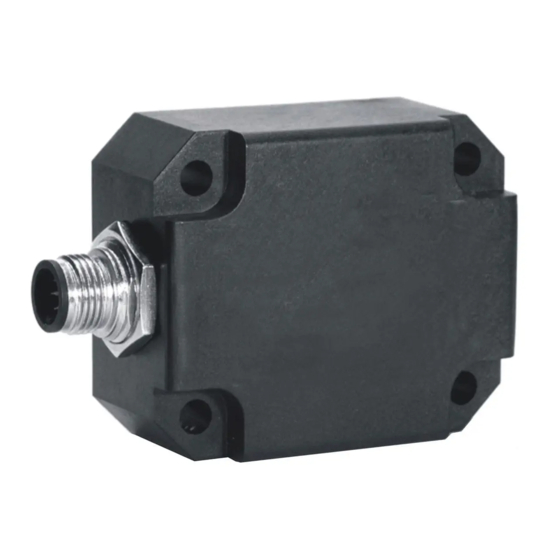
CAN User Manual
Inclination Safety Sensor
(Type D) V2.0
8.6 Accelerator element tolerance
The sensor consists of two accelerator elements. The acceleration values of these elements are converted to
angles. These angles are compared and a safe state is set when the elements differ too much. To prevent for
false alarms, a tolerance can be configured. The tolerance consists of allowing an angle deviation during a certain
time.
These values are adjustable via object 4006h sub- index 01h and 02h. The default values are 300d and 200d ( 3°
during 2000 ms). The actual values used by the customer should fit the application involved. Before using this
sensor and with the settings chosen the customer should evaluate risks in order to check whether the chosen
settings satisfies his safety requirements. Manufacturer is not responsible for any damage caused by these
customer-setting, even when the manufacturer defaults are used.
Definitions for the Redundancy error:
'Redundancy Compare time' (user programmable, default 2000ms)
'Redundancy Compare angle' (user programmable, default 3°)
8.7 Output invalid
A vertical device measures the angle relative to the gravity. When a device is tilted towards the horizontal plane
for more than 45°, the angle can't be accurately measure because the gravitation vectors become shorter. In this
case the output is set to 200°. This value indicates that the output is invalid.
For horizontal devices the same principle is valid. When the longitudinal axis is greater than 45 degree the output
for lateral axis is set to 200°. When the lateral axis is greater than 45° the longitudinal is set to 200°. The output is
also invalid when the range limits are reached. Example when angle is 32° for a ±30 device the output is limit to
±30°. For a ±90 device the angle is limited to ±90°.
8.8 Writing objects
When writing an object it can have a major influence on the output. To prevent unauthorized changes most write
action can only be executed when the device is in pre-operational state. According to EN 50325-5
8.9 Changing SRDO1 settings
When changing an SRDO1 setting the sensor must be in pre-operating state.
The direction 1301h sub id 01h must be disabled by writing 00h to object 1301h sub id 01h.
When the SRDO setting is changed the CRC code must also be changed and activated. Finally the data must be
stored in EEPROM
Example to change SRDO1 refresh time
Load object:
1301h sub id 01h with:
Load object:
1301h sub id 02h with:
Load object:
1301h sub id 01h with:
Load object:
13FFh sub id 01h with:
Load object:
13FEh sub id 00h with:
Load object:
1010h sub id 01h with:
validation to EEPROM.
After a power reset and when the device is set to operational, the transmission time is equal to the desired time.
00h
disable SRDO1 communication.
0064h new SRDO1 refresh time.
01h
enable transmit SRDO1 communication.
xxxxh
code from CRC calculation tool.
A5h
validate new CRC.
"save" or 65766173h
write new SRDO1 refresh time, CRC and
Page 8 of 18