Danfoss VLT HVAC Drive FC 102 Instruction Manual - Page 12
Browse online or download pdf Instruction Manual for Controller Danfoss VLT HVAC Drive FC 102. Danfoss VLT HVAC Drive FC 102 16 pages. Igbt module replacement for d1h–d8h drives
Also for Danfoss VLT HVAC Drive FC 102: Operating Manual (16 pages), Installation Manual (20 pages), Installation Instructions Manual (6 pages), Installation Instructions Manual (12 pages), Installation Manual (18 pages), Installation Instructions Manual (11 pages), Installation Instructions Manual (8 pages), Installation Instructions Manual (10 pages), Installation Manual (6 pages), Operating Instructions Manual (16 pages), Installation Instructions Manual (6 pages), Installation Manual (16 pages), Installation Manual (8 pages), Installation Instructions Manual (6 pages), Installation Manual (6 pages)
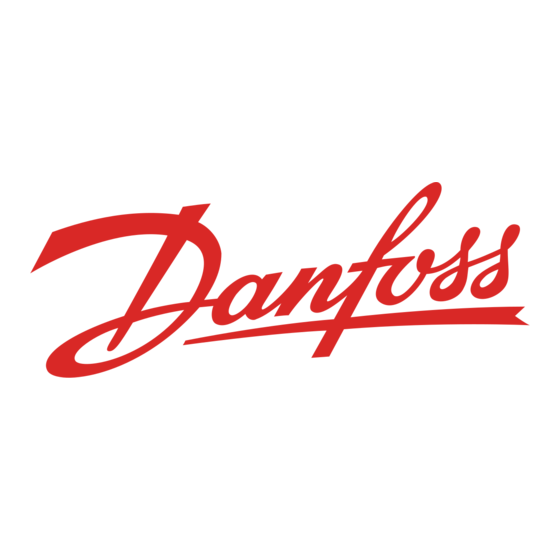