cashco C-PRV Panduan Pemasangan, Pengoperasian & Pemeliharaan - Halaman 4
Jelajahi secara online atau unduh pdf Panduan Pemasangan, Pengoperasian & Pemeliharaan untuk Pengontrol cashco C-PRV. cashco C-PRV 9 halaman. Pressure reducing regulator
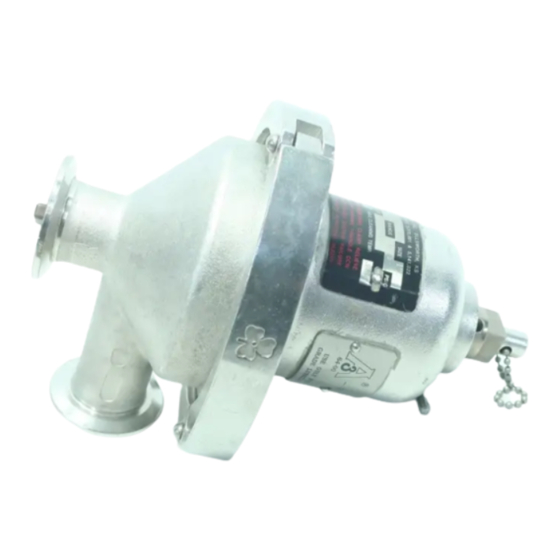
For 1" Investment Cast Body:
a. Install spacer (21).
b. Apply medium strength, Food Grade
threadlocker set screw (24). Thread set
screw into adapter nut (20) secure tight
to "flat" on plug (17).
c. Apply Emhart Bostic White Food Grade
"Never Seeze" or equivalent to the
external threads of the adapter (20) and
thread guide post (18) securely to the
adapter.
22. Thread guide post (18) onto end of plug (17),
tighten firmly into place.
23. Apply medium strength, Food Grade
threadlocker to set screw (19). Thread set
screw tight into guide post (18).
24. Position spring (7) over guide post (18) - resting
flat on pressure plate (3).
25. Place spring button(4) with adjusting screw
assembly (5) and bearing (22) down over guide
post (18) into spring (7) cavity. Align one tab
(ear) on spring button (4) directly above tab
slot cut into the body flange lip.
NOTE: Apply a small amount of Emhart
Bostic White Food Grade "NEVER-SEEZ
equiv a lent to threads of ad just ing screw (5) .
26. Align the two ribs inside the spring chamber
(2) with the tabs (ears) on the spring button
(4) and place the spring chamber (2) over
assembled parts directly on body (1). Refer to
step 6 previous for alignment of match marks
for final orientation.
VII. CLEANING PROCEDURE
A. Pre-Sanitation:
1. Owner should refer to owner's op er at ing
pro ce dures for system shutdown to include
re liev ing all system pres sure.
2. Refer to Figure 3 for item number reference ().
3. Remove the lock-open pin (10) from the pin
retainer hole in the spring cham ber (2). (See
Figure 2.)
4
27. Position the Tri-Clamp (13) around the mating
flanges of the body (1) and the spring chamber
(2) with the threaded fastener aligned with
the tab slot cut in the body flange lip. Clamp
should be tightened to approximately 4 to 6
ft-lbs.
halves around the mating flanges of the body
(1) and the spring chamber (2). Insert clamp
bolts (13C), wash ers (13D) and tighten clamp
nuts (13B) in alternating pattern. The clamp
should be tightened to approximately 4 to 6
ft-lbs or 18-20 ft-lbs for Gylon Diaphragms.
NOTE: Gap be tween clamp (13A) halves should
be equal in size. See Figure 1.
Figure 1: Clamp Arrangement.
28. Place nut or handle (6) onto square end of
adjusting screw assembly (5).
" or
®
29. Insert hitch pin (15) through hole near the top
of the guide post (18). Apply medium strength,
Food Grade threadlocker to set screw (27)
and secure tight into the top of the guide post
(18).
30. Return to Section II. for Installation, Section
IV. for Start-up, and Sec tion VII for cleaning
procedure.
SECTION VII
4. System internal pressure must be at/near 0
psig (0 Barg). This will ensure plug (17) is
fully open. NOTE: Do not change range
spring (7) setting by rotating nut or handle
(6).
5. Insert pin (10), jostle nut or handle (6) lift up
or push down to secure pin (10) thru ad just ing
screw (5).
a. For Opt.-80: Position the clamp (13)
IOM-C-PRV