Dynacut MDM Operation Manual - Page 14
Browse online or download pdf Operation Manual for Lubrication systems Dynacut MDM. Dynacut MDM 17 pages. Minimum quantity lubrication system for external lubrication
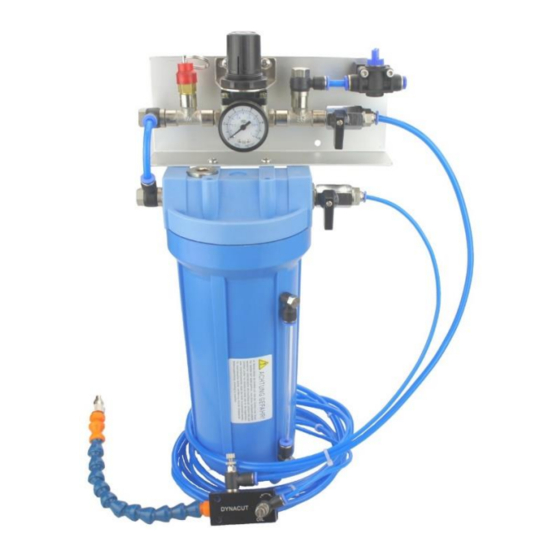
Default
The adjustment of the valves depends on all process parameters such as cutting speed,
materials, cutting tool, etc. and must therefore be re-adjusted on a case by case basis by the
machine operator.
The basic setting of the systems is as follows:
Open main valve for air.
Adjust the operating pressure via the pressure reducing valve (7 Fig. 2) depending on viscosity
to 0.2 - 1.5 bar.
Open hand valve for atomizer air (9 Fig. 2).
Open hand valve for coolant (10 Fig. 2).
Adjust the necessary lubricant quantity via the lubricant control valve (2 Fig. 1).
Adjust the carrier air quantity and thus the pressure via the atomizer air valve (5 Fig. 1).
Check the settings
Point the spray nozzle onto the cutting edge of the standing tool and observe if a lubricant
film is formed. If necessary, increase the amount of lubricant or atomizing air.
The distance between the spray nozzle and the tool tip should be kept as low as possible. If
the distance is too long, the tool cutting edge is not sufficiently lubricated.
Note: The larger the distance, the greater the spray angle of the spray nozzle.
Start machining and adjust the aerosol quantity and the aerosol composition to the machining
process by using criteria such as lubricant, cutting parameters, surface roughness and tool
wear to change the setting.
We recommend that you use test runs to determine and optimize the setting values required
for your application in order to get the best result for your machining process.
If necessary, use two spray nozzles, which are arranged at an angle of 180 ° to optimize the
aerosol supply to the lubrication point.